In de reeks ‘Hoe maakt u het?’ trekken we telkens naar een bedrijf in de motorbranche om uit te zoeken hoe een product gemaakt wordt. Van banden tot uitlaten en van laarzen tot helmen leggen we de finesses van de productieprocessen bloot. Dit keer: een kijkje achter de imposante Kilometro Rosso.
Wie in de voorbije vijftien jaar van Milaan richting Bergamo reed over de A64 snelweg kon er ter hoogte van Stezzano niet naast kijken: de gigantische rode muur die als de ‘Kilometro Rosso’ te boek staat. “Je zou er de flank van een Formule 1-bolide in moeten zien, maar daarvoor heb je toch redelijk wat verbeelding nodig”, lacht Brembo-perswoordvoerster Monica Michelini als ze mij ontvangt. `
“Brembo was het eerste bedrijf dat zijn intrek nam in de Kilometro Rosso, een kennishub rond een voormalige fabriek van Hewlett Packard. Ondertussen hebben meerdere bedrijven ons vervoegd”, verduidelijkt Monica terwijl we de indrukwekkende inkomhal betreden. In de eindeloze gangen van het Brembo-gebouw aan de Kilometro Rosso staan de producten als visitekaartjes uitgestald. Van full-carbon remschijven voor de Formule 1 tot parkeerremmen voor elektrische auto’s en complete kits zoals Brembo die voor de motorindustrie aanbiedt.
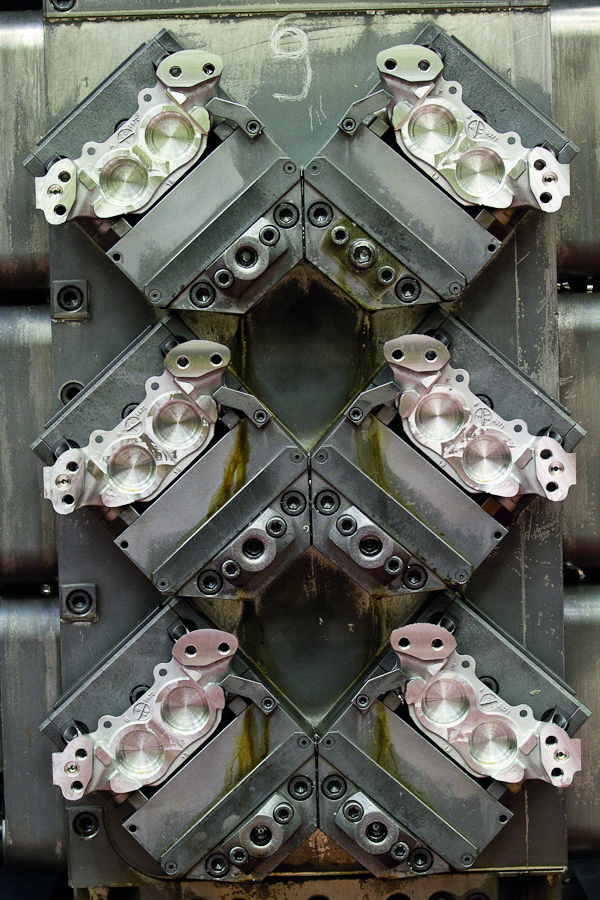
“We produceren remklauwen, hoofdremcilinders, koppelingshendels, remschijven en wielen. Al die producten bundelen we voor sommige fabrikanten zoals Ducati in complete kits. Ducati laat de banden bij ons leveren, waarna wij de banden en de remschijven op de wielen monteren. Ook de complete remsystemen bieden we per model kant-en-klaar aan: van rempomp tot remklauw en met het hele systeem meteen ontlucht en al. Dat scheelt de motorproducenten een hoop tijd in de productie”, legt Michelini uit.
De Brembo business kan je grofweg in drie stukken hakken: alles wat OEM (Original Equipment Manufacturer, red.) betreft zijn onderdelen die aan de motor-, auto-, of bestelwagenfabrikanten geleverd worden. Deze producten worden meestal in samenwerking met de auto- of motorconstructeur ontwikkeld. De tweede bedrijfstak concentreert zich op de onderdelen voor de racerij, hier wordt nauw samengewerkt met de teams. In de derde afdeling worden de onderdelen gemaakt waarmee elke motorrijder of autofreak zijn bolide kan upgraden.
Achter de rode muur van de Kilometro Rosso wordt er enkel aan productontwikkeling en testwerk gedaan. “Iets meer dan tweehonderd mensen zijn dagelijks bezig met het testwerk”, meldt Mauro Ialesi (verantwoordelijk voor de testafdeling) niet zonder de gepaste trots. Dat testwerk valt uiteen in drie luiken: het statische testwerk, het dynamisch testen en de tests op de weg.
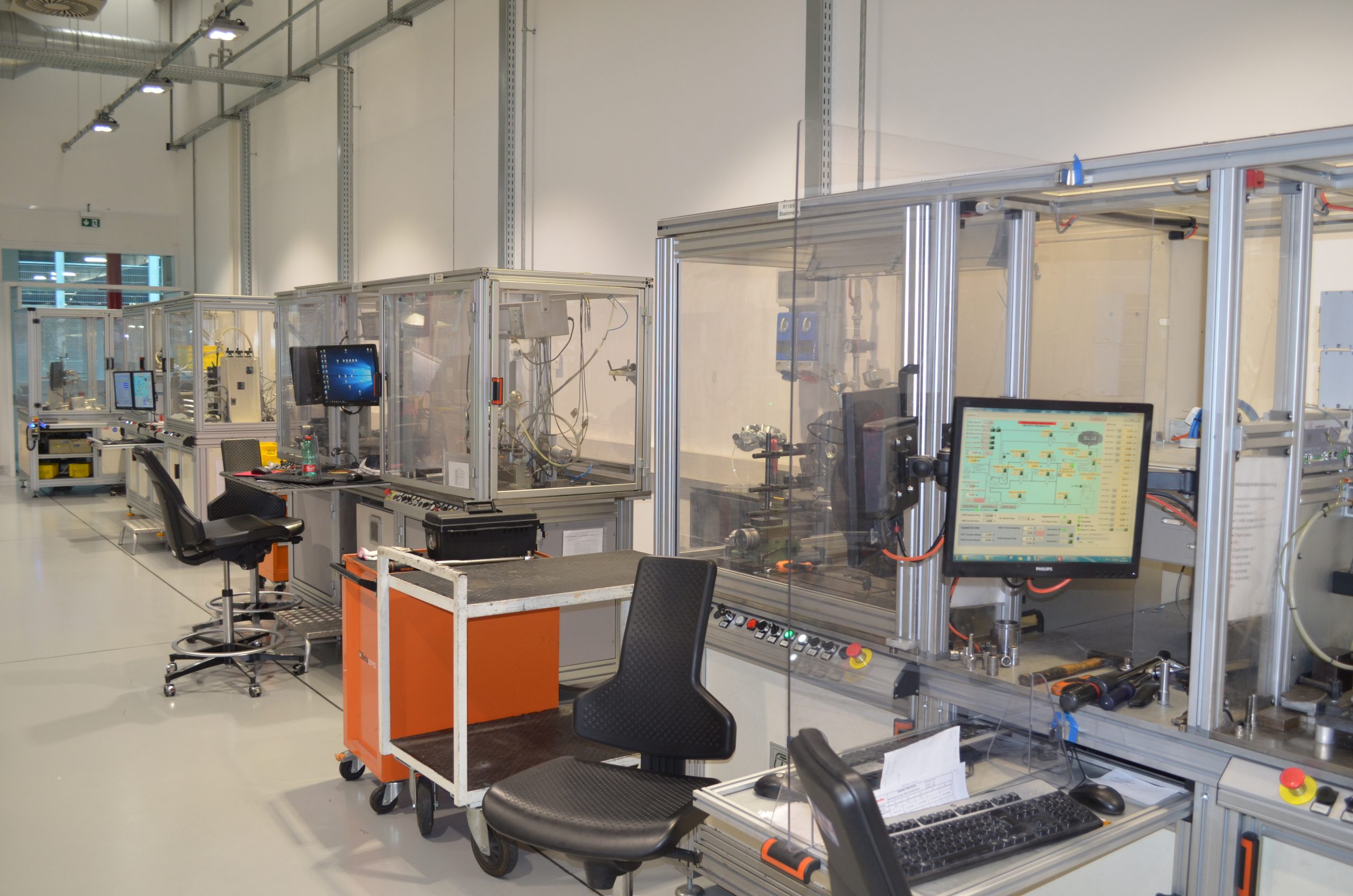
First things first: statisch testen. “Bij de ontwikkeling van een nieuw product gaan we eerst elk onderdeel haarfijn nameten om te checken of het product wel overeenkomt met de ontwerptekening. Bij een remsysteem gaan we dan op hoge en lage druk testen of er geen lekken zijn en om te kijken hoe de zuiger en de klauw daarop reageren. Een remsysteem kunnen we met lucht of met helium testen. Helium is nog fijner dan lucht, dus als er ergens een minimaal lek zit zal helium sneller ontsnappen dan lucht. We testen dat in een heel kleine ruimte waarin we een specifieke sensor voor helium zetten. Van zodra er een lek is, zal die sensor het ontsnapte helium opmerken en signaleren”, verduidelijkt Ialesi.
“We meten met laser de vervorming van een remklauw onder druk, zowel koud als heet. De stijfheid van een remklauw is essentieel als je een performant remsysteem wil ontwikkelen. We meten tot op een paar honderdsten van een millimeter of een remschijf wel mooi rond en vlak is. We kunnen indoor alle mogelijke weertypes simuleren om in sneltempo het verouderingsproces van een onderdeel in kaart te kunnen brengen. We meten hoeveel remhendels verbuigen onder druk en ga zo maar door”, zegt Mauro nog over het onderdeel ‘static testing’.
Zoals het echte wetenschappers betaamt test Brembo telkens slechts één parameter tegelijk. Op die manier weet je altijd wat er fout gaat en waarom het fout gaat. Test je in één cyclus meerdere productkenmerken tegelijk en gaat er wat mis, dan is het vaak gissen naar de oorzaak.
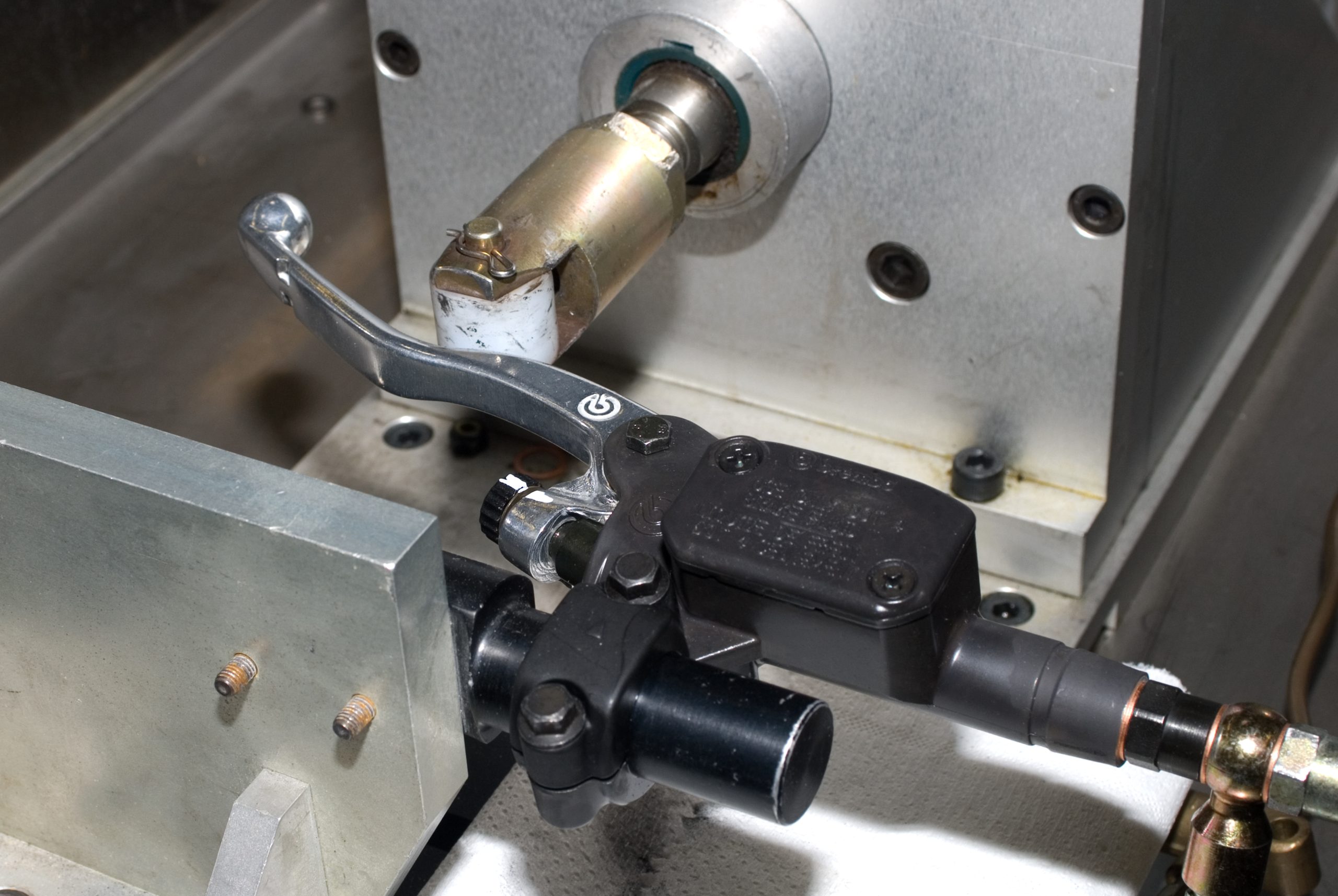
Voor de dynamische tests hebben Ialesi en co de beschikking over zomaar eventjes achttien testbanken, waarbij heel veel aandacht gaat naar de warmte die er ontstaat bij het remmen en hoe een remsysteem daarop reageert. Maar het leukste zijn uiteraard de tests op de weg. In de smetteloos witte garage staat vooraan een twintigtal motoren met in deel twee van de garage minstens evenveel exclusieve auto’s.
Een handvol motoren zit verstopt onder een Brembo-hoes, ik spot een paar auto’s met het typische krulletjesmotief van prototypes om te voorkomen dat je de vormen correct kunt inschatten. “De wegtesten van de OEM-producten doen we in samenspraak met de fabrikant van de motor, we krijgen daarvoor de motor dan uiteraard in bruikleen. Om na te gaan of een upgrade van een bepaald bestaand motortype met een Brembo remsysteem feilloos werkt, moeten we die motor soms zelf aankopen om alles degelijk te kunnen testen”, aldus Ialesi die alle resultaten van zijn testwerk deelt met de ingenieurs van Bybre (By Brembo), het Indische submerk van Brembo.
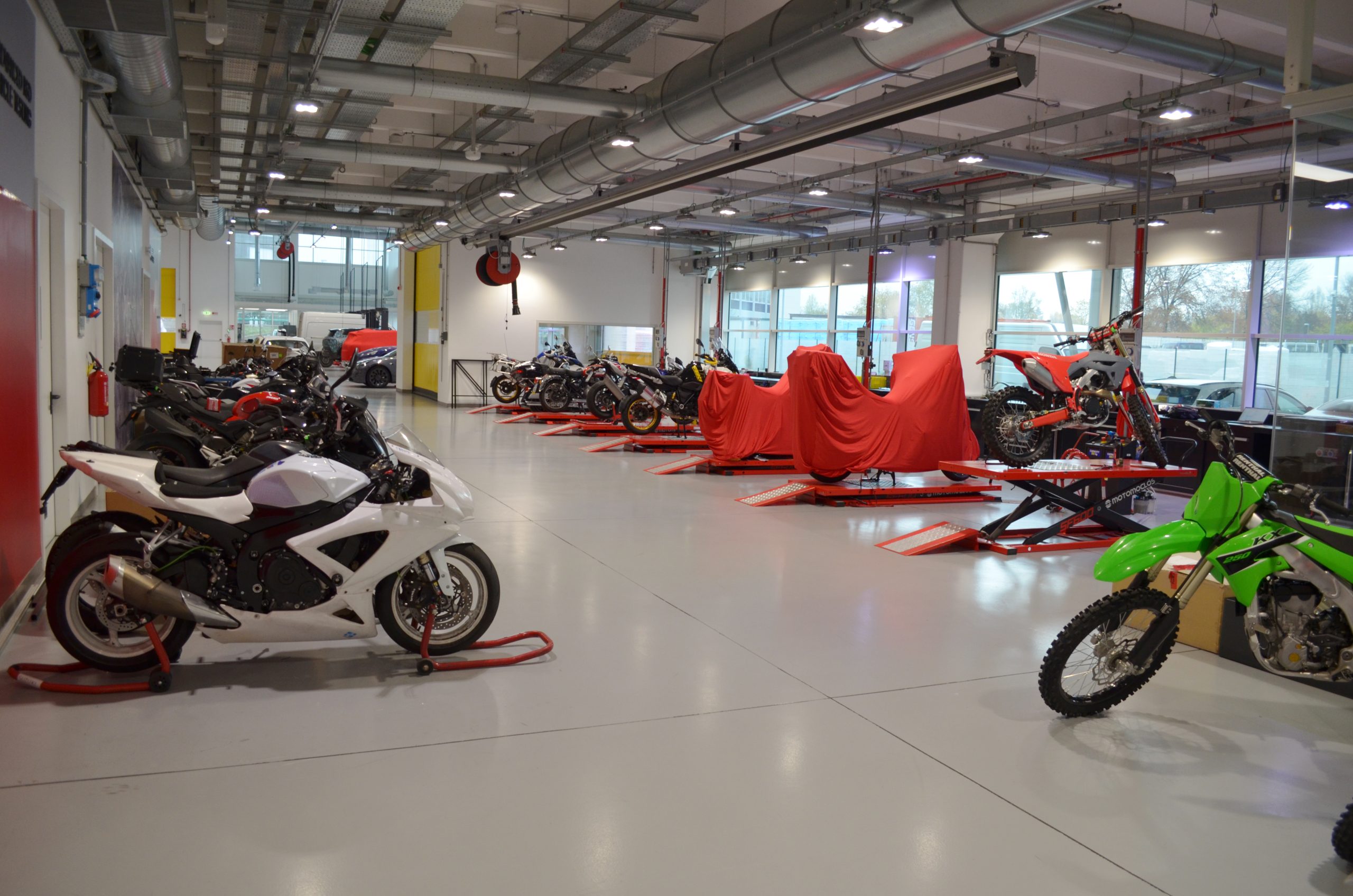
Een tiental kilometer van de Kilometro Rosso staat een van de grootste Brembo-fabrieken van Italië, opgedeeld in meerdere units. We beginnen in het deel van de fabriek waar de remklauwen, hoofdremcilinders en hydraulische koppelingshendels voor de motorfabrikanten geproduceerd worden.
Het gietwerk, het smeedwerk en walsen van het staal en de aluminium half afgewerkte onderdelen worden in een andere fabriek gemaakt; in Curno wordt enkel (nu ja, ‘enkel’, er werkt zeshonderd man) het freeswerk, de anodisatie en de montage van de onderdelen gedaan. Voor de OEM-onderdelen heeft productieleider Paleari 43 CNC-freesunits en 27 assemblagelijnen ter beschikking.
Het freeswerk kan met één of twee freeskoppen gebeuren, het frezen van de gaten in de monobloc remklauwen is een huzarenstukje dat ik niet mag fotograferen. Zo’n monobloc remklauw is aan de buitenkant gewoon dicht, maar binnenin moeten er wel gaten gefreesd worden voor de remzuigers. “In samenwerking met onze gereedschapsleverancier hebben we een unieke machine ontwikkeld waarmee we die gaten toch kunnen frezen. We zijn de enige remmenfabrikant ter wereld die over deze technologie beschikt”, meldt Paleari trots.
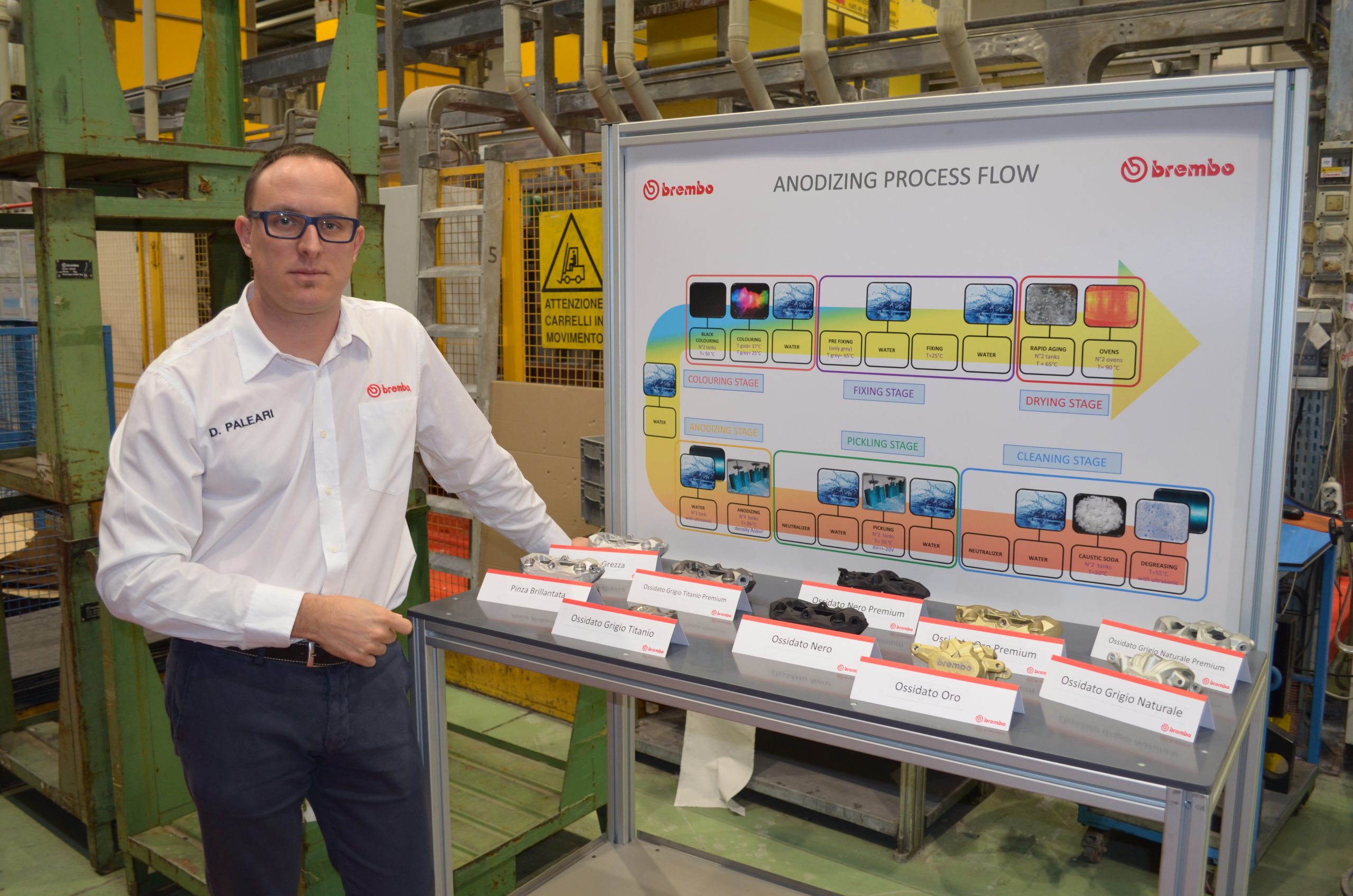
In de anodisatie-afdeling krijgen de onderdelen middels een chemisch proces een kleurtje (metaalkleur, titaniumgrijs, goud of zwart). Als de onderdelen geanodiseerd zijn, worden ze in sommige zones nagefreesd, bijvoorbeeld om de merknaam en het logo zichtbaar te maken. Heeft je Brembo-remklauw een gouden kleurtje en lijkt het merk er in zilver op te staan, dan betreft het een klauw die eerst goud is geanodiseerd waarna de frees een half millimetertje van de modelnaam heeft gehaald om die te doen glanzen. Staat het Brembo-logo er in het rood op, dan is dat er zowaar met de hand op geschilderd.
Bij de assemblage van elk product worden alle stappen gemonitord. Lampjes boven het gereedschap tonen het personeel welk stuk gereedschap ze moeten gebruiken, elke sleutel is op het juiste aanhaalmoment afgesteld. Nagenoeg alles wordt met de hand gemonteerd, simpelweg omdat verschillende kleine rubber onderdelen (dichtringetjes en dergelijke) te klein en te flexibel zijn om ze machinaal te monteren.
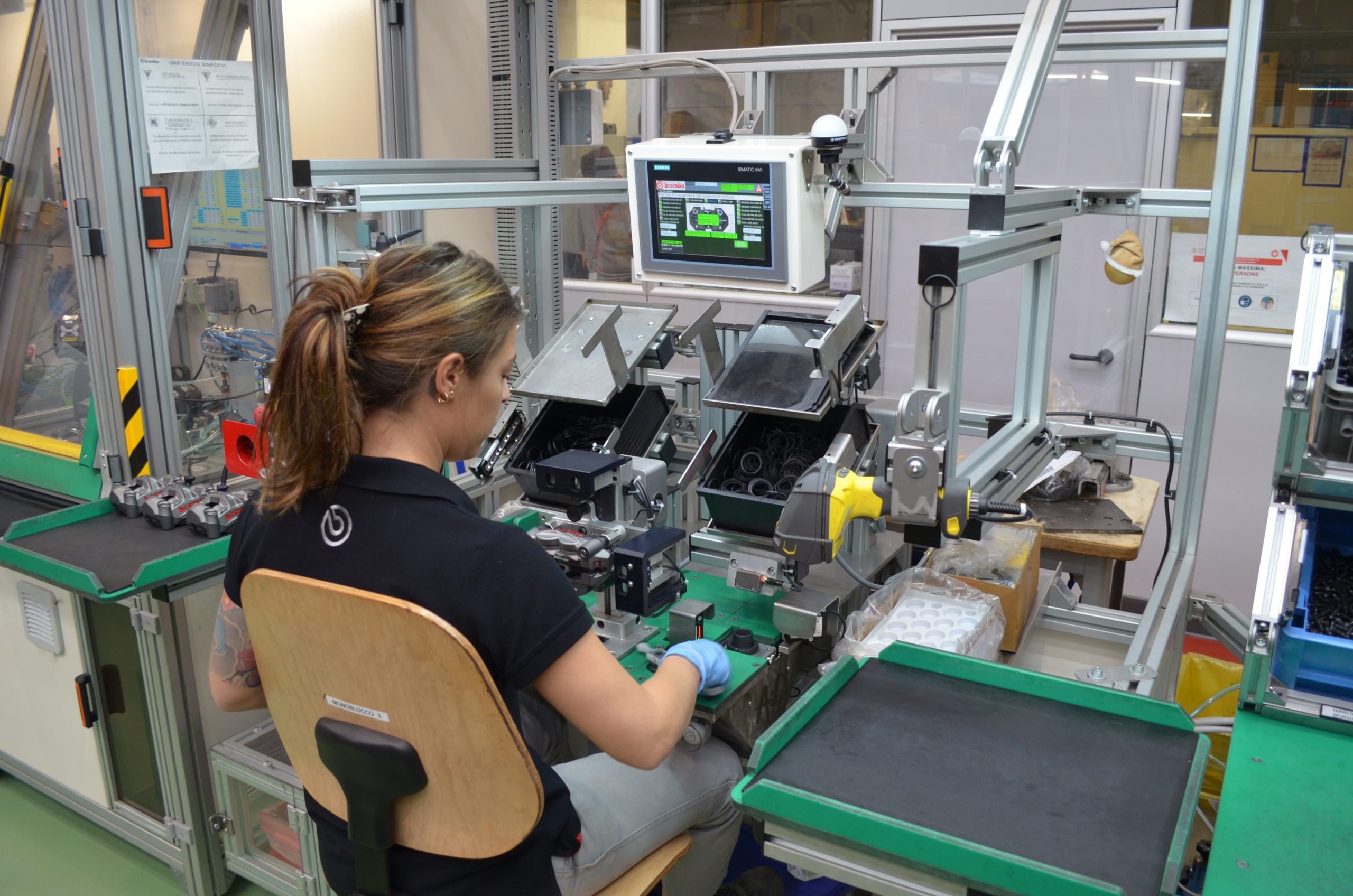
Zowel de hoofdremcilinders als de remklauwen worden allemaal op lage en hoge druk getest op lekken. De remklauwen die naar de motorfabrikanten gaan worden van remblokken voorzien en die worden meteen op een nep-remschijf gecentreerd, ook dat spaart de motorfabrikant in de montage weer tijd uit. Aftermarket remklauwen worden nooit met remblokken geleverd, die mag je er zelf bij zoeken in functie van je rijstijl. Sinds de overname van het Deense SBS heeft Brembo nu ook toegang tot remblokken van de hoogste kwaliteit, het Spaanse J.Juan werd dan weer gekocht vanwege de hoogwaardige remleidingen.
Ter afronding van het fabrieksbezoek mag ik nog even binnenkijken in de afdeling waar de upgrade-onderdelen en de racespulletjes gemaakt worden. Hier zijn de aantallen een pak kleiner, wordt er met veel kleinere assemblagelijnen gewerkt en wordt elk onderdeel tussen elke twee productie- of assemblagestappen met de hand gereinigd. En er is plaats voor speciallekes.
“We zijn bezig met het machinaal inremmen van de remblokken en remschijven voor de Dakar; die worden dan samen bewaard en opgestuurd. Superhandig voor de teams, ze kunnen die onderdelen gewoon monteren en de piloten kunnen de volgende dag met een gerust hart meteen volgas gaan”, vertelt Claudio Teoldi die de raceafdeling runt.
De remklauwen voor de MotoGP-machines worden hier in zachte mousse opgeslagen en verpakt. Tot in de puntjes perfect gefreesd uit billet aluminium. Ik mag wel informeren naar de prijs, maar krijg geen antwoord. “Laat ons zeggen dat de kostprijs hier veel minder belangrijk is dan de prestaties”, lacht Teoldi.
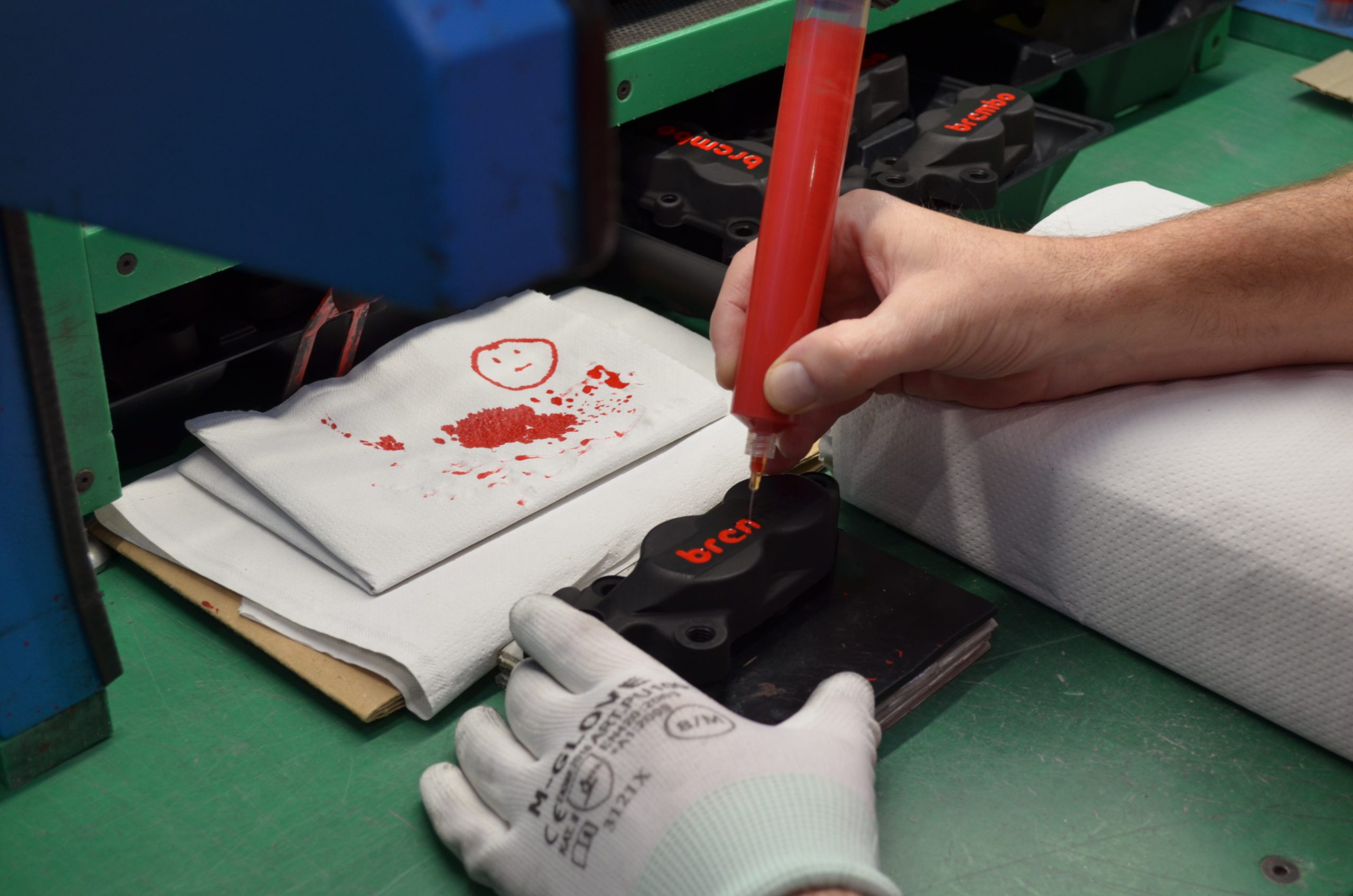
Al verbaas ik er mij twee units later wel over dat hier een pak remklauwen gereviseerd wordt. “De remklauwen die we in de racerij gebruiken zijn extreem duur. Na elke race worden ze naar ons teruggestuurd. Wij halen die remklauwen helemaal uit mekaar, vervangen de slijtage-onderdelen en sturen ze dan terug naar de renstal die ze opnieuw kan gebruiken, meestal voor testwerk in het tussenseizoen.” En niet dat al het basismateriaal dat ze bij Brembo gebruiken zo buitensporig duur is, maar al het metaal en aluminium dat bij de productie weggefreesd wordt, wordt wel verzameld om te recycleren en opnieuw te gebruiken.
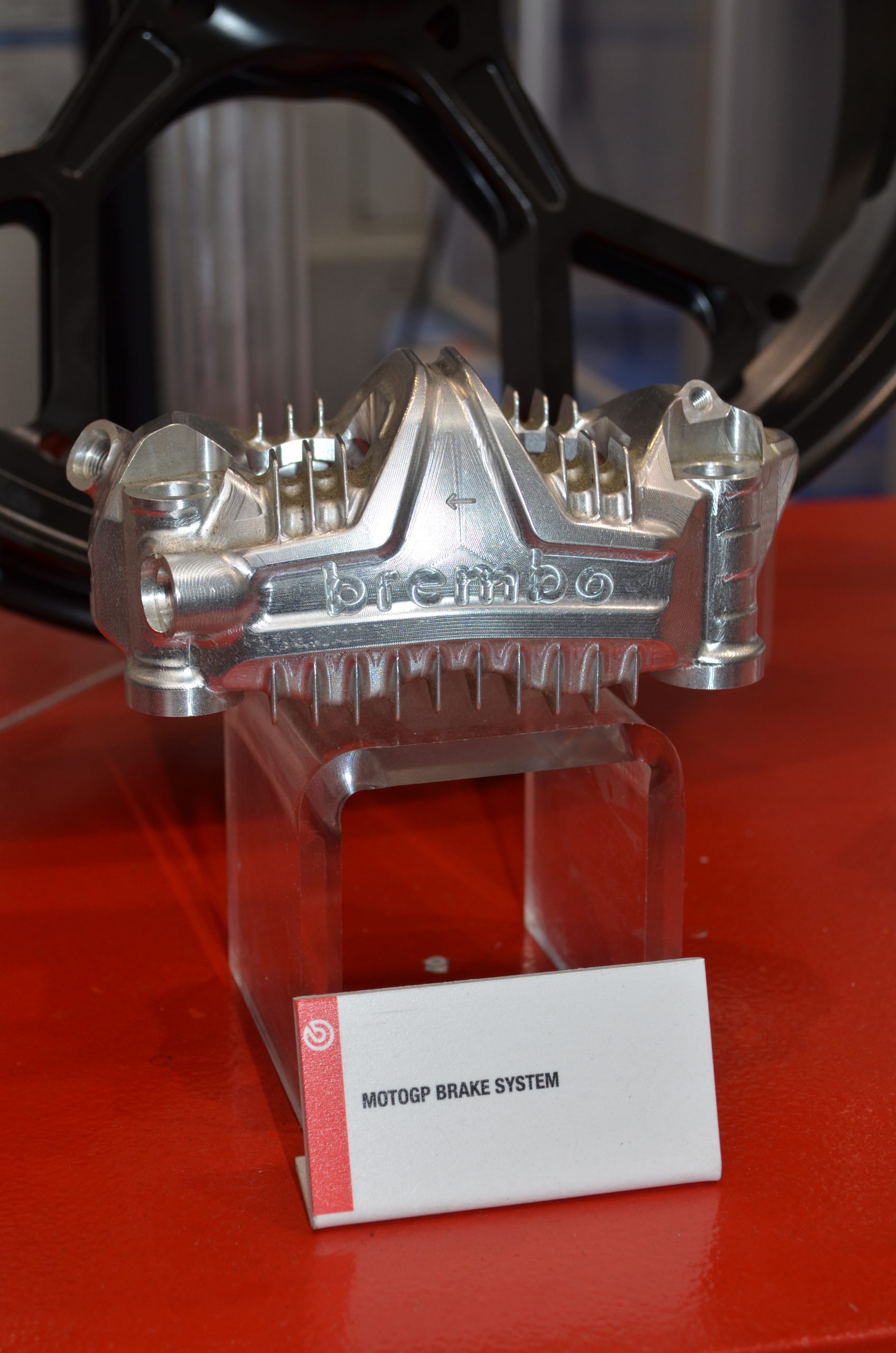
Tekst Bart De Schampheleire • Fotografie Brembo, Bart De Schampheleire