In de reeks ‘Hoe maakt u het?’ trekken we telkens naar een bedrijf in de motorbranche om uit te zoeken hoe een product gemaakt wordt. Van banden tot uitlaten en van laarzen tot helmen leggen we de finesses van de productieprocessen bloot.
Ik bezocht eerder in Noord-Italië al fabrieken waar motorlaarzen worden gemaakt, al moest je daar meer de term ‘assembleren’ dan ‘produceren’ op plakken want de meeste onderdelen voor de laarzen werden elders voorbereid. “Niks van dat bij ons. Behalve de metalen gesp waarmee je onze TransTourman GTX laars sluit en de panelen voor de aramide binnenschoen van onze Security EVO laarzen, maken we elk onderdeel voor elke daytona laars hier in Eggenfelden”, stelt zaakvoerder Reinhard Frey me gerust.
Eggenfelden moet je in Beieren zoeken; een dik uur ten westen van München is het met vijftienduizend zielen niet veel meer dan een uit de kluiten gewassen dorp. Maar wel een dorp met een opmerkelijke schoenengeschiedenis. “In de periode na de Tweede Wereldoorlog vond je in Eggenfelden niet minder dan acht schoenfabrieken en toch besloot mijn moeder om er een negende te openen, al was dat niet meteen een echte schoenfabriek. Haar idee was om heel kleinschalig te werken en uiterst gepersonaliseerd schoeisel te maken. Dat begon met simpele pantoffels, evolueerde naar alle soorten schoenen en al snel kregen we klanten met probleemvoeten over de vloer. Mensen voor wie geen enkele standaardschoen comfortabel was, die kwamen naar ons voor aangepast schoeisel”, keert Reinhard Frey een eind terug in de tijd, naar 1957 om precies te zijn.
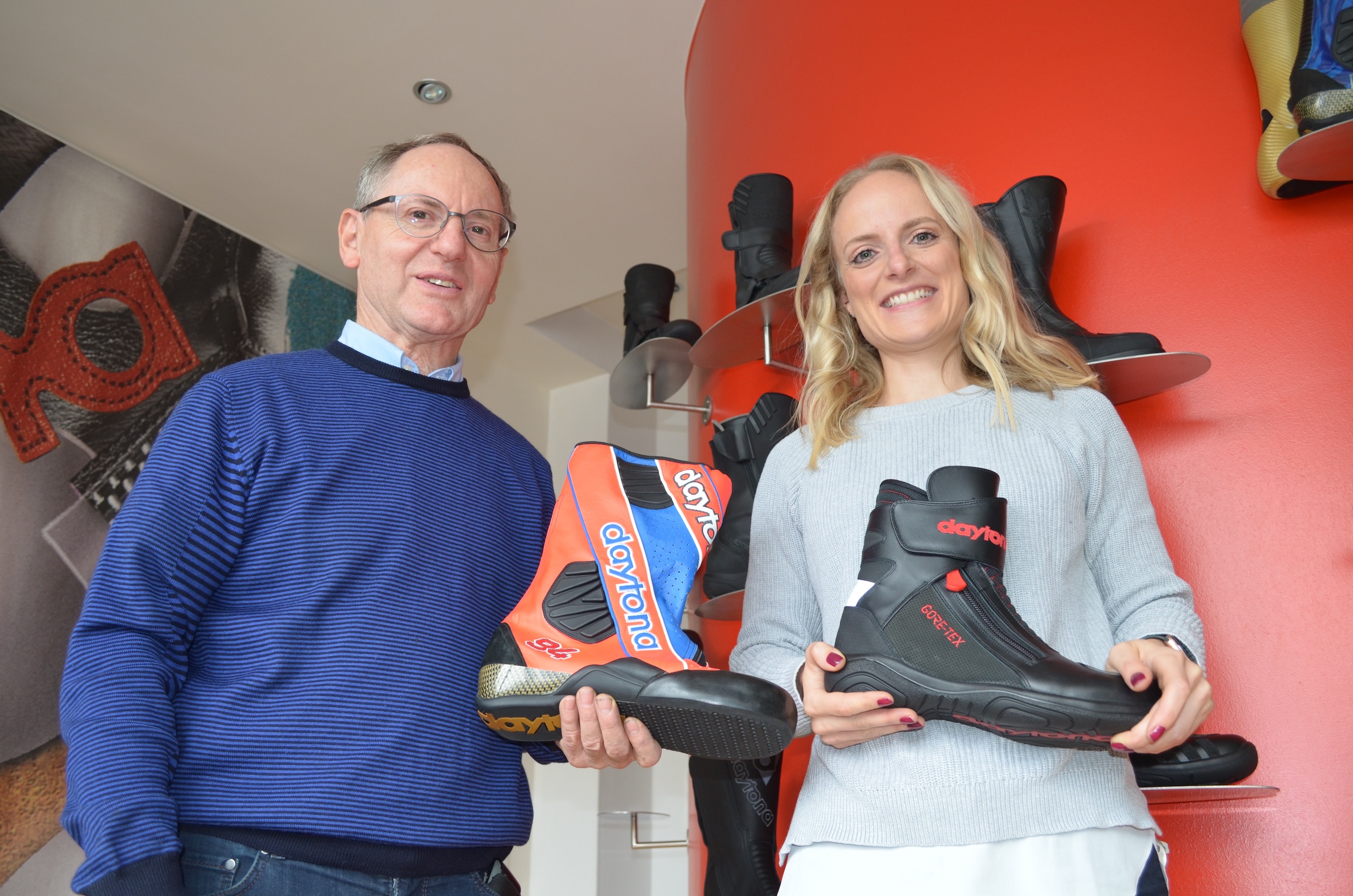
In de jaren zestig stapte zijn broer Helmut in de zaak en hoewel de familie helemaal geen link met de motorwereld had, gaf zijn vader ergens midden de jaren zestig Helmut een 50cc Honda viertakt cadeau. “Het ding was niet vooruit te branden, maar mijn broer wou de machine er wat sneller laten uitzien en kocht in Zwitserland een hoop tuningonderdelen die voor geen meter pasten. Waarop hij ermee naar een zijspancoureur in de buurt trok. Die werkte de Honda af en zo legden we contact met zijn raceteam en het bedrijfje waarmee hij lederen racelaarzen uit Italië importeerde. De laarzen stonden echter op lederen zolen, totaal onbruikbaar in het Duitse weer en dus vroeg die motorracer of wij geen rubberzolen onder zijn Italiaanse laarzen konden zetten. Dat konden we wel, maar al snel kwamen we erachter dat we eigenlijk beter compleet nieuwe laarzen voor motorrijders konden ontwikkelen. En zie waar we nu staan: we werken in Eggenfelden met 115 medewerkers, ontwikkelen en produceren alles in eigen beheer en zetten jaarlijks ongeveer vijftigduizend motorlaarzen op de markt”, meldt Richard met gepaste trots.
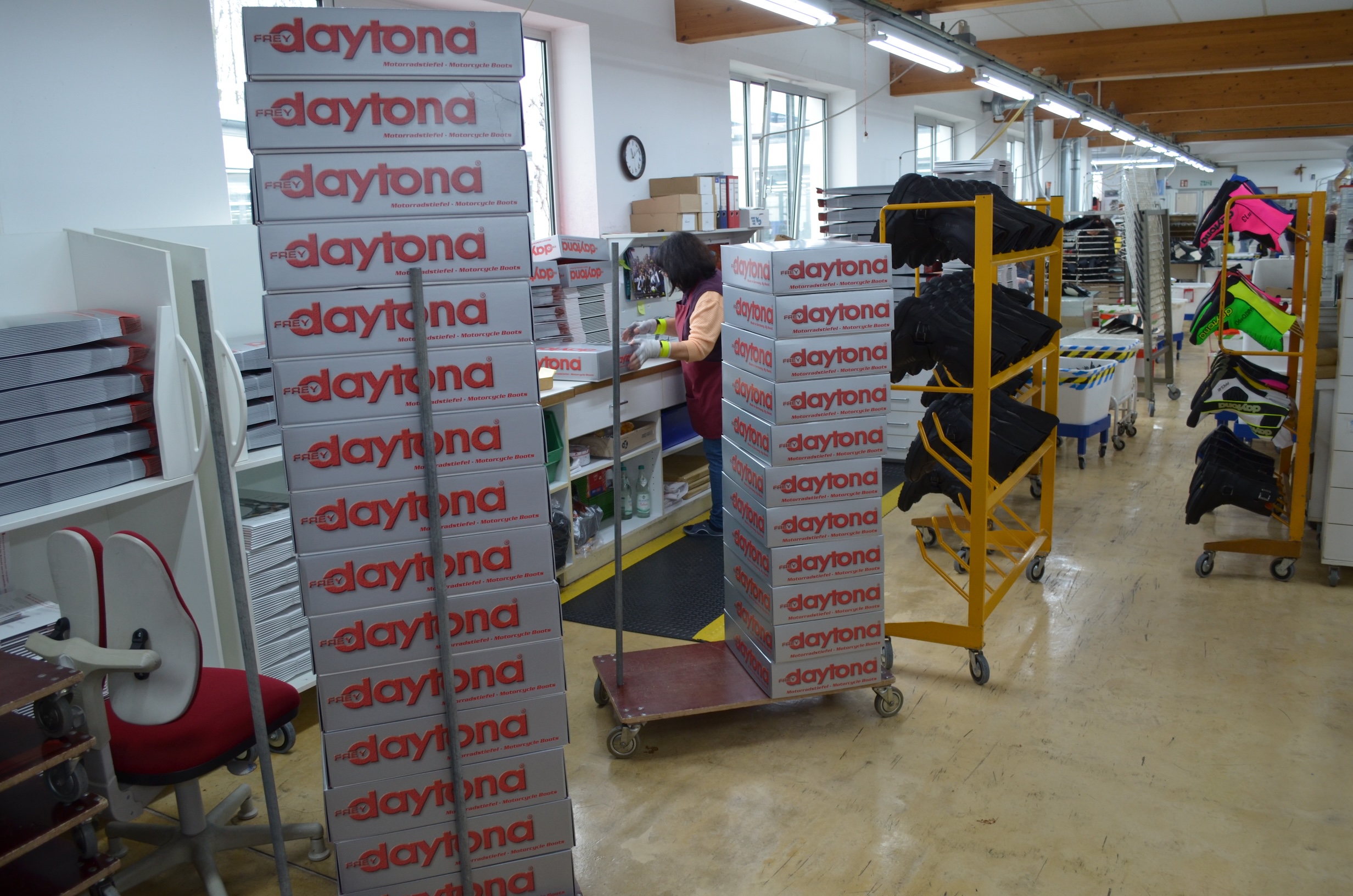
Voor we aan de rondleiding beginnen, is Richard niet te beroerd om ook de moeilijkheden waarmee zijn bedrijf kampt te bespreken. Toen hij in 1973 in het bedrijf stapte en met de merknaam daytona – met kleine d – op de proppen kwam, maakte hij naar eigen zeggen meteen ook een grote blunder. “Mocht ik alles opnieuw kunnen doen, ik zou niet meer voor die merknaam kiezen. Het klonk wel heel internationaal en racy, maar we hebben er aan het eind van de jaren negentig een hoop gedoe mee gehad in Amerika. Ik had voor alle markten waarop we actief waren de merknaam daytona gedeponeerd, tot de International Speedway Corporation daar ineens een wereldwijde bescherming van de merknaam tegenover zette. In die periode verkochten onze laarzen best goed in de VS en het duurde vier jaar vooraleer we met de ISC tot een regeling konden komen. Onder andere door die zaak zijn onze verkopen in de Verenigde Staten enorm teruggelopen”, vertelt Frey die sinds kort het bedrijf alleen runt, na het overlijden van zijn broer Helmut.
Het wegvallen van Helmut was voor daytona niet alleen een emotioneel verlies. “Mijn broer was de man van de ideeën, degene die al het ontwikkelingswerk aanstuurde. Hij had de creativiteit om met nieuwe producten en ontwikkelingen in te spelen op de vragen en wensen van de motorrijders. Toen mijn broer ziek werd, is het ontwikkelingsproces een beetje stilgevallen en corona heeft daar ook geen goed aan gedaan. Voor corona waren we jaarlijks aanwezig op alle grote motorbeurzen en daar moest je ieder jaar wel een nieuwigheid presenteren om de aandacht van het publiek te trekken. In de coronatijd waren er geen evenementen meer en viel ook de druk om iets nieuws te presenteren weg. Maar goed, dat ligt achter ons en we hebben een nieuwe designer aangetrokken om dat gat dicht te fietsen. Er zijn ideeën genoeg, ook om andere nichemarkten die heel specifiek schoeisel nodig hebben te bedienen. We hebben de kennis en het vakmanschap, die moeten we benutten”, klinkt Frey strijdlustig.
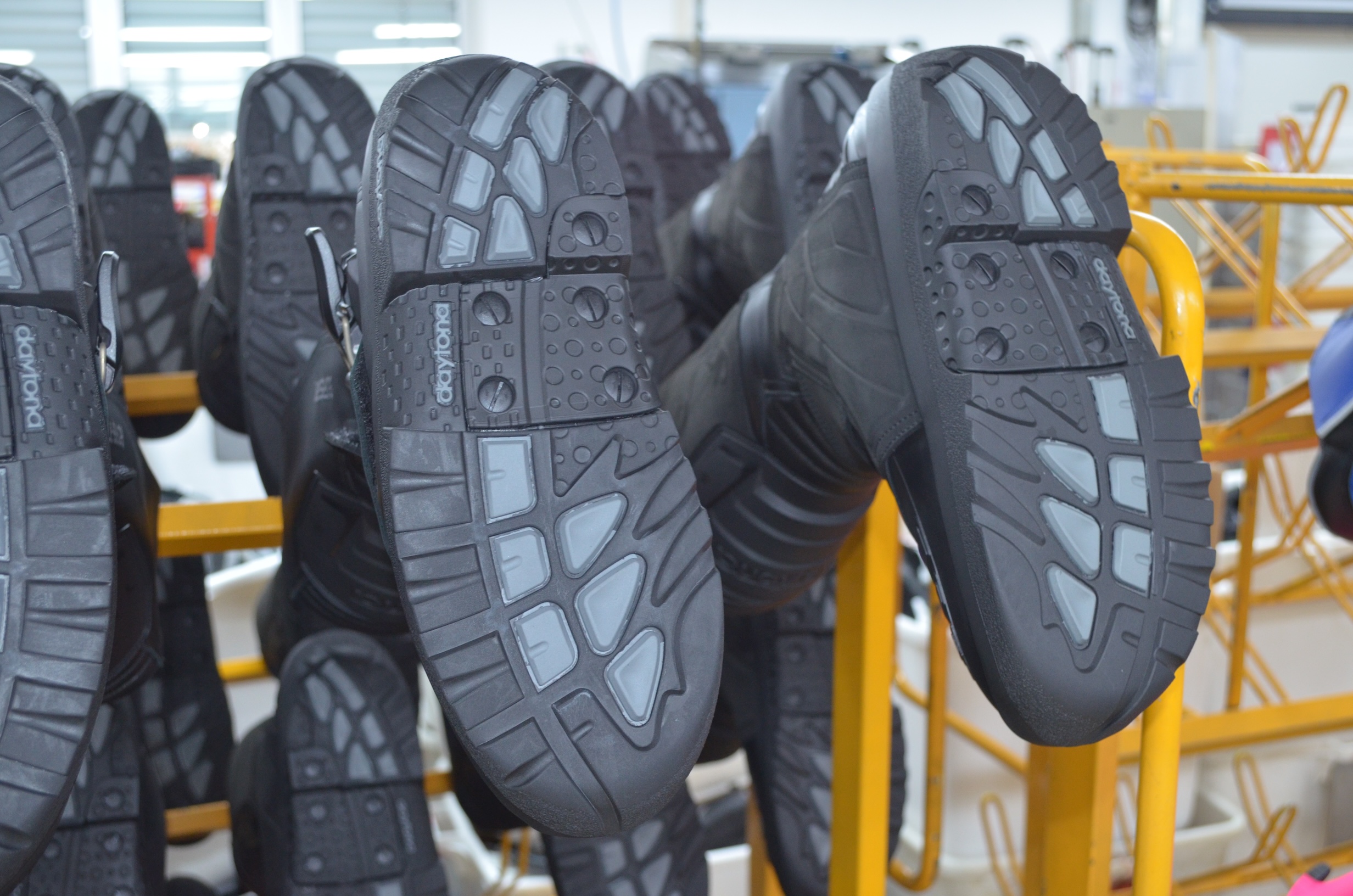
Hoog tijd om de productieruimte in te duiken die over twee verdiepingen verdeeld is. Op de benedenverdieping bevindt zich niet alleen de voorraad grondstoffen en afgewerkte laarzen; alle kunststof delen die nodig zijn in een motorlaars worden er ook geproduceerd met de machines zoals ze die ook bijvoorbeeld bij Givi/Kappa gebruiken om plastic delen te maken. “Alles samen bestaat een motorlaars uit ongeveer 120 onderdelen, voor een simpele tussenzool alleen al hebben we vier verschillende onderdelen nodig. De stalen lamel die onder de voet zit is essentieel voor de stabiliteit van de voet op de voetsteun”, toont Reinhard. Voor de enkelbescherming gebruikt daytona twee stukken zacht polymeer die met nopjes in mekaar passen en op die manier een schokdempende laag vormen, eenzelfde principe passen ze toe voor de bescherming op het scheenbeen. Voor de laarzen uit de EVO-lijn combineert daytona een lederen buitenschoen met een binnenschoen die opgebouwd is rond een harde structuur van aramide. Die aramide delen kopen ze in Duitsland in, maar ook de assemblage van die aramide binnenlaars gebeurt in Eggenfelden.
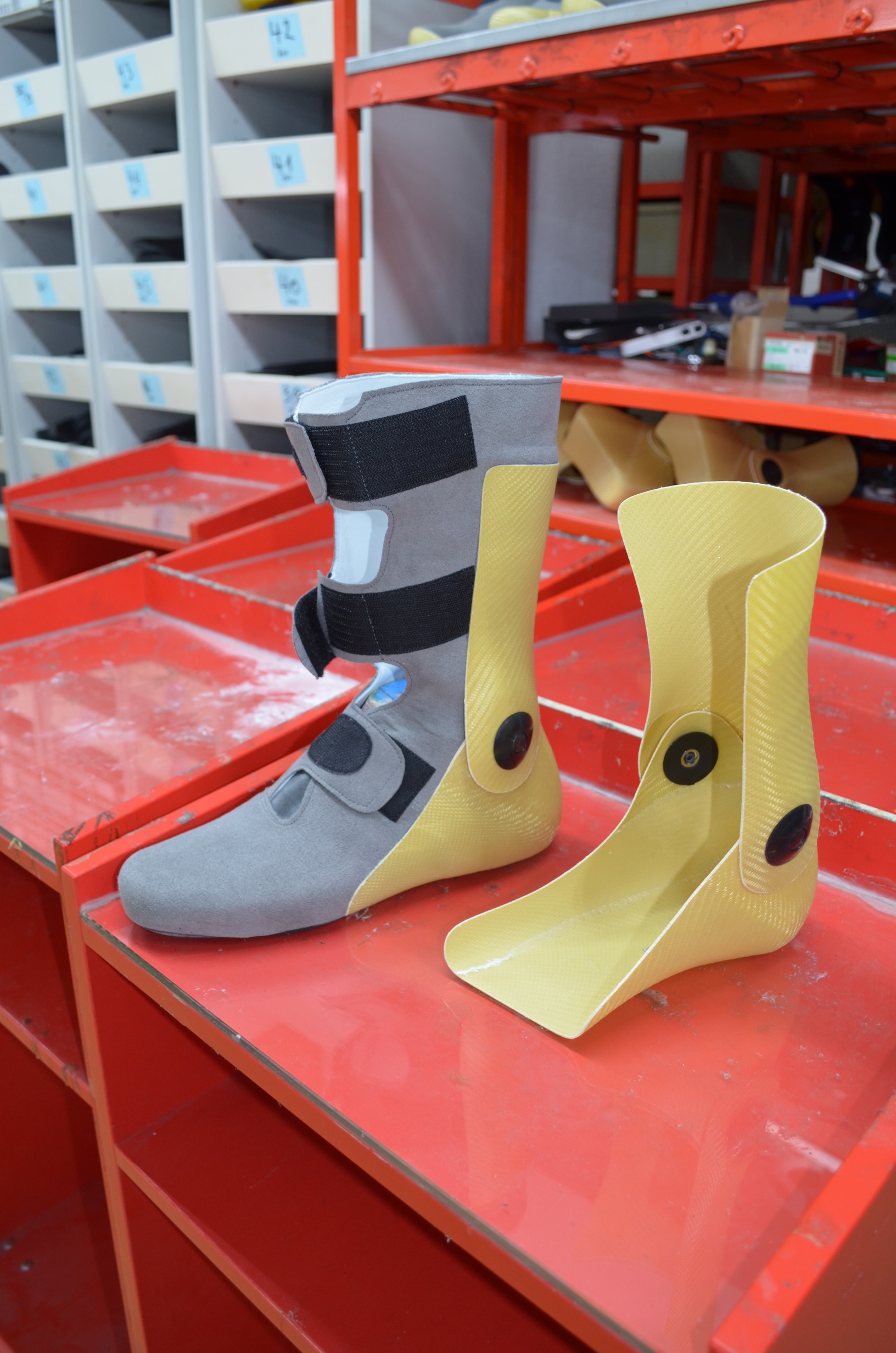
Op de eerste verdieping is een ruimte vol zwarte en felgekleurde lappen leder zowat de schatkamer van daytona. “Het leder komt uit Duitsland, Kroatië en Italië, het kangoeroeleder uiteraard uit Australië. Al die ledersoorten moeten aan bepaalde kwaliteitsnormen voldoen, al blijft het een natuurproduct en kunnen er altijd onregelmatigheden in zitten. Voor alle laarzen hebben we specifieke stansvormen die we gewoon en ondersteboven kunnen gebruiken voor de linker- en de rechterlaars. Het is aan de medewerkster om te kijken hoeveel stukken ze kan stansen uit de lap leder van 2,5 vierkante meter die ze ter beschikking heeft, dat is gewoon passen en meten. Voor de sportieve laarzen gebruiken we leder van 1,7 tot 1,9 mm dikte, voor de toerlaarzen is dat 2 millimeter en voor de endurolaarzen 2,5 mm. Kangoeroeleder is sowieso slechts 1,2 millimeter dik en dus veel lichter. En uiteraard zijn de vellen kangoeroeleder een stuk kleiner, die beestjes zijn niet half zo groot als een koe”, lacht Frey.
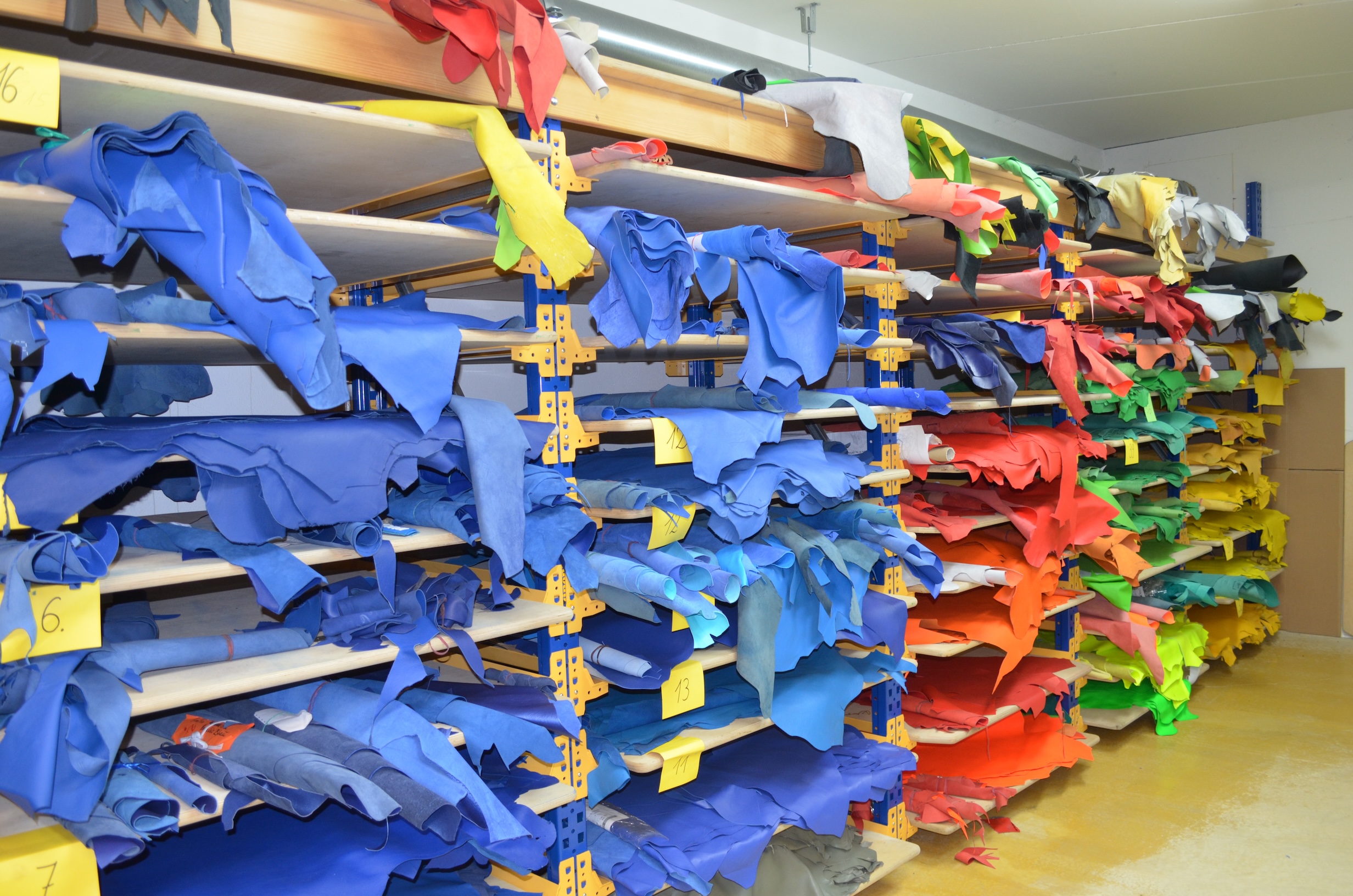
Om straks bij het assembleren van de laars te voorkomen dat er zich rond de stiknaden te veel materiaal ophoopt, worden de randen van de gesneden stukken leder wat verdund met een soort dremeltje. Waar nodig worden logo’s op de stukken leder gestikt, of andere stiksels aangebracht die functioneel of esthetisch kunnen zijn. Daytona heeft de Gore-Tex licentie en mag dat waterdichte en ademende membraan dus in zijn laarzen verwerken. Afhankelijk of het een lichte zomerlaars dan wel een stevige toerlaars voor het hele jaar wordt, gebruikt daytona een Gore-Tex laag van verschillende dikte. Nadat de verschillende stukken van de Gore-Tex voering aan mekaar zijn gestikt, worden de naden met een speciale tape afgedicht.
Om de tape goed te laten hechten, wordt die aangebracht met 400° hete lucht. Terwijl de dame (in de stikafdeling werken uitsluitend dames) de volgende voering stikt, controleert ze de waterdichtheid van de vorige voering die ze heeft afgewerkt met een speciaal toestel dat op 0,8 bar water doorheen het membraan probeert te persen. Een vloeipapier aan de andere kant van het membraan moet lekken duidelijk zichtbaar maken. “De Gore-Tex membranen worden enkel onder in de schoen met lijm vastgezet en helemaal bovenaan. Daartussen mag er geen vaste verbinding zijn tussen het membraan en het leder van de laars om de ademende eigenschappen van het Gore-Tex niet aan te tasten”, aldus Frey.
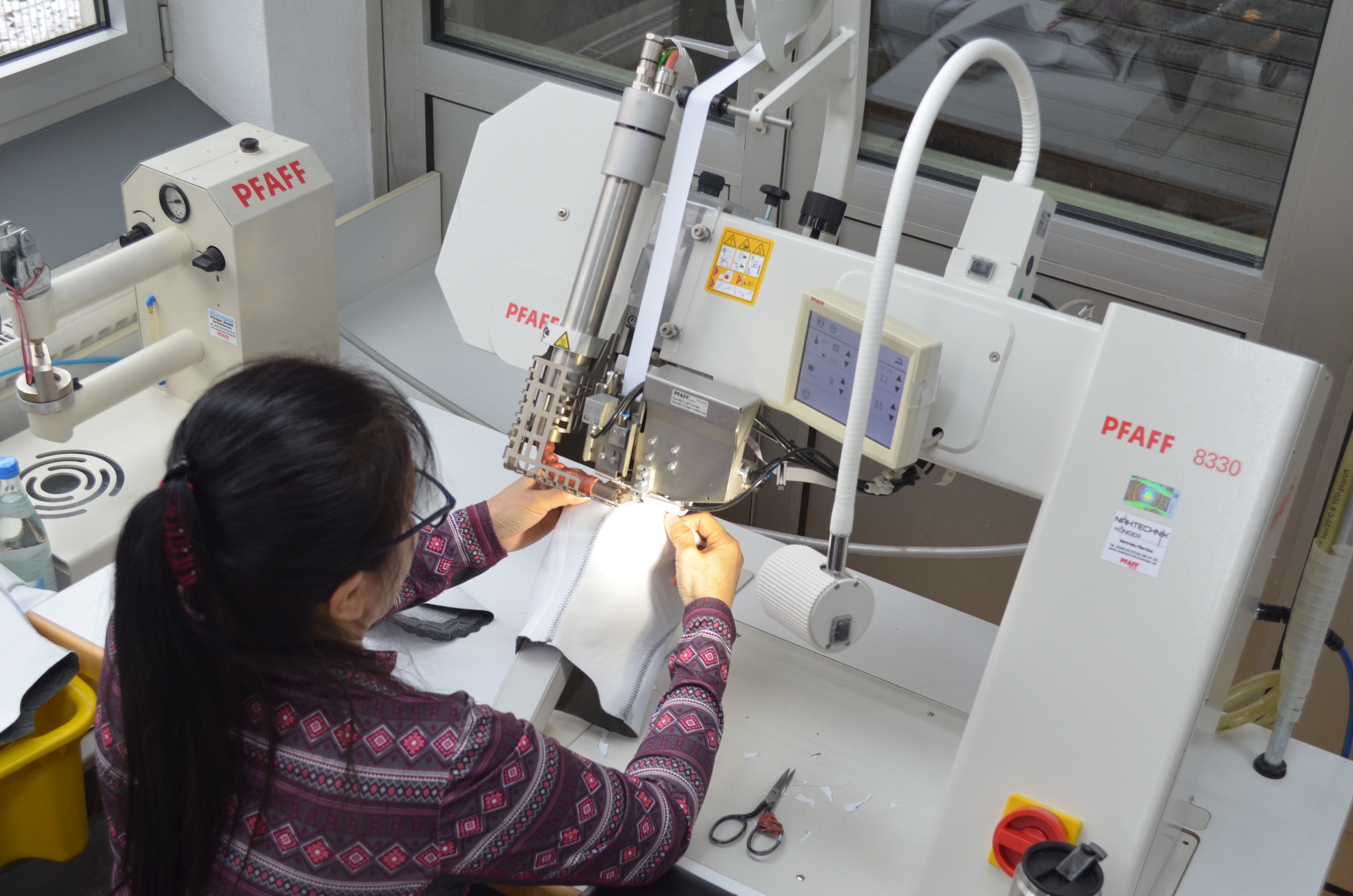
Met alle leder delen voorgesneden en van stiksels voorzien en ook alle kunststof onderdelen klaar, ligt er een hoop stikwerk voor de boeg om de bovenkant van de laars af te werken. Per model en per maat worden daarvoor alle delen in kistjes samengebracht en door verschillende stiksters verwerkt, het is niet zo dat één dame een complete bovenkant van een laars in mekaar stikt. Nadat de protectoren op scheenbeen en enkel op hun plaats zijn gelijmd en van een zachte laag zijn voorzien (je wil niet dat die protectoren je huid irriteren) worden de tussenzolen met twee kleine spijkertjes op leesten genageld. Een speciale machine (“Ze is intussen stokoud en echt aan vervanging toe, maar je vindt dit soort machines nog maar heel moeilijk.”) rekt het leder van de laars met waterdamp op zodat die gemakkelijker over de leest past, om ook de hak te omsluiten moet er nog spierkracht aan te pas komen.
De 250° warme lijm wordt heel snel en met veel druk aangebracht om te voorkomen dat de bovenschoen meteen weer loskomt van de tussenzool. Bovenop de tussenzool wordt nu een laagje plastic geïnjecteerd, een tweecomponenten materiaal dat een beetje aanvoelt als plasticine en dat de verbinding tussen laars en tussenzool perfect afwerkt. Het einde van het productieproces komt nu stilaan in zicht en dat mag ook wel want gemiddeld kost het 1 uur en 45 minuten om één motorlaars te produceren. Wat meteen toch al een verklaring is voor de stevige prijs van de daytona laarzen.
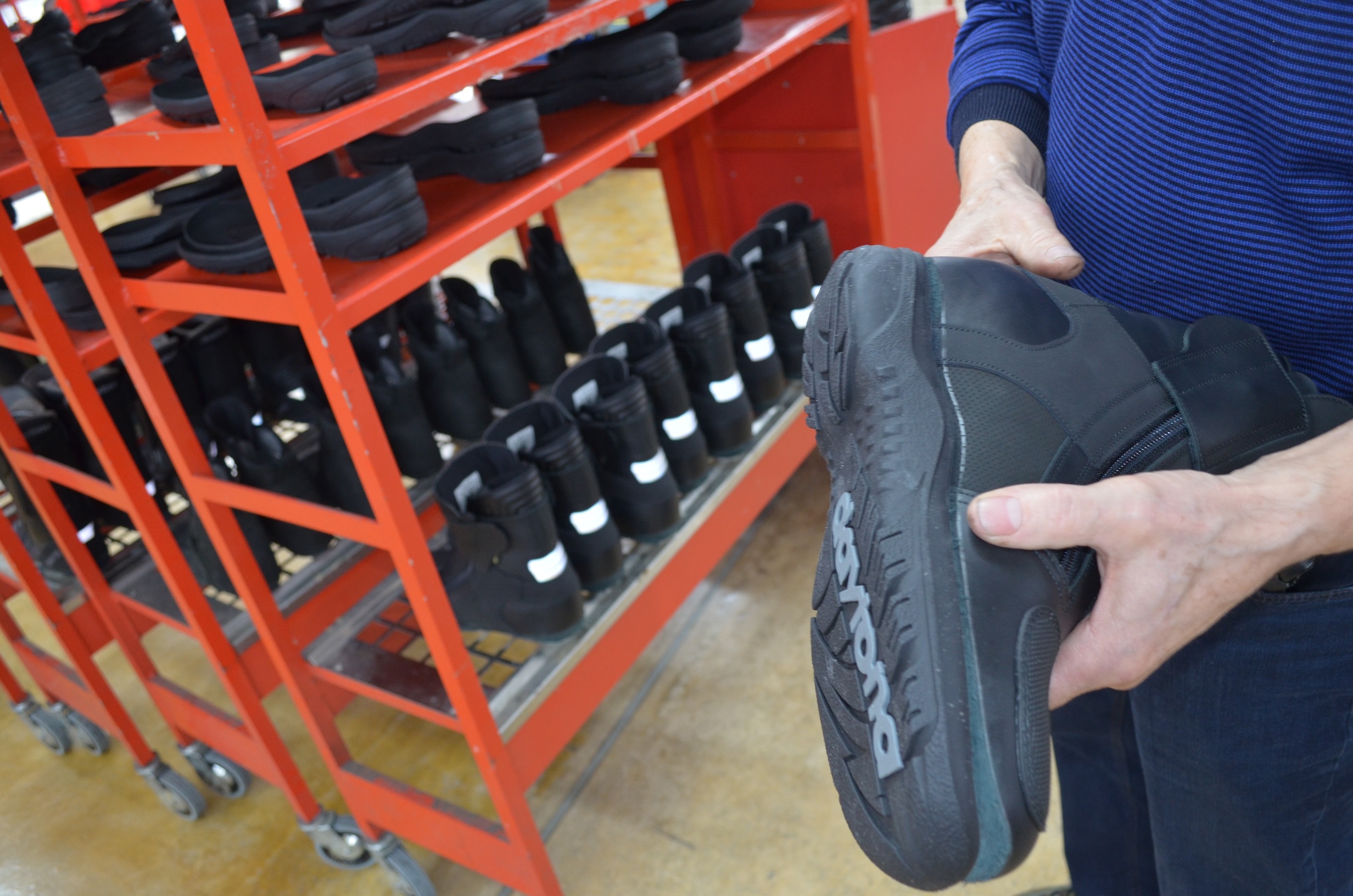
De zool en de onderkant van de tussenzool worden elk twee keer met lijm ingestreken waarbij er drie kwartier wachttijd zit tussen het aanbrengen van de eerste en de tweede lijmlaag. Tegen dat de zool en de laars klaar zijn om verenigd te worden, zijn de lijmlagen op elk van de twee delen al volledig uitgehard. Om de lijm opnieuw te activeren worden de beide onderdelen die op vereniging wachten gedurende 22 seconden tot 500° (!) opgewarmd waarna een speciale pers de laars op de zool drukt.
Een werknemer maakt van het afkoelingsproces gebruik om de lijmresten die nog niet helemaal zijn opgedroogd weg te polijsten van de zijkanten van de laars. “Maar dan moeten de leesten nog uit de laarzen gehaald worden. In sommige gevallen lukt dat niet meer omdat de ruimte in de laars daarvoor te beperkt is. Daarvoor hebben we gelukkig leesten die in het midden van de voet scharnieren, zo krijgen we ze toch nog uit de laarzen”, demonstreert Reinhard Frey. Het impregneren van het leder en retoucheren van mogelijke imperfecties zijn de laatste van de in totaal tachtig productiestappen die een daytona motorlaars doorloopt.
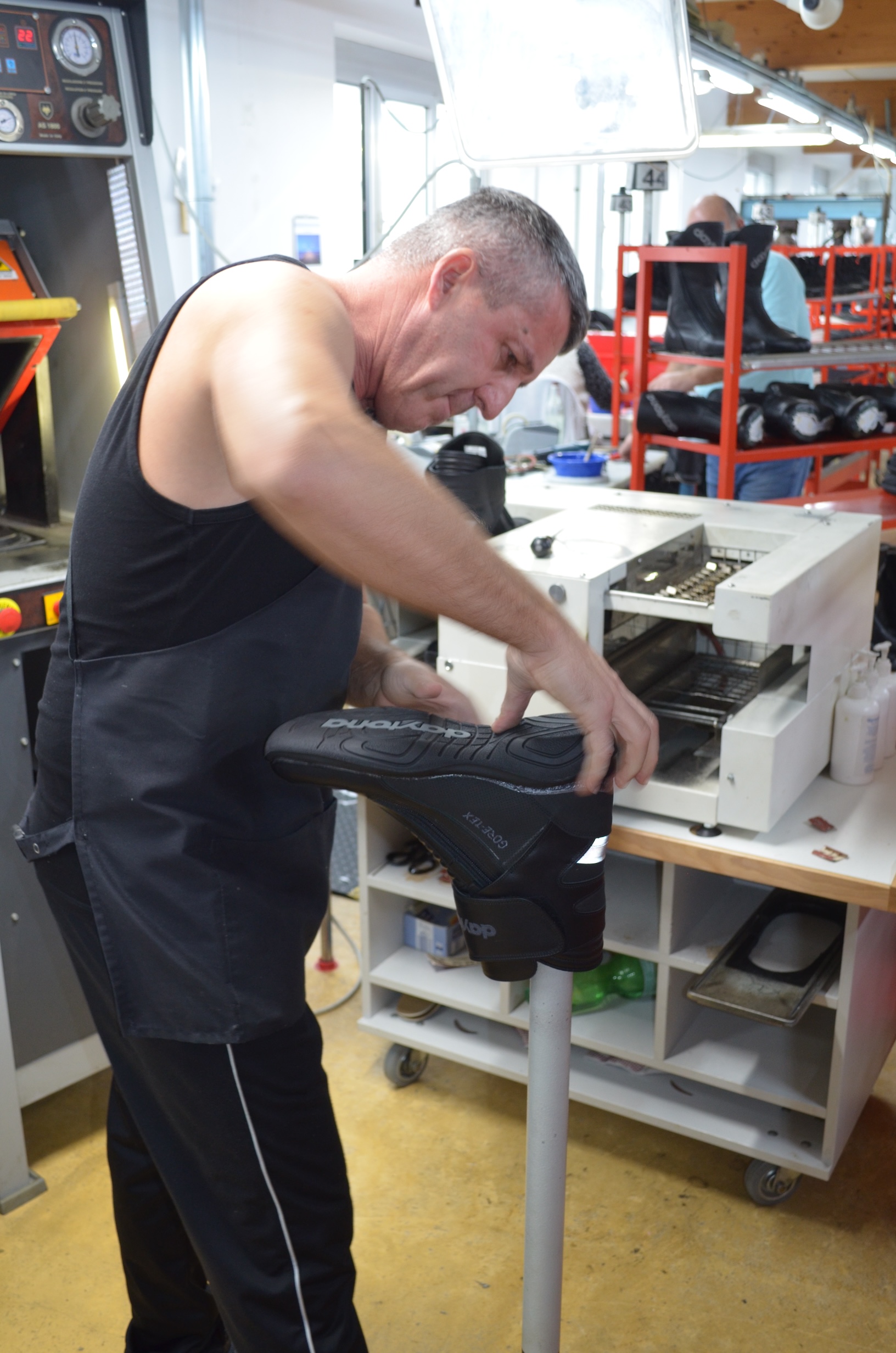
De uitzonderlijke aandacht voor detail resulteert in een enorm hoogwaardig product met een prijskaartje dat kan oplopen tot 1.200 euro voor een paar gepersonaliseerde Security Evo G3 Grand Prix laarzen. Maar voor dat geld krijg je dan wel wat. “We kunnen niet ontkennen dat we door economisch lastige tijden gaan en door de inflatie is de verkoop wat teruggelopen. Daar tegenover staat wel dat wij enorm kwalitatieve motorlaarzen aanbieden, laarzen waar motorrijders soms hun hele leven lang van genieten. We zien de jongste tijd dat we meer herstellingen binnenkrijgen, mensen hebben nu misschien even niet de centen voor een paar nieuwe daytona laarzen, maar zijn wel zodanig gehecht aan hun daytona’s dat ze die van een nieuwe zool laten voorzien of een andere herstelling laten uitvoeren. Dat geeft toch aan dat onze productkwaliteit en knowhow gewaardeerd worden”, besluit Reinhard Frey.
Meer info: www.daytona.de