Proberen binnen te geraken in de productieruimte van een grote bandenfabrikant is ongeveer hetzelfde als Peter Goosens vragen of je zijn recept van coq au vin even mag hebben voor het kerstdiner. Of anders gezegd: ‘njet’ gegarandeerd. Bij Heidenau werden we echter met open armen ontvangen en mochten we overal in de potten kijken.
Als er dan een bandenfabrikant positief reageert op je verzoek om de productie te bezoeken, dan moet je daarna niet onnozel doen over het feit dat je daarvoor wel een afstandje moet rijden. 872 kilometer om precies te zijn, want Heidenau vind je vijftien kilometer ten zuidoosten van Dresden; het drielandenpunt met Polen en Tsjechië ligt vlakbij. Pre 1989 zat je hier dus heel ver achter het IJzeren Gordijn en toen Heidenau in 1946 met de productie van tweewielerbanden begon was dat onder een compleet ander gesternte.
“Heidenau was altijd al een industriestad en voor de oorlog stond hier een oude rubberverwerkingsfabriek. Na de Tweede Wereldoorlog lag alles in puin en moest ook alles voor de mobiliteit van de bevolking opnieuw worden opgestart. De Sovjets beslisten om hier een bandenfabriek uit te baten, een bandenfabriek die van in het begin focuste op tweewielers. Zoveel decennia later focussen wij ons nog altijd op tweewielerbanden en in die lange geschiedenis en de tonnen ervaring die daaruit voorvloeien ligt onze sterkte”, vertelt salesmanager Pierre Schäffer als hij mij ontvangt.
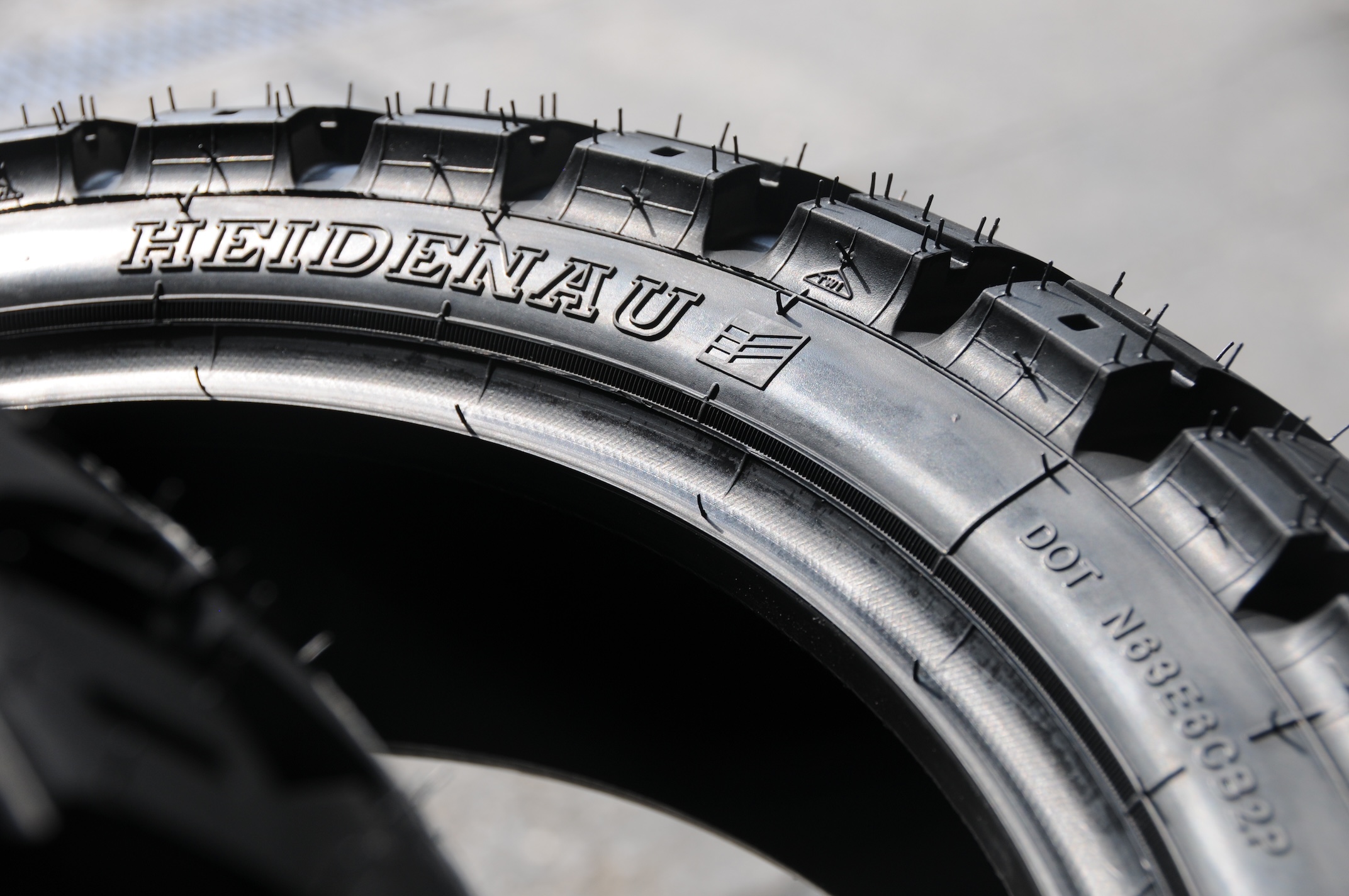
Overeind krabbelen
Van de laatste keer dat ik bij een grote bandenfabrikant was, herinner ik me dat ik bij de ingang een keer of zeven gescreend werd en dat pas daarna de slagboom omhoogging. Enkele minuten geleden heb ik aan een paar personeelsleden aan de entree van de Heidenau-site gevraagd waar ik mocht parkeren en kreeg ik ‘zet je maar voor het kantoor van de verkoopdirecteur’ als antwoord.
“Nee, wij zijn in niks te vergelijken met de grote bandenmerken die amper nog in Europa produceren. Allemaal zijn ze onderdeel van internationale groepen die bijna alle productie naar Azië hebben verhuisd. Daar kunnen ze enorme hoeveelheden banden aan bodemprijzen maken, daar kunnen wij niet tegenop.”
“Wij hebben van kleinere series en niches onze core business gemaakt en daarmee doen we het lang niet slecht. Toen de Muur in 1989 tegen de vlakte ging werkten hier achthonderd mensen. In de jaren daarna ging onze economie door een diep dal, maar wij hielden stand en krabbelden overeind. Momenteel werken er weer tweehonderd mensen voor Reifenwerk Heidenau, die dagelijks vierduizend banden produceren”, aldus Schäffer.
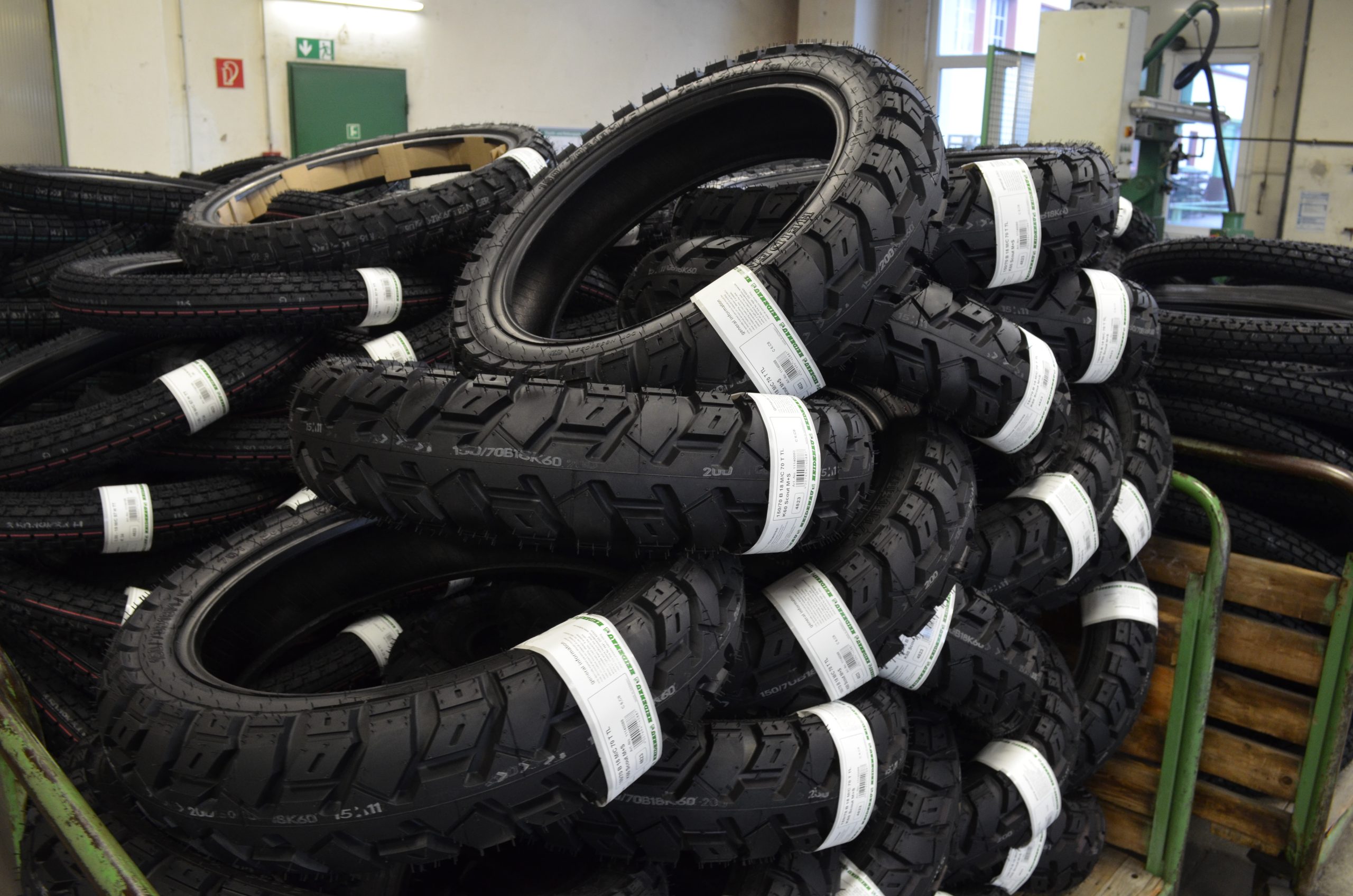
Let it snow
Dat Heidenau de val van de Muur overleefde, heeft het bandenmerk deels te danken aan de scooter die in de jaren negentig heel populair werd. Net dat type tweewieler waarvoor Heidenau aardig wat banden in de catalogus had. En in 2002 kwam er een bijzonder nicheproduct bij.
Pierre Schäffer: “Wij waren de eerste fabrikant die een winterband voor scooters maakte en de Zwitserse post koopt die banden al twintig jaar bij ons om op de scooters van de postbodes te leggen. Heel veel andere bandenfabrikanten kwamen na ons met een gelijkaardige band, maar de meesten zijn daar alweer mee gestopt omdat de aantallen te klein zijn om in hun bedrijfsmodel rendabel te zijn. Voor ons is het perfect.”
Toen Heidenau in 2013 met de Scout op de markt kwam was dat de eerste allroadband met het Mud/Snow-label, een band die tien jaar later als K60 in drie varianten in het gamma zit en die we straks in de productie ook zullen tegenkomen. De productie in Heidenau is over verschillende gebouwen op het terrein verdeeld.
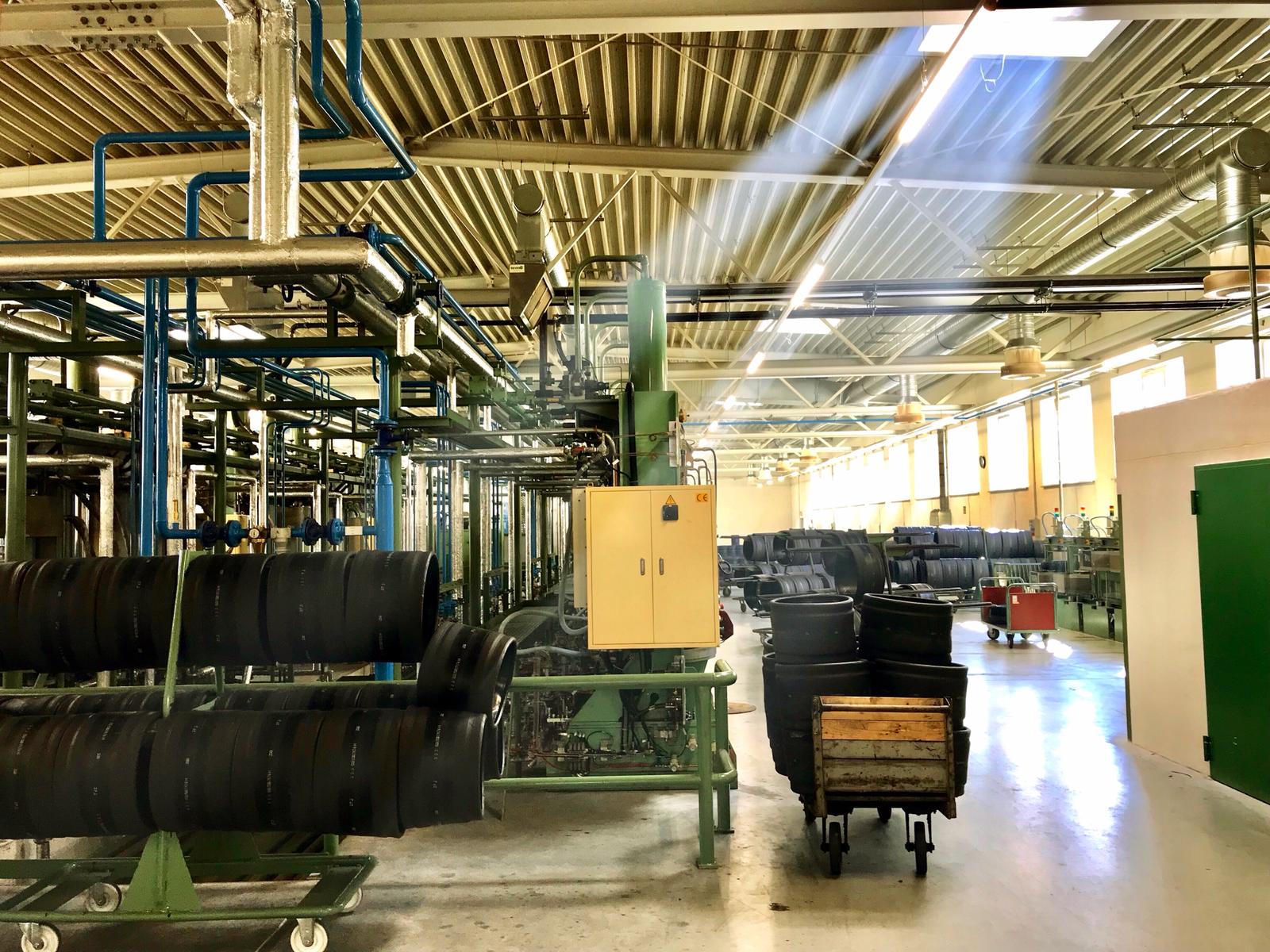
Sommige panden staan er al bijna tachtig jaar, andere zijn nagelnieuw: het bewijs dat hier de voorbije decennia wel degelijk nog geïnvesteerd is. De directe toegang naar het treinstation van Heidenau – inclusief laadkade waar de banden naar alle uithoeken van de Sovjet-Unie werden verstuurd – is er niet meer, die tijden zijn definitief voorbij.
Recept
Tijd voor gebouw nummer één, waar het lekker warm is en dat ondanks het feit dat het rubbermengsel hier koud geëxtrudeerd wordt. “Het rubbermengsel komt hier kant-en-klaar aan van een Europese onderaannemer die het volgens onze receptuur maakt. Zo’n recept is hypercomplex en de compound van een band kan wel duizend ingrediënten bevatten.”
“Sommige elementen komen het rijgedrag van de band ten goede, maar er zitten evengoed stoffen in die bijvoorbeeld het verouderingsproces van de band vertragen. Die recepten worden bij ons op punt gesteld en alle compounds die binnenkomen worden in het labo getest om te controleren of ze aan de vereisten voldoen”, legt Pierre uit.
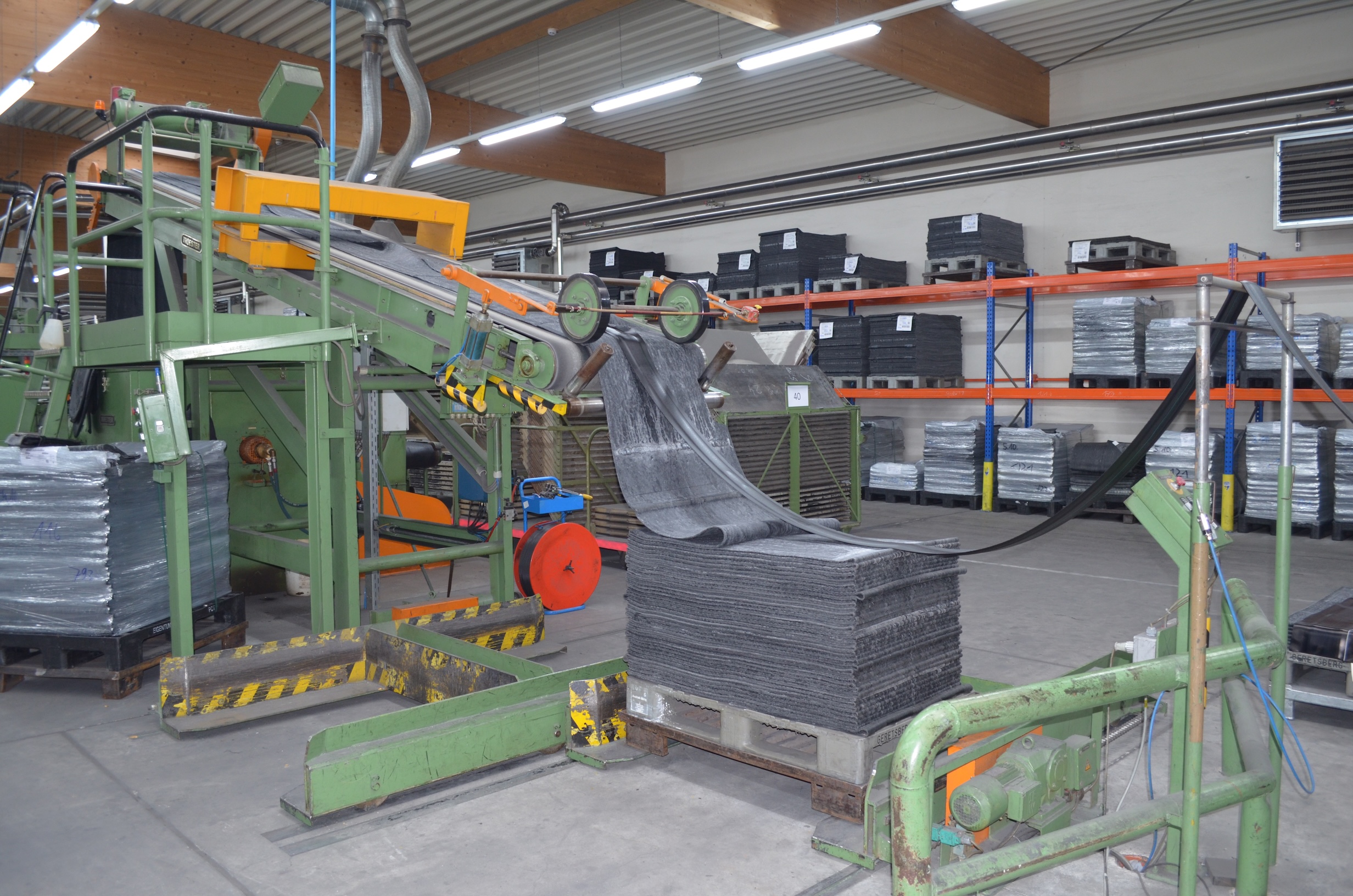
Hij gaat van bij het begin van de rondleiding geen thema uit de weg en ook de ecologische kant van de zaak komt aan bod. “Je mag niet om het even wat in die rubbermix gooien, tijdens het gebruik verslijt een band en komen er minuscule deeltjes in de lucht terecht die ingeademd kunnen worden. Ik verwacht dat in de toekomst meer onderdelen van de auto of motor aan emissienormen onderhevig zullen zijn. Ik denk aan banden en bijvoorbeeld remblokken”, aldus de verkoopdirecteur.
Brievenbus
De gigantische vellen compound zijn in harmonicastijl opgevouwen en worden zo de extrusiemachine in getrokken. Die machine perst het rubbermengsel door een aantal trechters en de kracht waarmee dat gebeurt zorgt ervoor dat het rubber een beetje warmer en dus soepeler wordt. Op het einde van de machine wordt het rubber door een soort van brievenbus geperst en krijg je een hele lange lap rubber die in het midden dikker is dan aan de zijkanten: dit wordt straks het loopvlak.
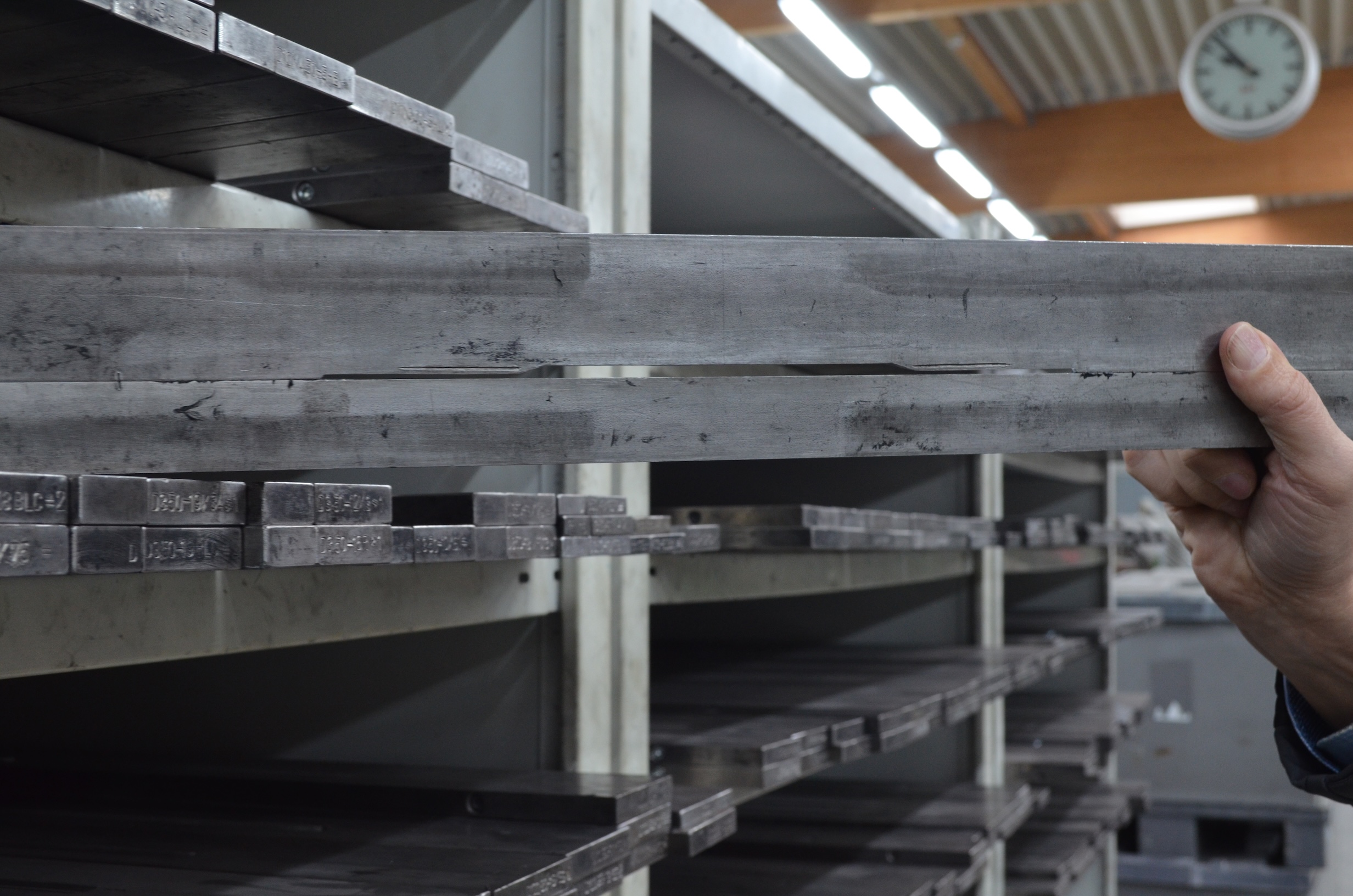
De vorm van de ‘brievenbus’ bepaalt hoe dik en hoe breed de lap rubber is, voor elk type band heeft Heidenau dus een andere mal of ‘brievenbus’. Door drie vellen compound gelijktijdig door de machine te persen (links – midden – rechts) kan Heidenau dual compound banden maken die een centraal loopvlak van wat harder rubber hebben in functie van de levensduur, terwijl het rubber op de zijkanten van de band zachter is en dus meer grip geeft. De lange lap rubber wordt in water gekoeld en op lengte gesneden.
“Na het afkoelen krimpt het stuk rubber nog een beetje. Mochten we de repen te vroeg snijden, dan zou het loopvlak van een band nooit passen.” Sommige racecompounds zijn sowieso te zacht om machinaal te snijden en moeten dus met de hand op de juiste lengte worden afgesneden. Alle repen worden opzijgelegd om te wachten op de samenstelling van de band.
Fret je (kar)kas niet op
De volgende stap is de voorbereiding van het karkas en dat begint bij de hieldraden. Daarvoor gebruikt Heidenau altijd dezelfde staaldraad, een 0,89 mm dikke draad uit een legering van staal met brons om het metaal voldoende corrosiebestendig te maken. Afhankelijk van de belasting van de band wordt de hieldraad uit meerdere staaldraden en uit meerdere wikkelingen gebouwd.
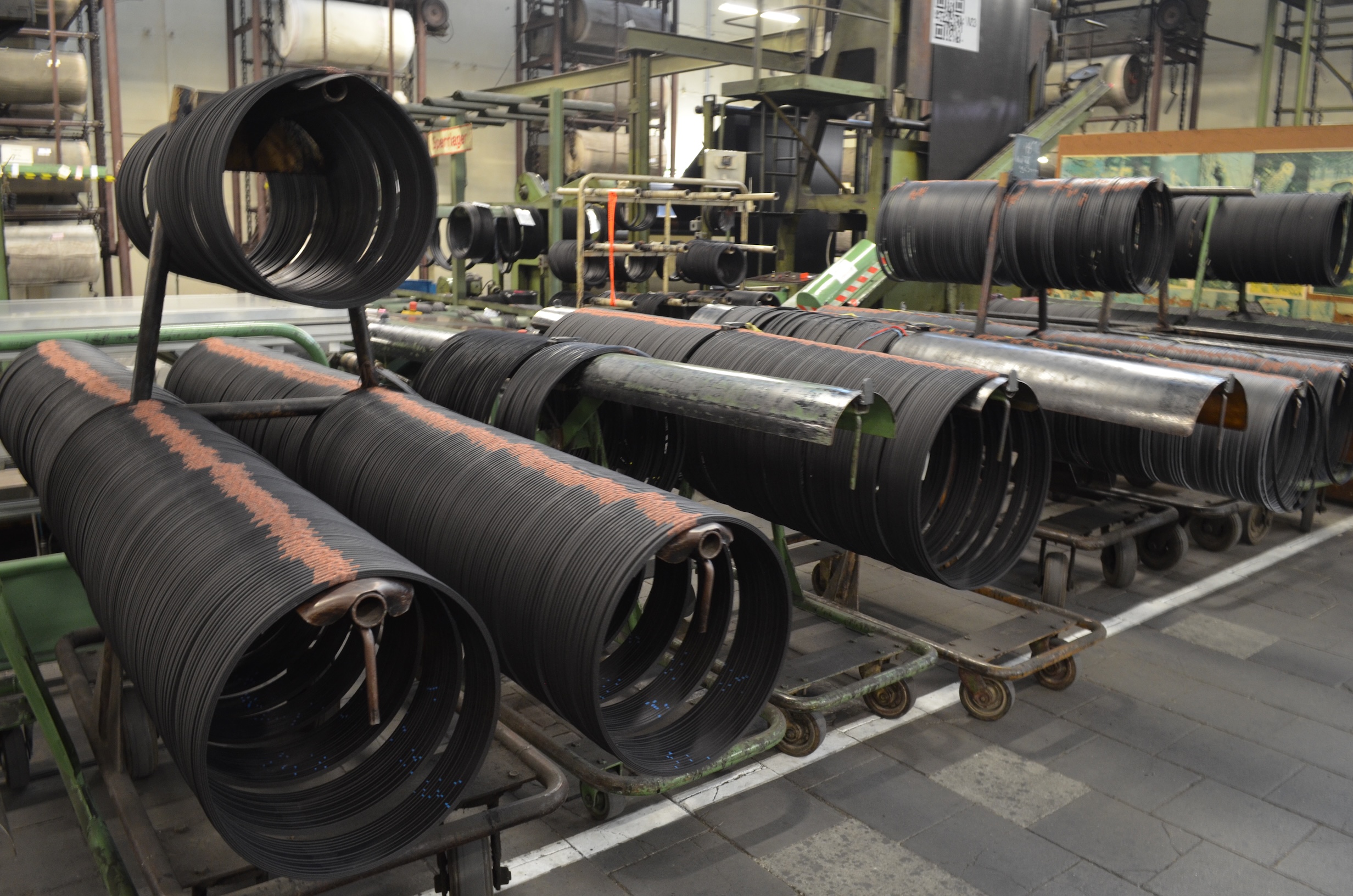
Een ‘3×3’ hieldraad wil zeggen dat er drie staaldraden in één bundel worden samengebracht (zo’n bundel staaldraden wordt in een rubber coating gestopt) en dat de hieldraad drie keer gewikkeld is. Voor de Scout achterbanden gaat Heidenau voor de zwaarste hieldraad, een ‘4×4’ exemplaar. Hier zitten dus vier 0,89 mm staaldraden in één bundel en wordt de gecoate bundel vier keer rond de mal gedraaid om de hieldraad te maken.
De hieldraden komen straks aan de zijkanten van het karkas te zitten, een karkas dat bestaat uit meerdere lagen polyamide dat in een gigantische pers met rubber is geïmpregneerd. Die grote vellen worden in een parallellogramvorm gesneden en dat gebeurt met de grootste precisie op een gerobotiseerde snijtafel.
Diagonaal
“Wij bouwen bij Heidenau enkel diagonaalbanden, dat zijn banden waarbij de verschillende lagen karkasweefsel diagonaal over mekaar worden gelegd. Diagonaalbanden hebben het grote voordeel dat ze bij snelheden tot tweehonderd kilometer per uur veel meer demping en comfort geven. De hoek waaronder de stukken karkasweefsel gesneden worden, bepaalt het comfort dat het karkas en bij uitbreiding de hele band zal geven. Hoe stomper de hoek, hoe soepeler de band. Hoe scherper de hoek, hoe stabieler de band”, doceert Pierre.
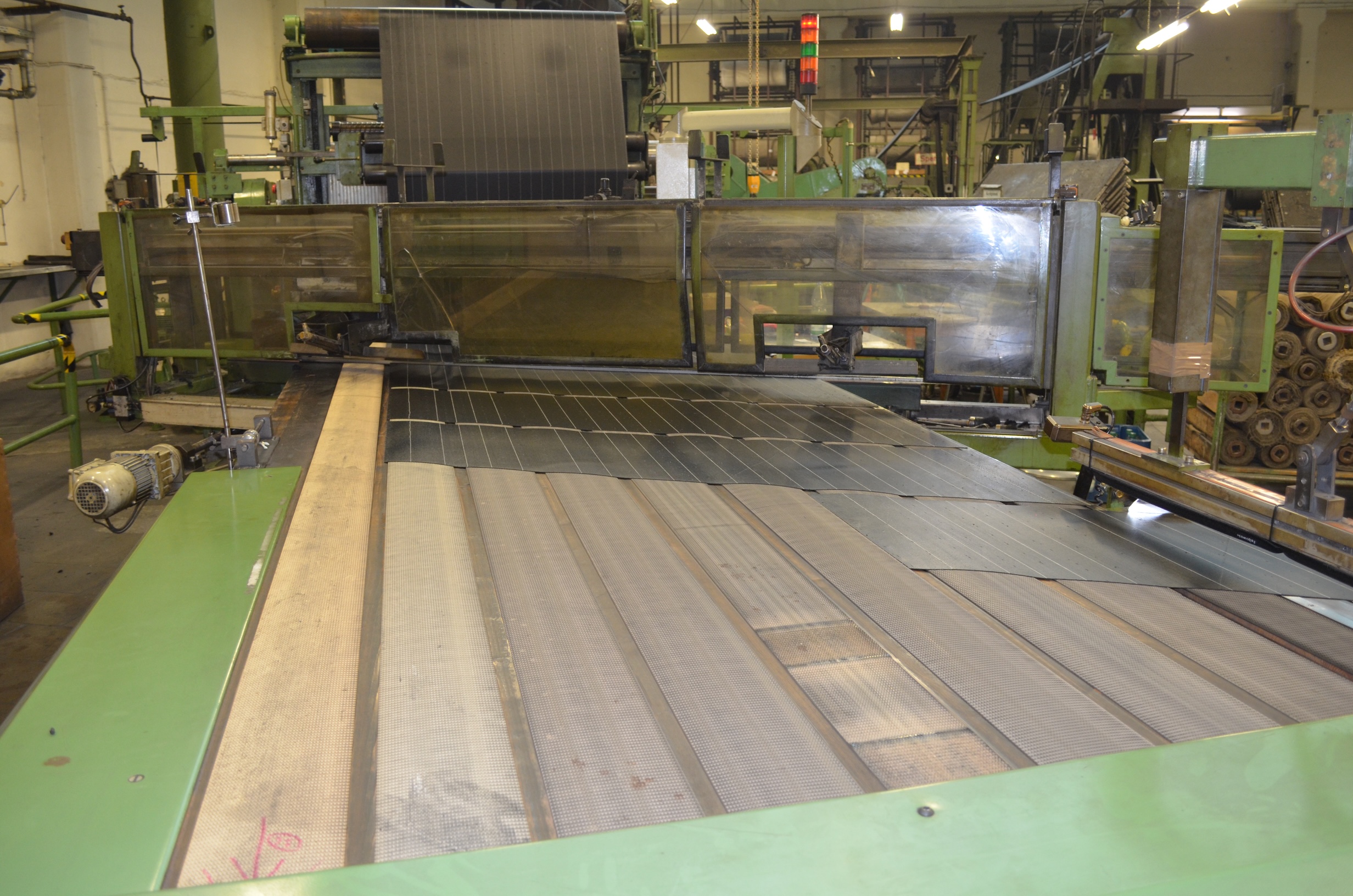
De tubeless banden krijgen een extra laag van een synthetische stof met een heel hoge dichtheid, deze laag wordt dicht tegen de luchtkamer van de velg in de band geplaatst om de band perfect luchtdicht te maken. Ook deze repen synthetisch materiaal moeten op de juiste breedte worden gesneden, afhankelijk van de maat van de band. Nog een stukje handwerk.
Stop de persen!
Met alle onderdelen van de band klaar is het tijd voor de montage, die op een soort van draaibank gebeurt. Op die draaibank zit een cilinder waarrond de verschillende onderdelen van de band worden gewikkeld. De arbeider in kwestie weet hoeveel lagen hij van het karkas moet aanbrengen, groene lasers geven aan waar hij moet snijden waarbij de hoeken altijd anders zijn. De hieldraden worden op de uiteinden geplaatst waarna een paar lagen van het karkas worden omgeplooid zodat de hieldraden erin vastzitten.
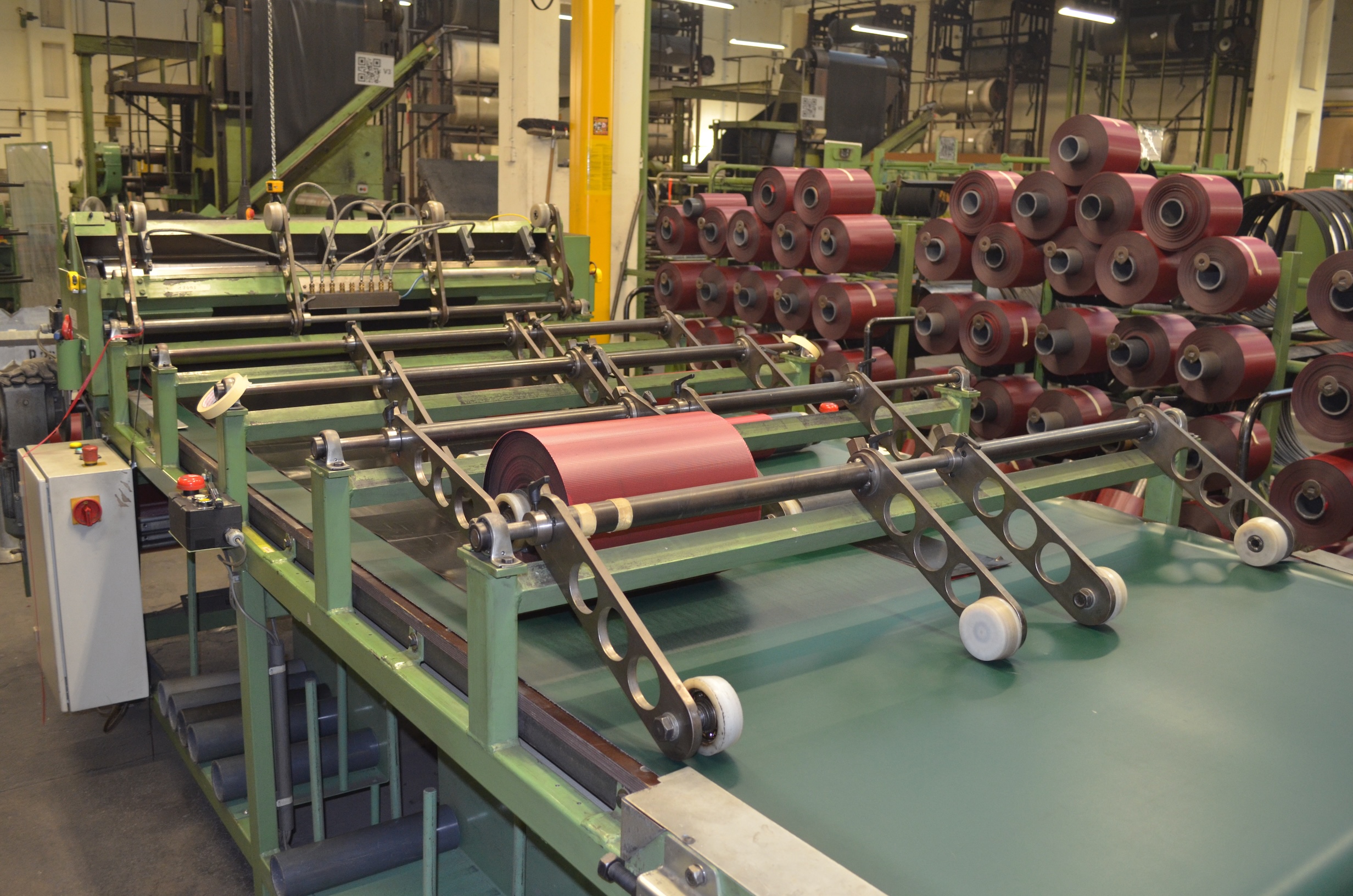
De verschillende karkaslagen worden zowel machinaal als manueel aangedrukt om alle luchtbellen er tussenuit te persen en om de band over de hele oppervlakte zo egaal mogelijk te krijgen. Als laatste wordt het loopvlak erop gelegd en is de band klaar om geperst te worden. Daarvoor heeft Heidenau een honderdtal persen staan, die 24 uur per dag bediend worden.
“In de rest van de productie werken we in twee ploegen, vijf dagen in de week. In de persafdeling werken we het klokje rond omdat dit het meest tijdrovende gedeelte van het productieproces is. Het is tegelijk ook de duurste stap in de productie omdat we hiervoor enorm veel energie nodig hebben”, legt Schäffer uit.
Afbakken
Voor alle banden (soort en maat band) heeft Heidenau een aparte mal, al worden sommige varianten in eenzelfde mal gebouwd. Om de verschillen aan te duiden worden de kentekenplaatjes in de mal dan verwisseld, dat moet sowieso voor de plaatjes die aangeven in welke week van welk jaar de band in kwestie gebouwd is. De mal bestaat uit een boven- en een onderkant, de kern van de machine is een balg die met hete lucht wordt gevuld.
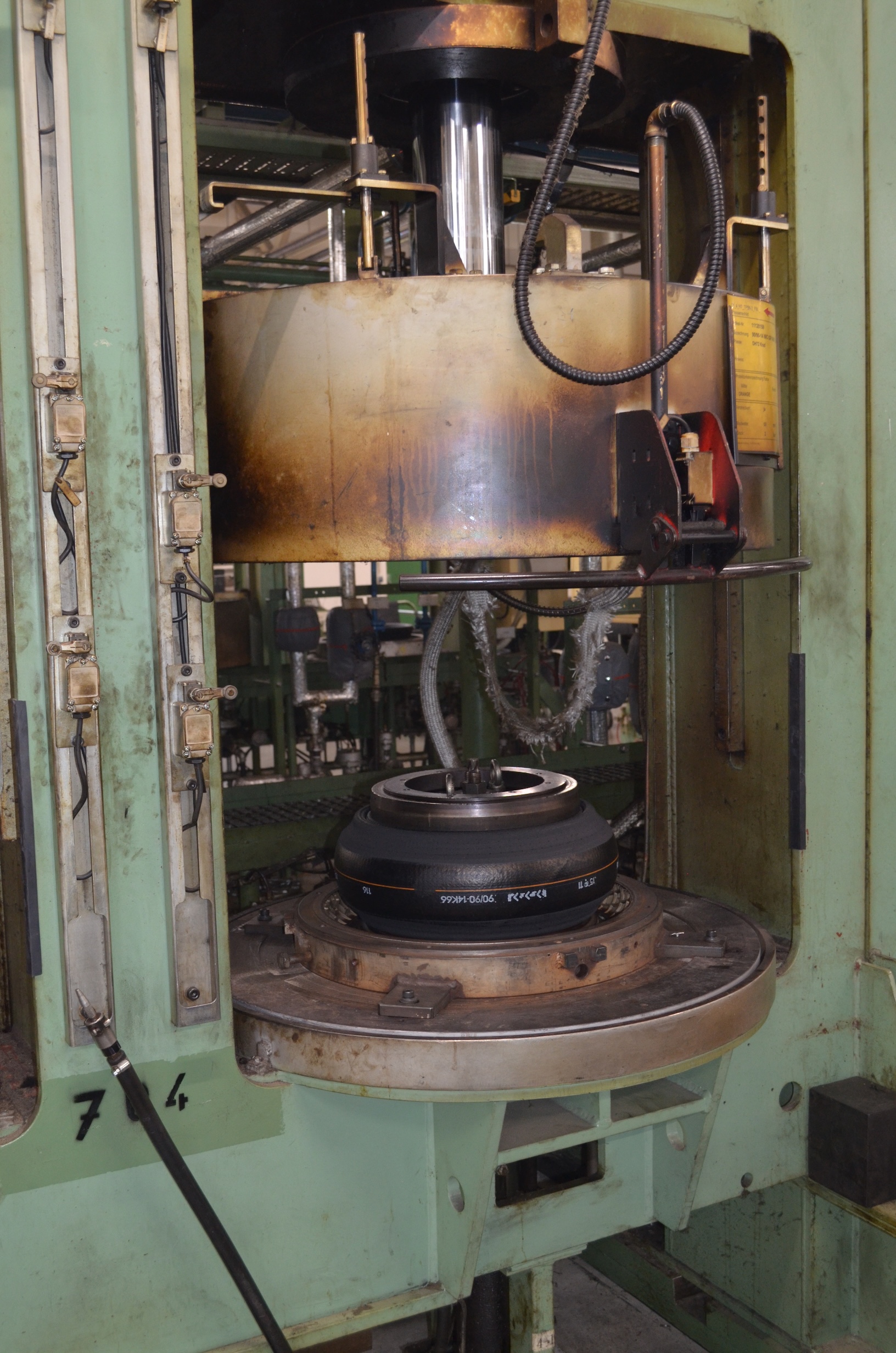
De voorgevormde band wordt in de onderkant van de mal gelegd en van zodra de pers dicht is, wordt de temperatuur en de druk in de balg opgevoerd. Voor sommige banden volstaat twaalf bar druk in de centrale balg, andere hebben zestien bar nodig. Sommige banden worden op 160° afgebakken en zijn klaar op vijftien minuten, andere hebben een halfuur op 170° nodig. En zo is elke band anders.
“Het is de warmte die voor de vulkanisatie zorgt. Voor het afbakken is het niet veel meer dan een pak slap rubber, na de vulkanisatie heeft de band een stabiele vorm aangenomen”, nog volgens de verkoopdirecteur.
Lichtjes
In een laatste stap worden de banden in een uitbalanceermachine gemonteerd, vergelijkbaar met wat de bandenboer bij jou om de hoek heeft staan. “Hier gaan we op zoek naar het lichtste punt van de band en duiden we dat aan met een rood puntje. Dat kan handig zijn voor de persoon die de banden gaat monteren, als de velg honderd procent recht en rond is zet hij het ventiel bij voorkeur tegenover het rode puntje om op die manier het wiel al voor een deel uit te balanceren.”
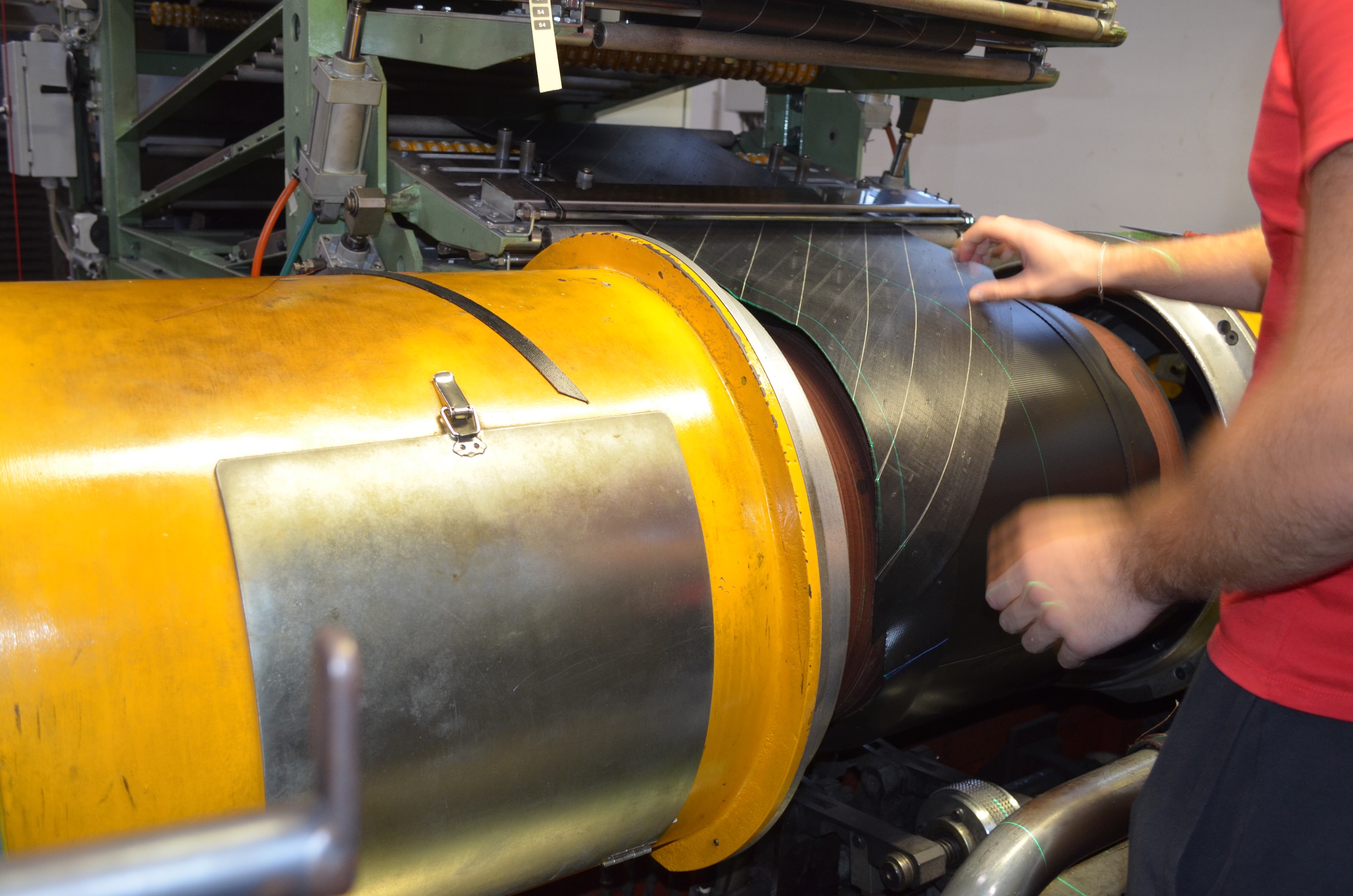
“Tijdens deze stap controleren we de band ook op onregelmatigheden. Omdat we tijdens de verschillende stappen in het productieproces zo nauwgezet te werk gaan en omdat we zoveel ervaring hebben, zit bij ons het percentage uitval onder de procent. Dus van elke honderd banden die we produceren, wordt er bij de kwaliteitscontrole hoogstens ééntje afgekeurd”, meldt Pierre trots.
Als we door de stockageruimte lopen, komt Schäffer ineens met een verzoek op de proppen. “Doe me een plezier en schrijf dat de productiedatum van een band slechts heel relatieve informatie geeft voor de koper. In Duitsland wordt er steeds weer op gehamerd dat mensen banden moeten kopen die zo recent mogelijk geproduceerd zijn, maar eigenlijk is dat slechts de helft van het verhaal. Als je een band in een donkere ruimte bewaart, ver van alle uv-straling, dan kan je hem heel lang bewaren zonder dat hij zijn eigenschappen verliest. Omgekeerd geldt ook: leg een band een jaar in de volle zon buiten en het beste zal er al van af zijn.”
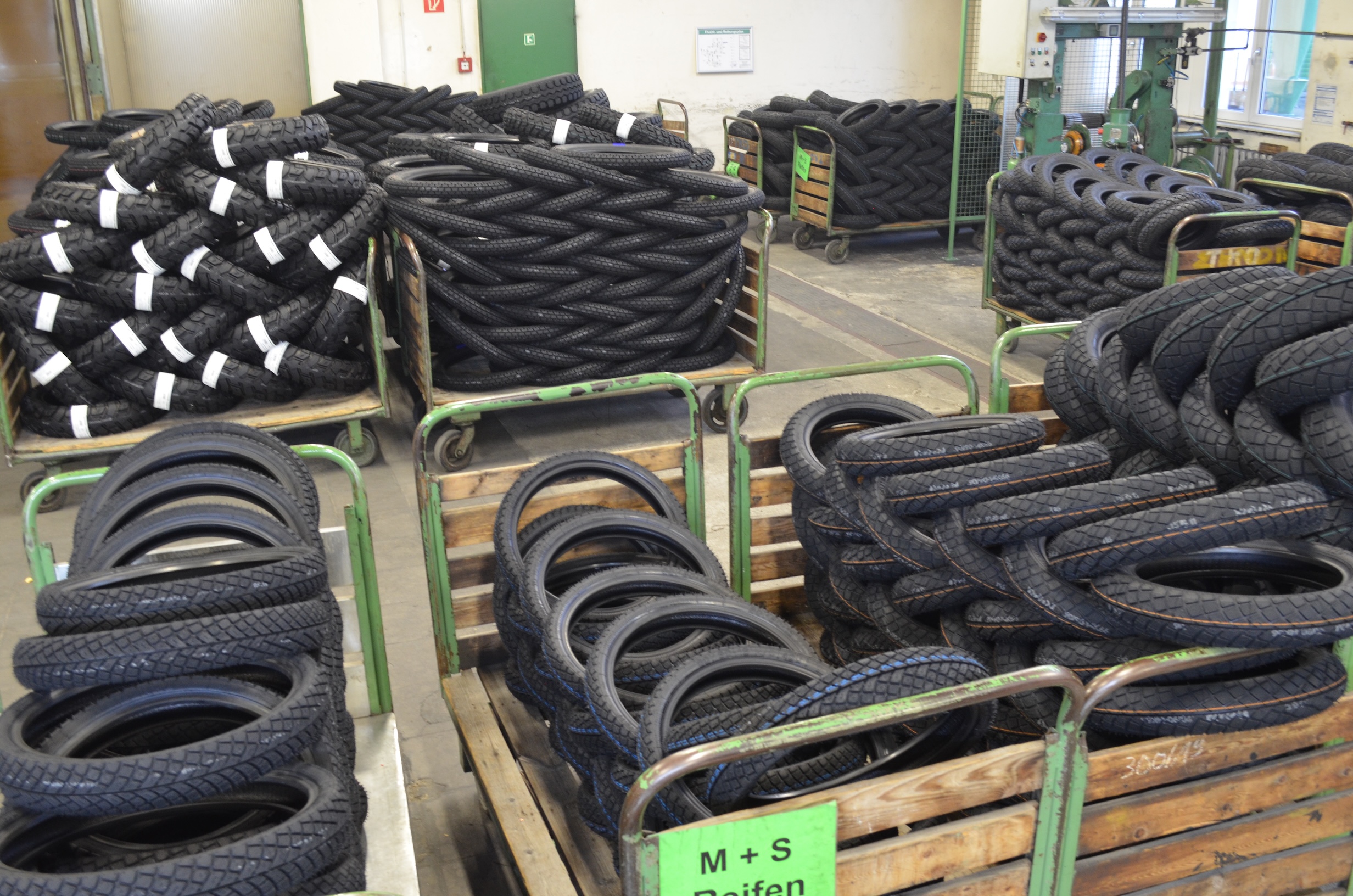
Toekomst
Met nog een ommetje langs het gebouw waar de ingenieurs hun werk doen (banden lopen er duizenden kilometers op rollenbanken en onnoemelijk veel mogelijke compounds worden er getest) komen we terug in Schäffers bescheiden kantoor uit waar we bij nog een laatste kop koffie even in de toekomst blikken. De man heeft er vertrouwen in.
“Als we ons blijven focussen op de kleine series die voor de grote fabrikanten niet interessant zijn, hebben we zeker onze plaats in de markt. Ook al is het om heel veel verschillende redenen niet evident om alles in Duitsland te doen. Wij betalen al onze belastingen in Duitsland. We schikken ons naar de strenge Europese milieuwetgeving.”
“De energie die nodig is om een band te maken kost handenvol geld en er kruipt ook gewoon heel veel materiaal in een band. Maar alles wat rijdt heeft nu eenmaal een band nodig. Maakt niet uit of jouw motor straks door een verbrandingsmotor of een elektromotor wordt aangedreven: als je wil rijden, dan heb je banden nodig. En daarvoor is en blijft de luchtband de allerbeste oplossing.”
Check de vernieuwde Heidenau website
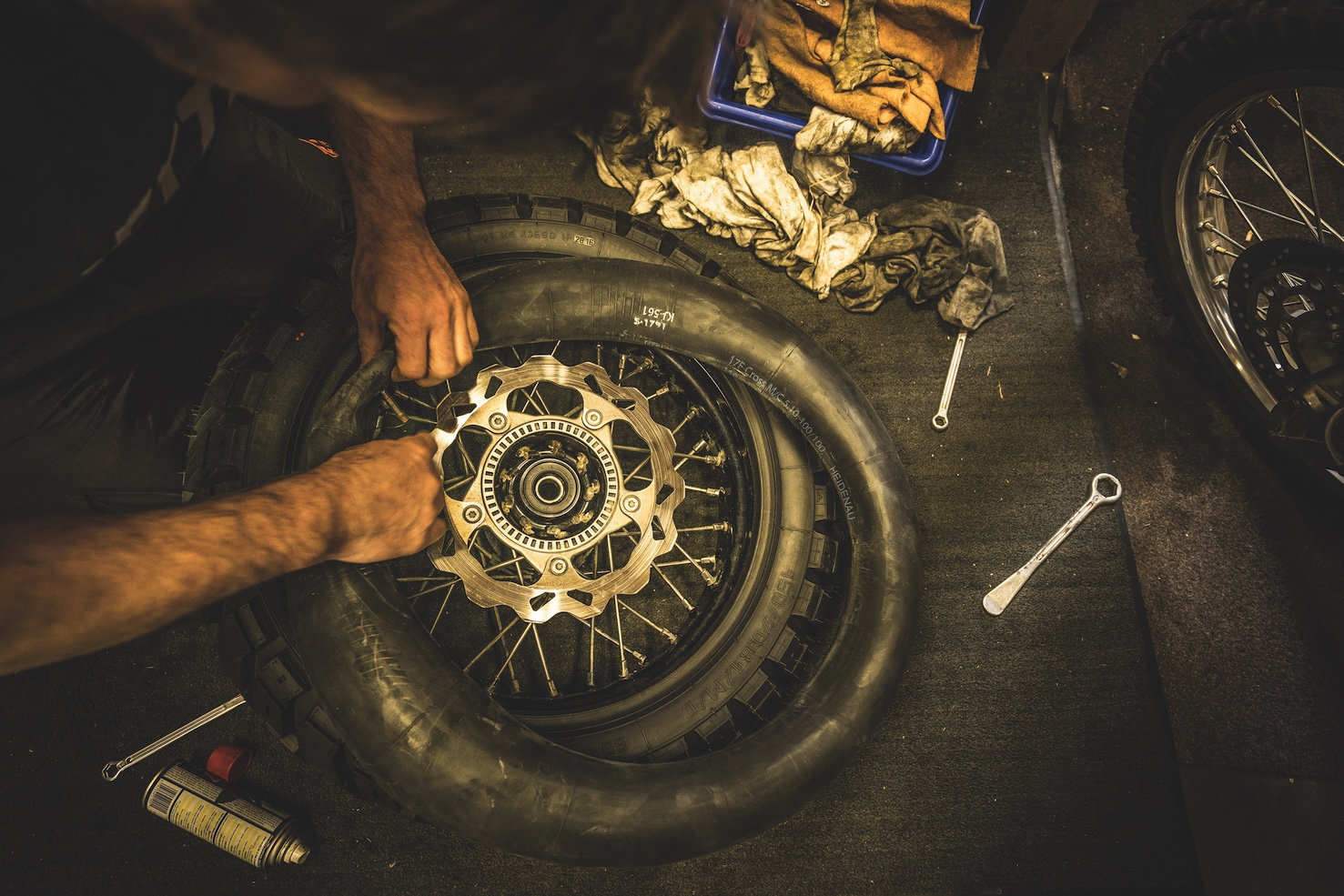
Tekst Bart De Schampheleire • Fotografie Bart De Schampheleire, Heidenau