In de reeks ‘Hoe maakt u het?’ trekken we telkens naar een bedrijf in de motorbranche om uit te zoeken hoe een product gemaakt wordt. Van banden tot uitlaten en van laarzen tot helmen leggen we de finesses van de productieprocessen bloot. Dit keer: Alpinestars.
Hoewel Alpinestars via de crosslaars in de motorsport belandde, is het inmiddels ook een naam die staat als een huis in het racewereldje. Van de meest laagdrempelige trackday tot de MotoGP: overal kom je het logo tegen. De productie van de meeste Alpinestars producten wordt uitbesteed aan onderaannemers, maar al het test- en ontwikkelingswerk wordt nog in het Noord-Italiaanse Asolo uitgevoerd.
Rij je als motorliefhebber over de SP248 van Bassano del Grappa naar Montebelluna, dan spot je de ene bekende bedrijfsnaam na de andere. Gaerne, SiDi en Alpinestars zitten allemaal langs dezelfde provinciale weg. Stuk voor stuk ontstonden die beroemde merken toen hun oprichters wandelschoenen en laarzen begonnen te maken, waarna ze hun focus verlegden naar de motor- en wielersport. Alpinestars verging het net zo.
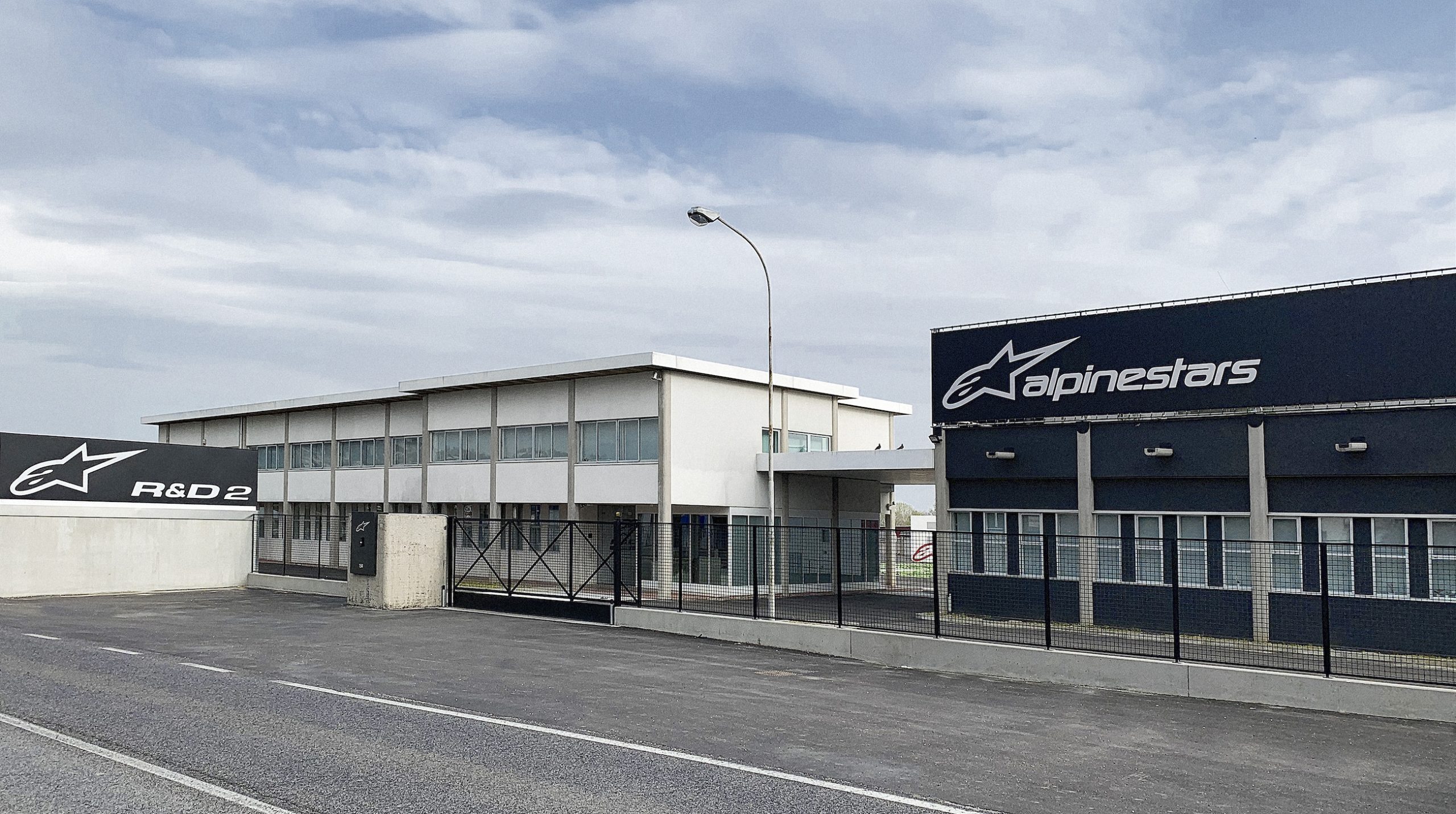
Sante Mazzarolo begon in 1963 in Asolo met de productie van wandelschoenen en bedacht er de naam ‘Alpinestars’ voor. Net in die periode begon motorcross zich als sport te ontwikkelen. Mazzarolo had al snel door dat er een markt was voor laarzen die aan de noden van de motorcrossers zouden voldoen en hij ontwikkelde de eerste motorcrosslaars die naam waardig. Het product werd meteen opgepikt door de rijders, waardoor het merk een vliegende start nam.
“Gabriele Mazzarolo, zoon van oprichter Sante, besefte evenwel dat het grote potentieel zich aan de andere kant van de Atlantische Oceaan bevond en dat Alpinestars dringend actief moest worden op de Amerikaanse markt. Gabriele opende in 1986 Alpinestars USA in Los Angeles en vanaf toen ging de bal internationaal aan het rollen”, zegt Gordon Casteller van de Alpinestars persdienst als we van het hoofdkwartier in Asolo naar de productie in Maser rijden.
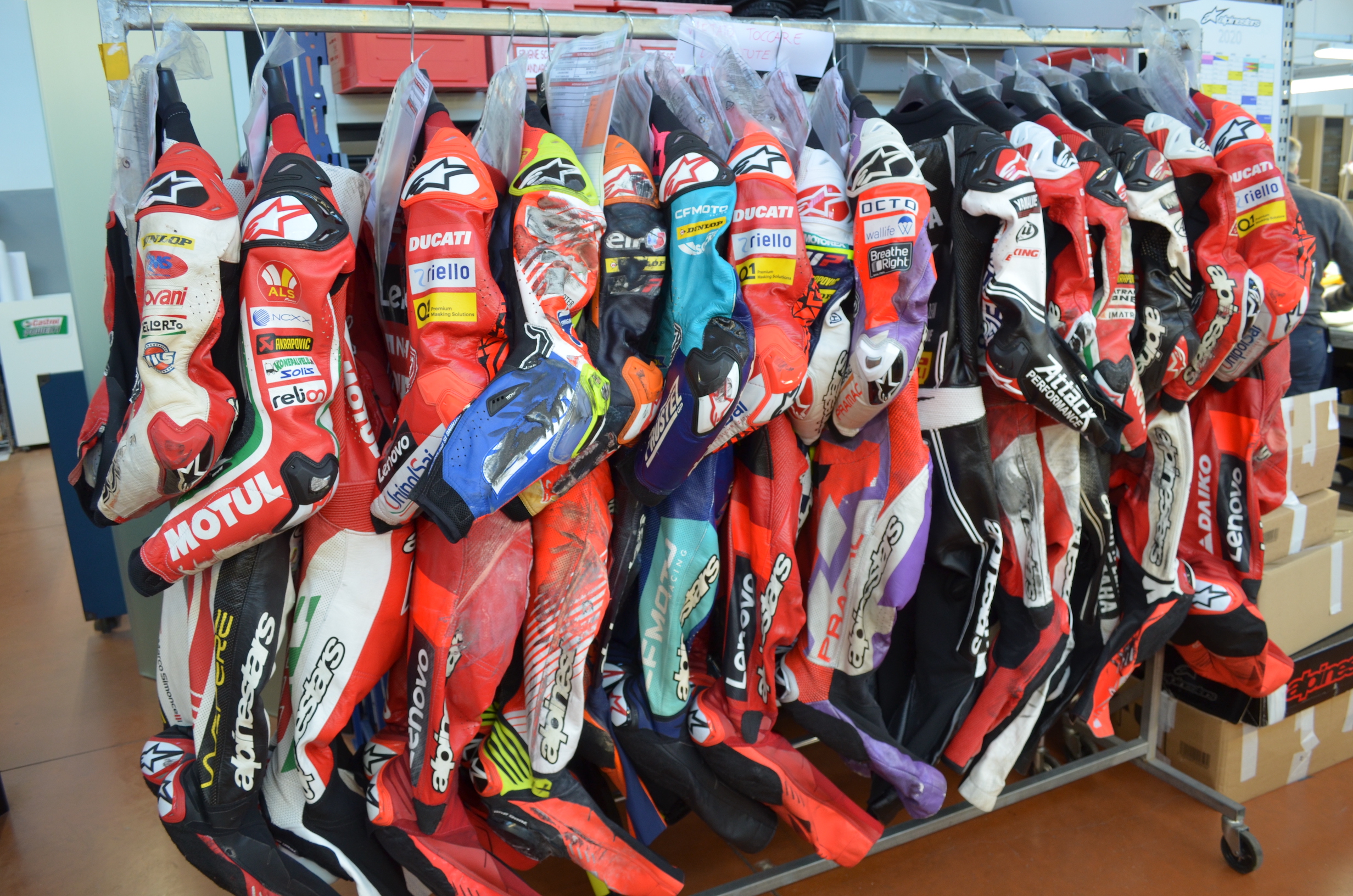
Als racer wil je op de motor uiteraard niet gehinderd worden door je pak, de eerste voorwaarde voor een goede racecombi is dan ook dat hij je als gegoten zit. Voor alle gesponsorde Alpinestars-racers betekent dat maatwerk.
“We nemen van alle racers voor het seizoen de maten, ook als ze al tien jaar met onze pakken rijden. Het kan uiteraard zijn dat we doorheen het seizoen alsnog aanpassingen moeten doorvoeren, als een racer wat verdikt of wat kilo’s afvalt. In de Rookies Cup hebben we sowieso meer werk in het seizoen om de pakken aan te passen want die jonge racers zijn doorgaans nog niet volgroeid”, meldt Gordon terwijl hij me de matentabel van Marc Márquez toont.
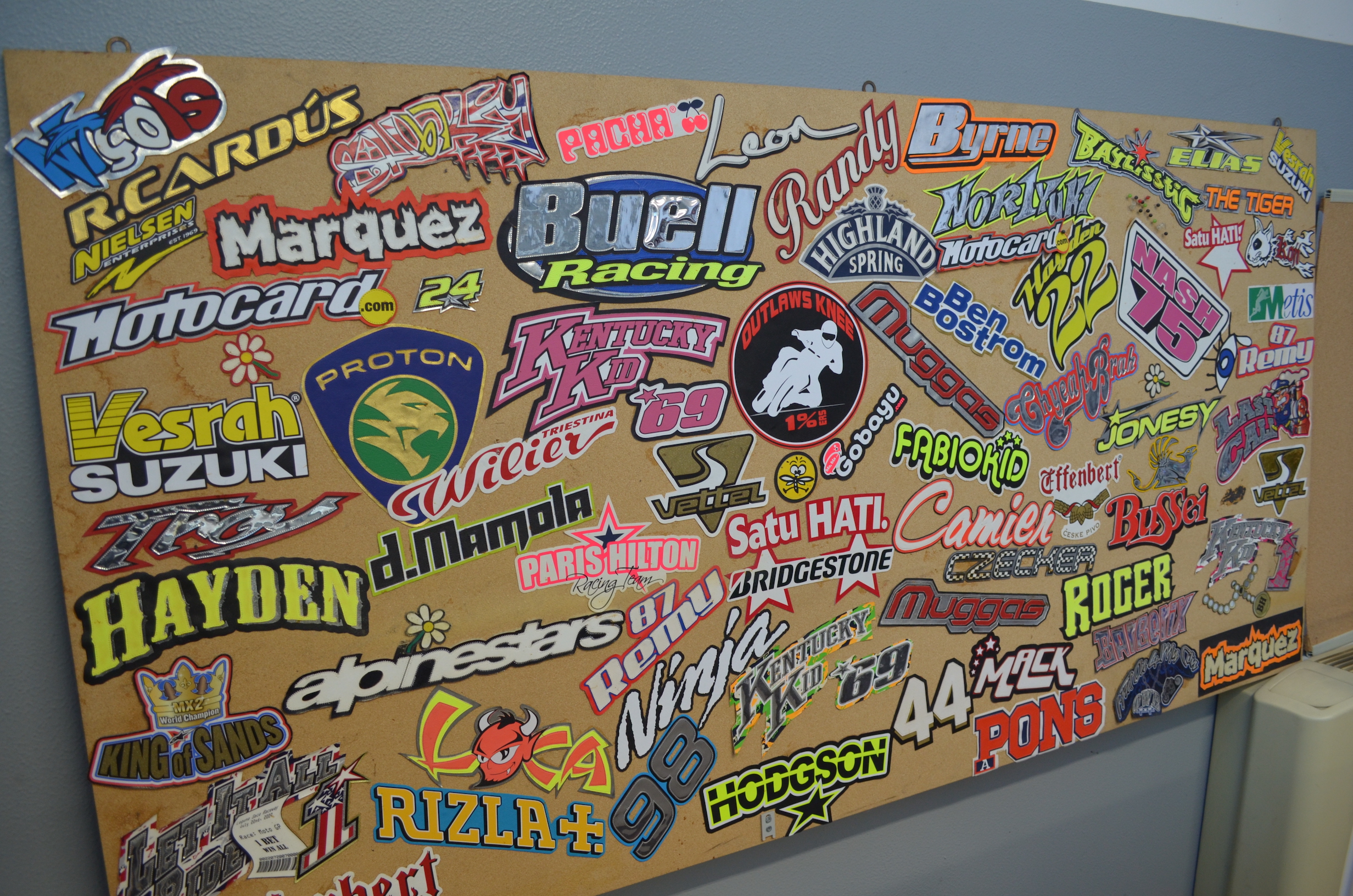
Op basis van de matentabel en de input van het raceteam wordt er dan een eerste artwork gemaakt. Dat ontwerp moet dan door de renstal worden goedgekeurd en dat heeft soms wat voeten in de aarde. “Bij de fabrieksteams valt dat meestal wel mee. Bij de satellietteams en de teams in de lagere raceklassen ligt het soms moeilijker omdat er vaak op het laatste nippertje nog sponsors worden toegevoegd. Maar goed, dan passen we ons daaraan aan.”
Werden de lederen pakken vroeger eerst bedrukt in een algemene kleur van het team waarna de logo’s van de sponsors erop werden gestikt, dan wordt nu het volledige artwork op het pak gedrukt. Maar wacht, zo ver zijn we nog niet want de rijders kunnen zelf nog een en ander kiezen.
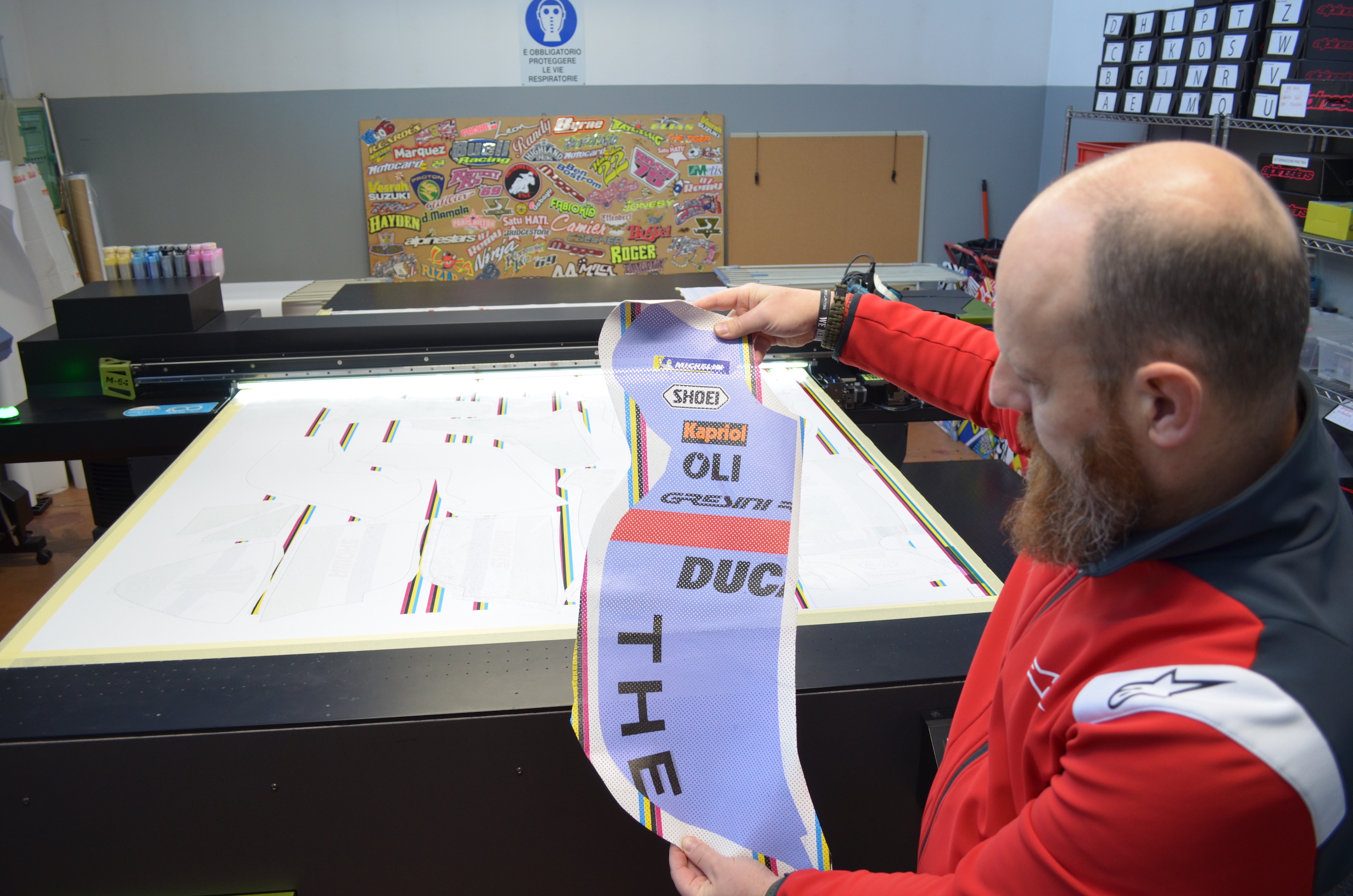
“In overleg met de racer, maar altijd binnen de grenzen van wat de raceorganisator voorschrijft, kunnen we een aantal parameters afstemmen op de voorkeuren van de rijder. Zo wil de ene een harde protector op de manchet van de handschoen en heeft een andere liever een zachtere. Sommigen willen pink en ringvinger van de handschoen aan mekaar verbonden, anderen niet. We kunnen daarin meedenken”, zegt Casteller.
Over het basismateriaal van een eendelig racepak wordt echter niet gediscussieerd: kangoeroeleder is de standaard. Gordon daarover: “Kangoeroeleder is dunner dan rundsleder waardoor je een veel lichter pak krijgt. Inclusief de airbag wegen onze pakken ongeveer 6,5 kilogram, dat is een gewicht dat je met rundsleder nooit haalt. Bijkomend voordeel van kangoeroeleder is dat het soepeler is, waardoor het pak vanaf de eerste training of wedstrijd als gegoten zit. Je hoeft het dus niet ‘in te rijden’. Keerzijde van de medaille is dat kangoeroeleder na een vijftal jaar zijn eigenschappen begint te verliezen, het is dus iets minder duurzaam als product.”
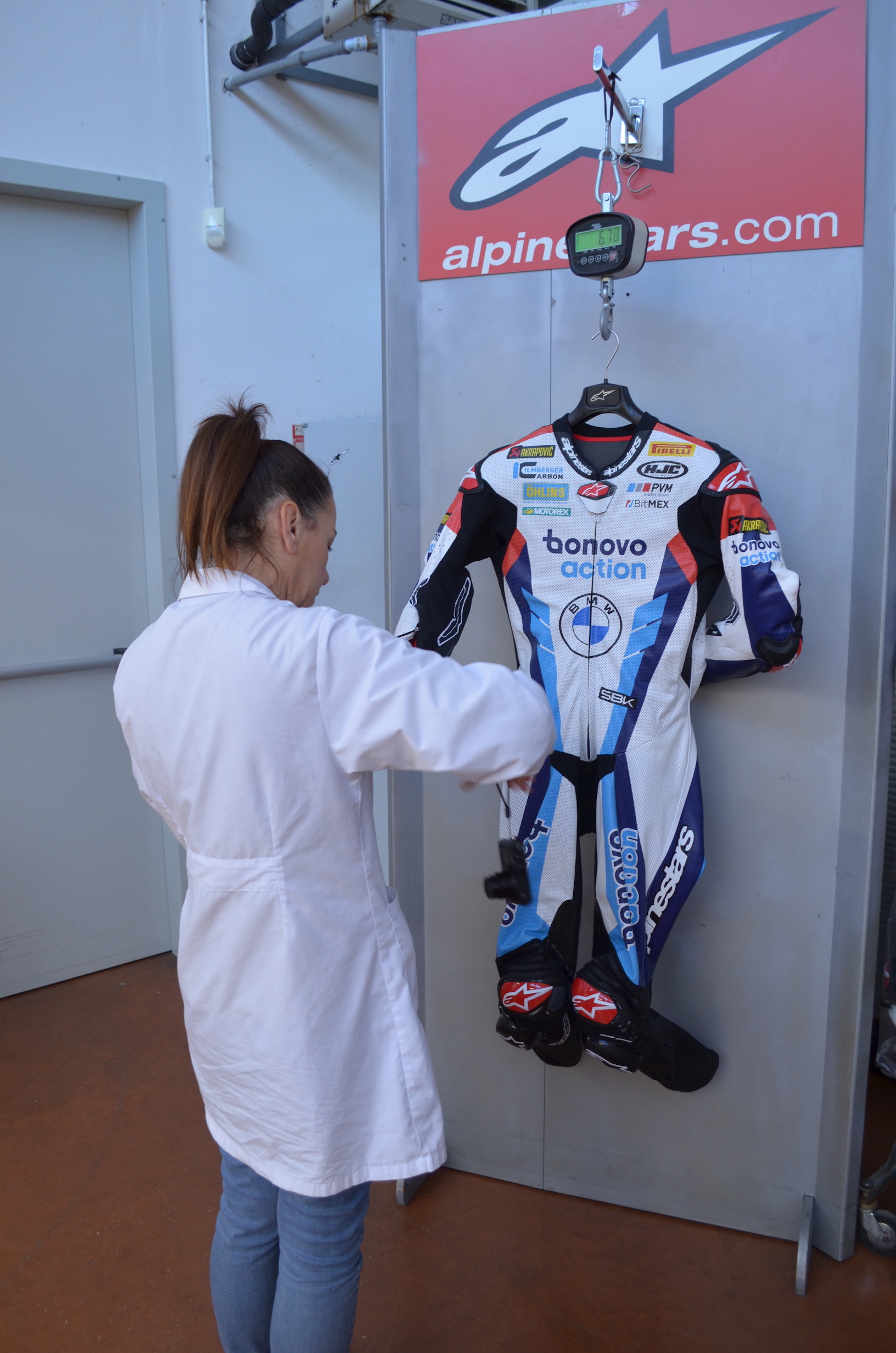
Niet dat het voor de gesponsorde racers zo veel uitmaakt, afhankelijk van het aantal crashes en het aantal sponsorwissels jaagt een gesponsorde rijder er per seizoen acht tot twintig pakken door. En als je rekent op ongeveer zesduizend euro per custom made racepak dan tikt dat al flink aan als kost voor Alpinestars, dat op elke race aanwezig is met een servicetruck.
“Dorna schrijft voor dat elke racer per weekend drie perfect functionerende pakken ter beschikking moet hebben. Wij doen daar vanuit Alpinestars altijd een vierde pak bij, een niet-geperforeerd exemplaar voor het geval het weer tegenzit. Daar bovenop hebben we voor alle racers ook reserveonderdelen voor hun pakken bij zoals complete mouwen of broekspijpen. Als iemand er tijdens de trainingen af gaat, dan kunnen onze stiksters in de servicetruck tijdens het weekend dat pak al herstellen.”
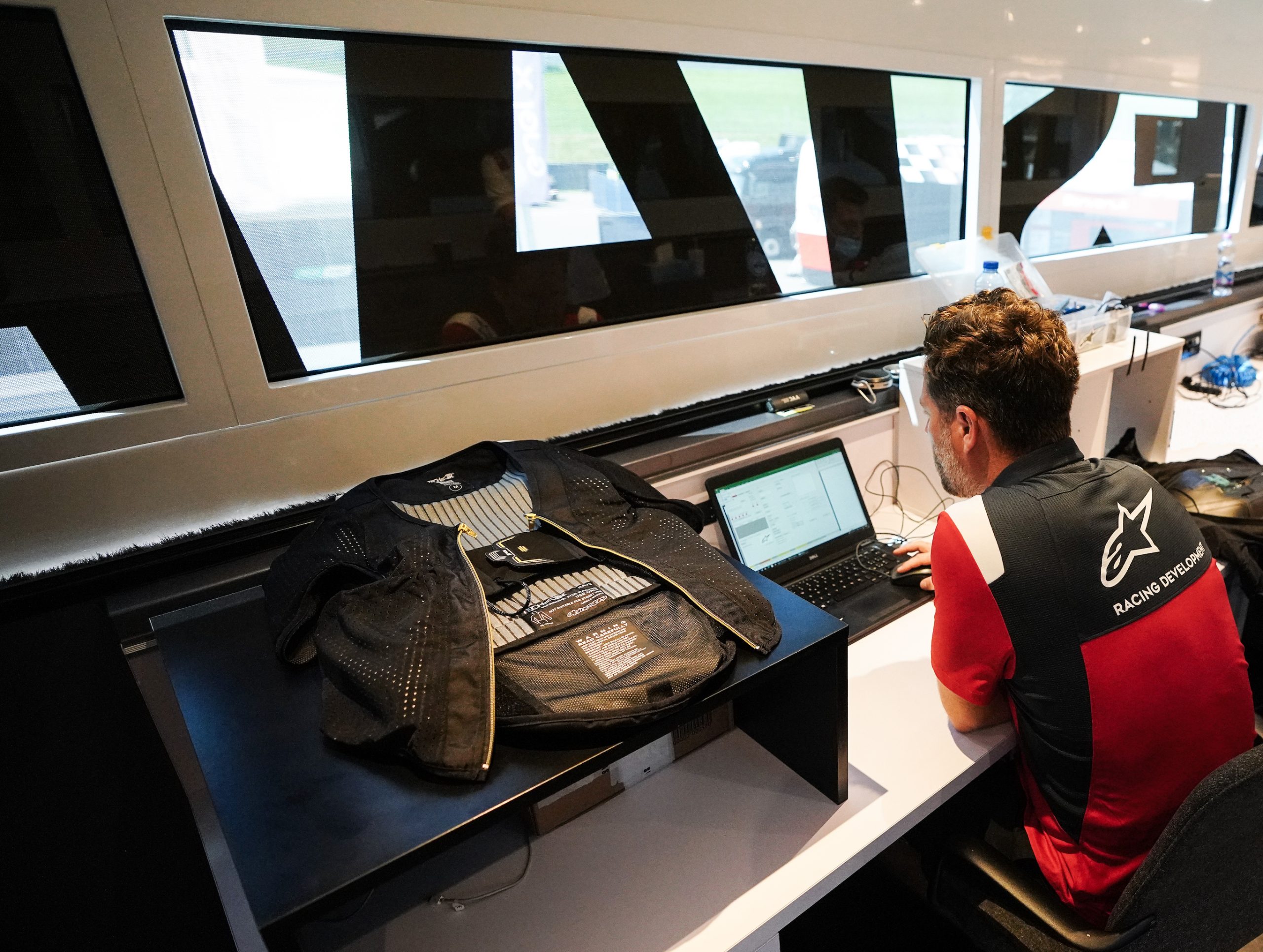
Voor het pak bedrukt wordt, worden eerst alle lederen onderdelen gesneden. “Een beetje ruimer dan wat we nodig hebben, kwestie van na het printen het leder nog op exact de juiste maat te kunnen bijsnijden”, toont Gordon terwijl een bloedserieuze Italiaan met een scalpeltje extreem precies leder aan het snijden is. Om de vijf sneden zet hij het scalpel weer op scherp door het mes een keer of twintig langs een wetsteen te halen. Daarna worden alle lapjes leder op de printer gelegd, waarna die in een halfuurtje het volledige pak print.
Na drie uur op een klassiek droogrek (niks hightech, gewoon een droogrek zoals iedereen dat thuis heeft staan om de was te drogen), worden alle delen exact op maat gesneden om aansluitend tot een pak gestikt te worden. Daarvoor staat een hele rij stikmachines opgelijnd, allemaal ‘bevrouwd’door zeer geconcentreerde dames.
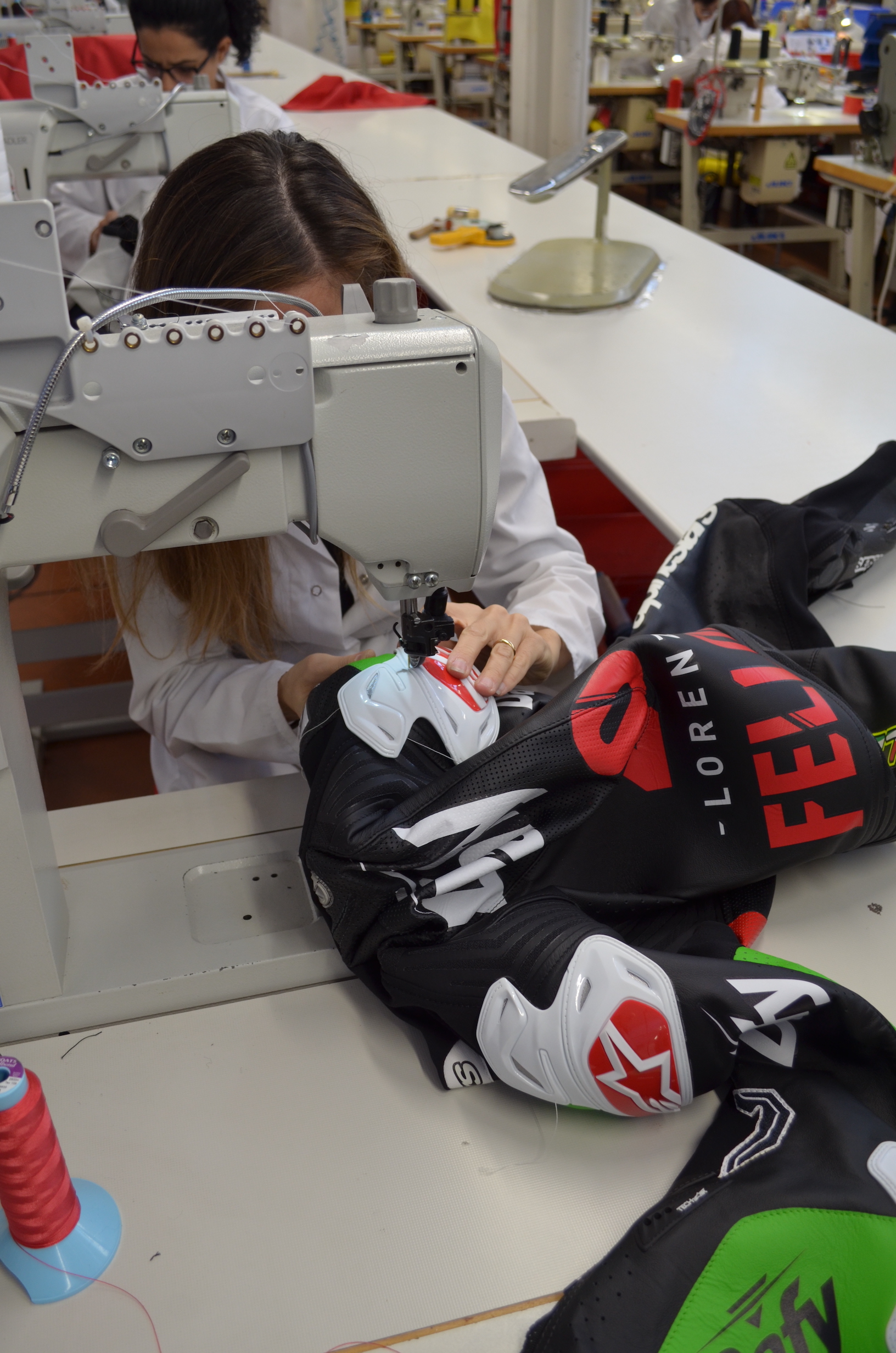
“Nee, je zal geen mannen aantreffen achter de stikmachines. Vrouwen zijn hier beter in, ze kunnen zich veel beter concentreren en hebben meer aanleg voor dit precisiewerk. Ze hebben ook allemaal hun specialiteit en dat respecteren we. Wie heel goed is in handschoenen stikken, die laten we vooral handschoenen doen.”
In het standaard productieproces kost het Alpinestars drie tot vijf dagen om een racepak te maken en werken er acht verschillende personen aan één pak. Moet het om God weet welke reden snel gaan, dan worden er twee dames ingezet om het pak van A tot Z klaar te stomen en klaren ze de klus in acht uur.

Aan het einde van de productielijn worden alle pakken gewogen en fotografeert Alpinestars alle details van het pak in functie van kwaliteitscontrole en archivering. Na het seizoen komen alle pakken terug naar Asolo, zowel de gecrashte als de nog bruikbare pakken en de nagelnieuwe suits.
“We stockeren die allemaal en in sommige gevallen lenen we eens een pak uit aan een winkel om te tonen in de verkoopruimte, da’s altijd mooie reclame. Maar de studie van de gebruikte pakken helpt ons ook bij de ontwikkeling van nieuwe technieken”, verduidelijkt Gordon als we weer in de auto stappen om ons naar het R&D-center te begeven.
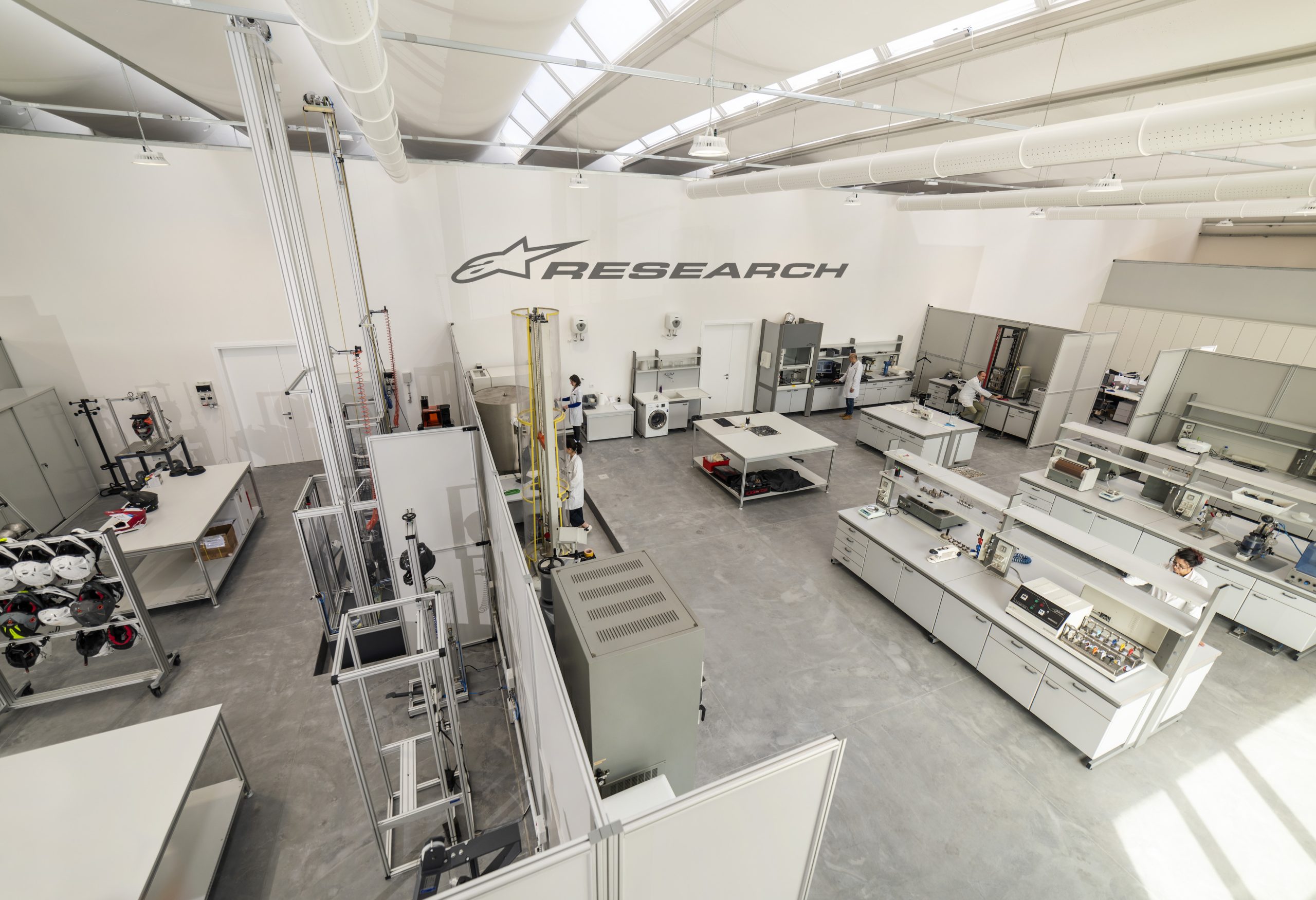
Alleen al aan het aantal locaties waarop Alpinestars in en rond Asolo actief is kan je zien welke spectaculaire groei het bedrijf de voorbije decennia doormaakte. En je proeft ook de Amerikaanse invloed; alle gebouwen zitten strak in de huisstijl, iedereen praat vloeiend Engels. “Dat laatste is essentieel als je wereldwijd actief bent. We kunnen ons geen communicatiestoornissen veroorloven.”
In het R&D-center worden alle stoffen en onderdelen voor de kleding, laarzen en helmen getest. Je vindt er dan ook de volledige opstellingen om motorhelmen te testen naast de branders waarmee de brandveilige raceoveralls voor Formule 1-racers worden getest en alle machines om de slijtvastheid van de zool van een motorlaars te controleren.
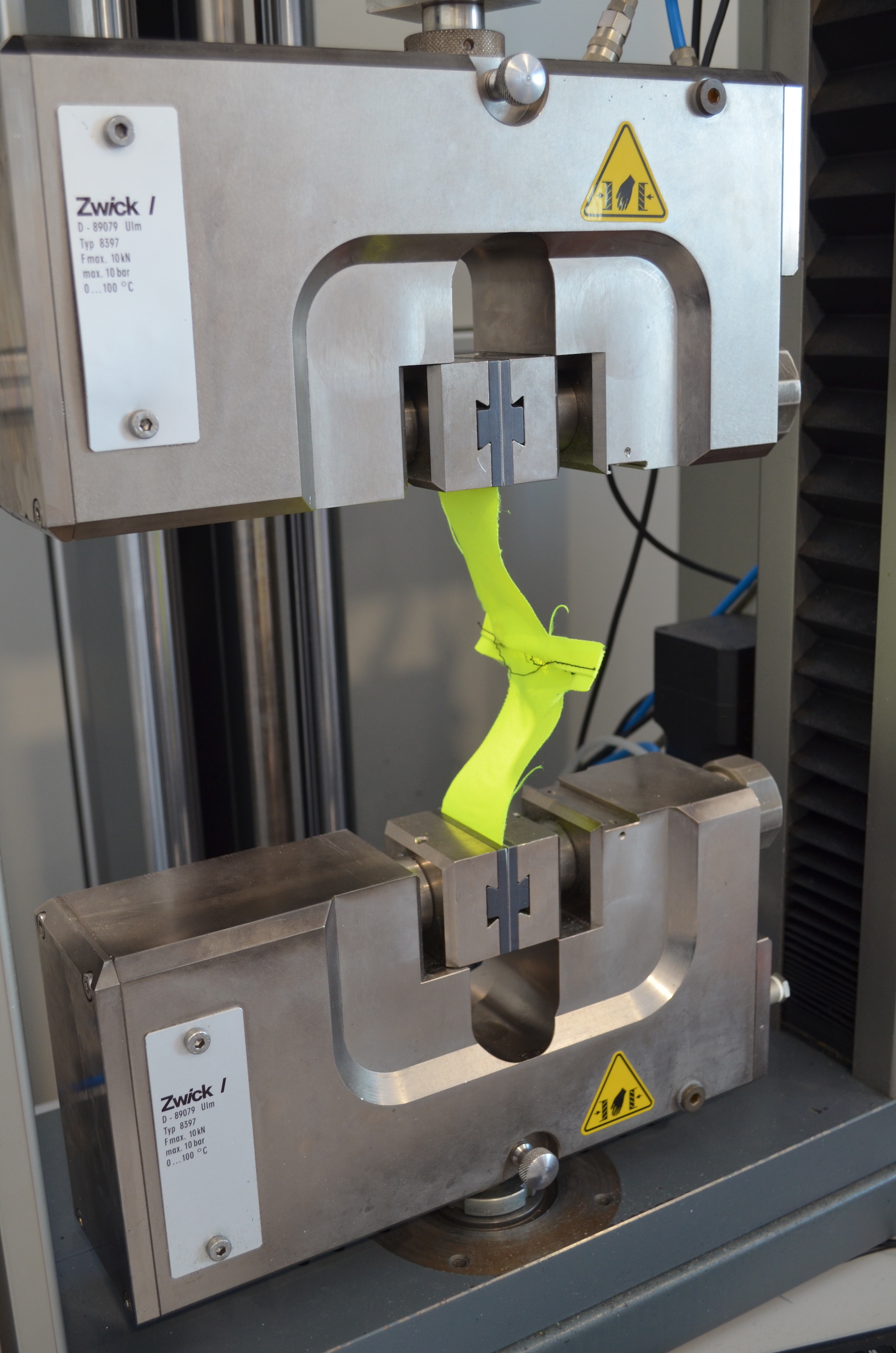
Voor de Moto GP-rijders heeft Alpinestars trouwens een ‘herzolingsdienst’: na elke race worden de laarzen van de toppers van nieuwe zolen voorzien. ‘Gewone’ Alpinestars consumenten die op versleten zolen rondsloffen kunnen van dezelfde dienst gebruikmaken om hun motorlaarzen te laten herzolen.
Afsluitend loodst Gordon me naar de afdeling waar de airbags voor de motorkleding worden ontwikkeld, een stokpaardje van Alpinestars. “We begonnen met het project in 2001, helemaal vanaf nul want er was nog geen referentiemateriaal. Het eerste systeem maakte gebruik van stikstof, momenteel werkt de airbag op een mix van 96 % argon en 4 % helium. In 2004 begonnen we met datalogging in de racerij, met pakken die vol sensoren zaten. Vijf jaar later konden we het eerste Tech Air-systeem voorstellen, met twee CO2-patronen in de hump en een airbag die enkel de schouders en sleutelbeenderen beschermde.”
“Veertien jaar en ontelbare versies en evoluties later is de elektronische unit die het geheel aanstuurt kleiner dan een luciferdoosje en beschermen we de volledige romp van de motorracer én de heupen. Helemaal in het begin waren er nog racers die sceptisch stonden tegenover deze nieuwe ontwikkeling, maar inmiddels is de airbag verplicht in de racerij en is iedereen overtuigd van de veiligheidsvoordelen, zonder dat er nog praktische nadelen aan vasthangen. En met alle afgeleide producten profiteren ook de straatrijders van deze technologie.”
Tekst Bart De Schampheleire • Fotografie Alpinestars, Bart De Schampheleire