Met de zomervakantie in het vooruitzicht tuigen we met z’n allen onze motoren terug op om eropuit te trekken, al is dat niet altijd even evident want niet elke motor is standaard voorzien van een kofferset. Givi en Kappa zijn specialist op vlak van bagagesystemen voor motorfietsen, al blijkt het een verduiveld complexe business om te runnen. Dat leer ik als Giampaolo Deambrogi me door de verschillende fabrieken in het Italiaanse Flero loodst.
Na de obligate koffie in het hoofdgebouw – dit is nu eenmaal Italië – stappen we meteen in de auto. Ik grijp gelijk mijn kans om Deambrogi te vragen hoe Givi ooit begon en hoe we de relatie tussen Givi en Kappa moeten inschatten. Want hoewel het Kappa-logo nergens in de hoofdzetel te bespeuren valt, zeilen de merknamen Givi en Kappa wel degelijk onder dezelfde vlag.
“Giuseppe Visenzi was in de tijd van Read en Agostini een verdienstelijk motorracer, maar aan elke racecarrière komt een einde, zo ook aan die van Visenzi. Zijn plan was om een motorwinkel te openen, al leverde dat bij de eerste onderhandelingen met Honda een vrij lachwekkende situatie op. ‘De CB750 is de speerpunt van onze collectie, hoeveel wil je er daarvan bestellen?’ vroeg Honda Italië, waarop Visenzi aarzelend ‘Eentje?’ antwoordde. Die ene CB750 had Visenzi al op de eerste dag verkocht in zijn motorwinkel, dus ging hij door met Honda.
Toen de Goldwing GL1000 op de markt verscheen, sloeg die motor niet meteen aan omdat er geen bagagesysteem voor was. Giuseppe Visenzi besloot het rek dan maar zelf in mekaar te knutselen en toonde zijn oplossing op de Eicma van 1970. De Zwitserse importeur van Honda merkte het systeem op en besloot er meteen honderd stuks van te bestellen. Enig probleem: Visenzi had nog geen fabriek, laat staan een productielijn voor bagagesystemen. Maar hij zag wel meteen het potentieel van die markt en besloot er vol voor te gaan.
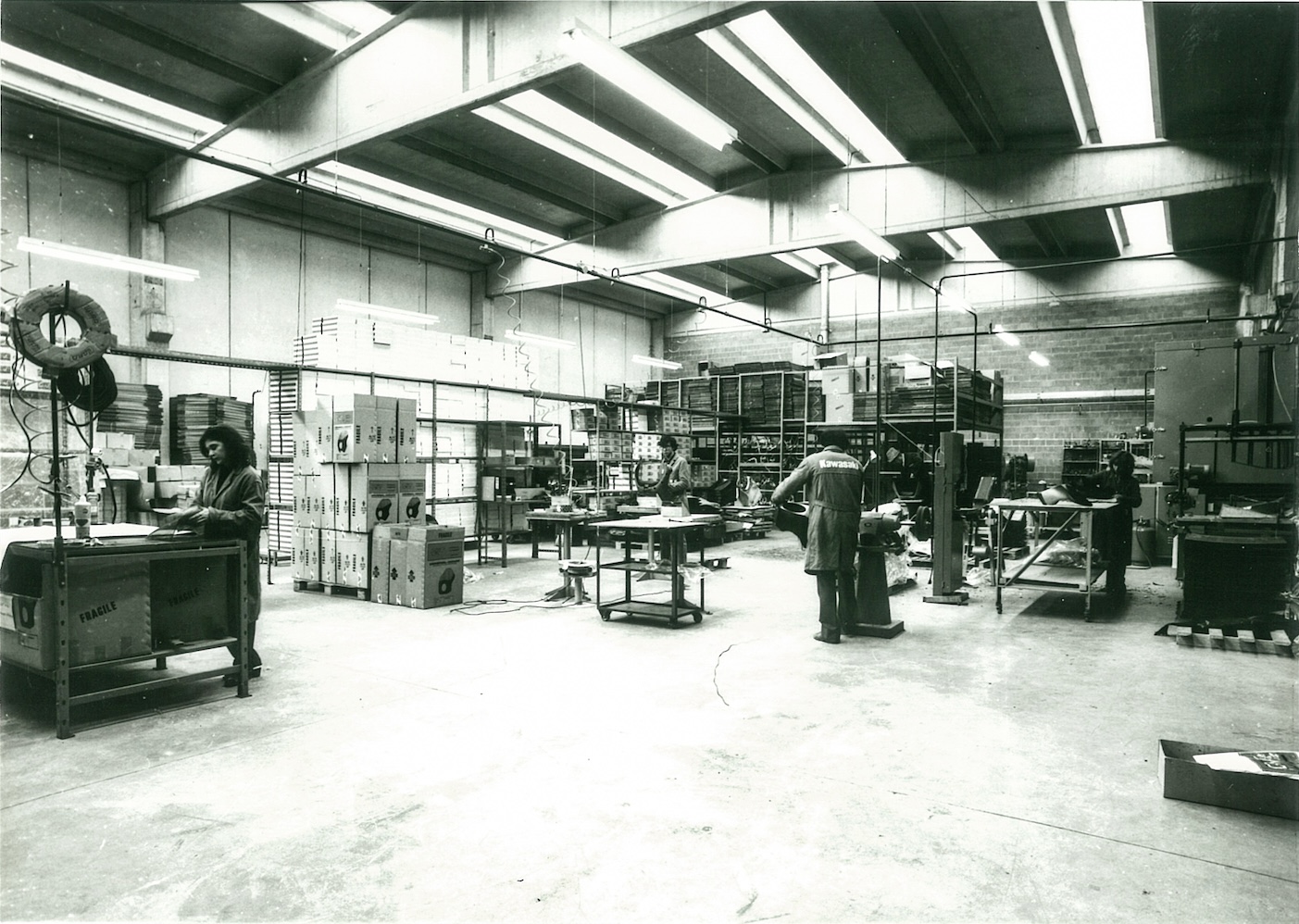
Hij richtte Givi op en breidde het bedrijf in de loop der jaren gevoelig uit. Zo kwam ook Kappa bij Givi terecht en werd er besloten om de beide merken naast elkaar te laten bestaan. We proberen Givi iets hoger in de markt te positioneren dan Kappa, al zijn de verschillen tussen de producten gering”, ratelt de Aftermarket Sales Director.
De soft luggage systemen en de helmen worden elders geproduceerd, in Flero concentreren Givi en de talrijke onderaannemers zich op de ontwikkeling en productie van de harde bagagekoffers (in kunststof en aluminium) en de ophangsystemen van die koffers. Een complexe aangelegenheid.
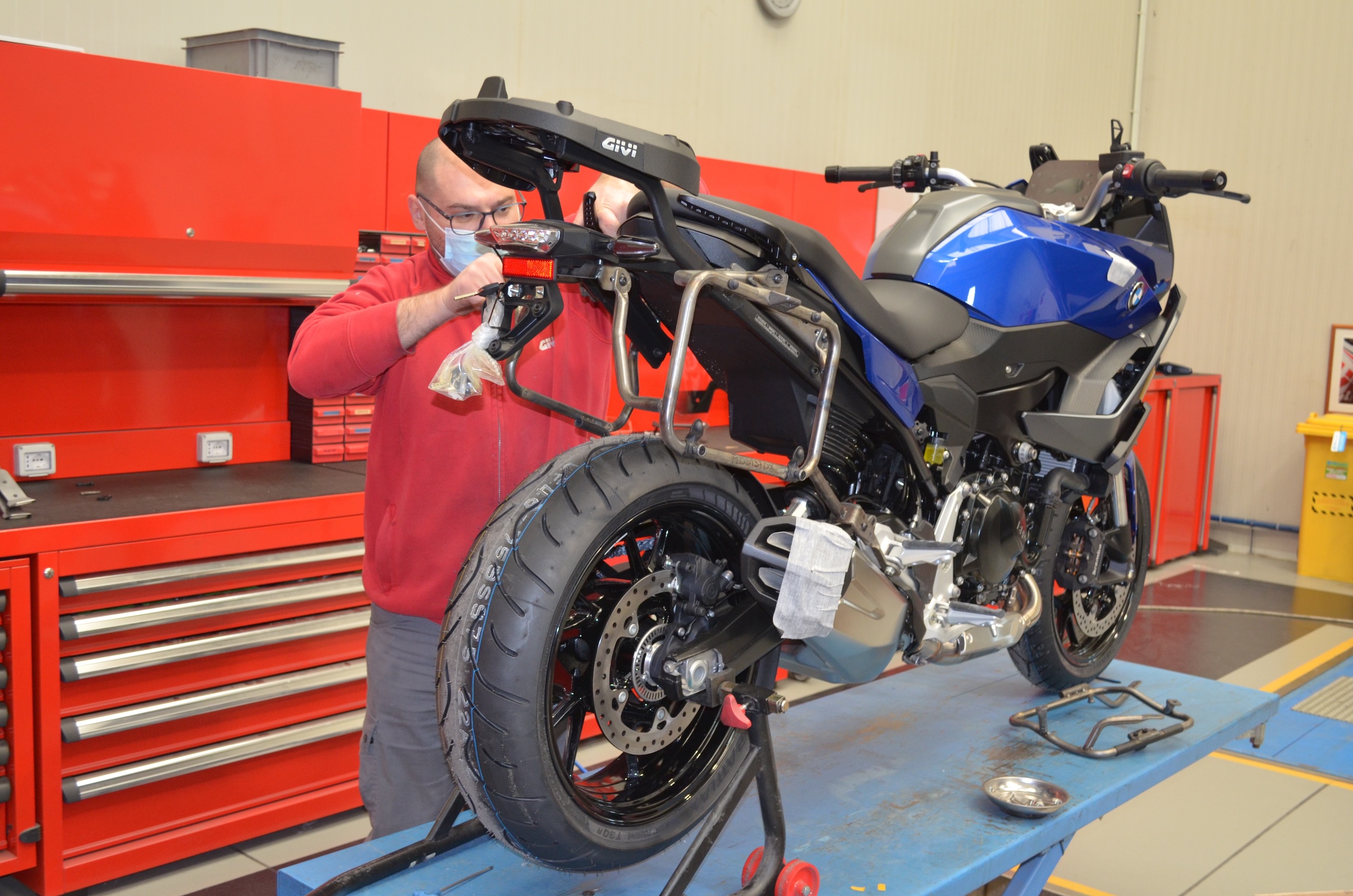
Deambrogi: “Elke koffer bestaat uit minstens vijftig onderdelen, wat betekent dat we voor al die onderdelen een mal moeten maken. Vandaar dat we bij elke ontwikkeling van een nieuw product onderzoeken hoe we weliswaar iets nieuws kunnen maken, maar daarbij toch een aantal bestaande onderdelen kunnen hergebruiken. Omdat we voor al dat spuitgietwerk van de kunststof onderdelen mallen moeten maken, hebben we een eigen mallenmakerij. Drie personen zijn voltijds bezig met de programmering van de vijfassige freesmachines voor onze eigen mallen. Die mallen zijn voor ons een gigantische kost, we stockeren ze dan ook met de grootste zorg. Om de mallen op te slaan maken we gebruik van een soort roterend magazijn, anders zouden we veel te veel plaats nodig hebben.”
In de aanpalende bedrijfshal worden alle kunststof delen geproduceerd. Vijf spuitgietmachines voor de grote onderdelen zoals kofferdeksels staan er naast zeven machines die aan een duizelingwekkend tempo kleine plastic delen uitspuwen. De grote onderdelen worden met zuignappen uit de mal gehaald en op een transportband gelegd waar ze tijd krijgen om af te koelen, de kleine onderdelen vallen in een soort van conische koker waarin ze nog een paar rondjes draaien om koud en vormvast te worden.
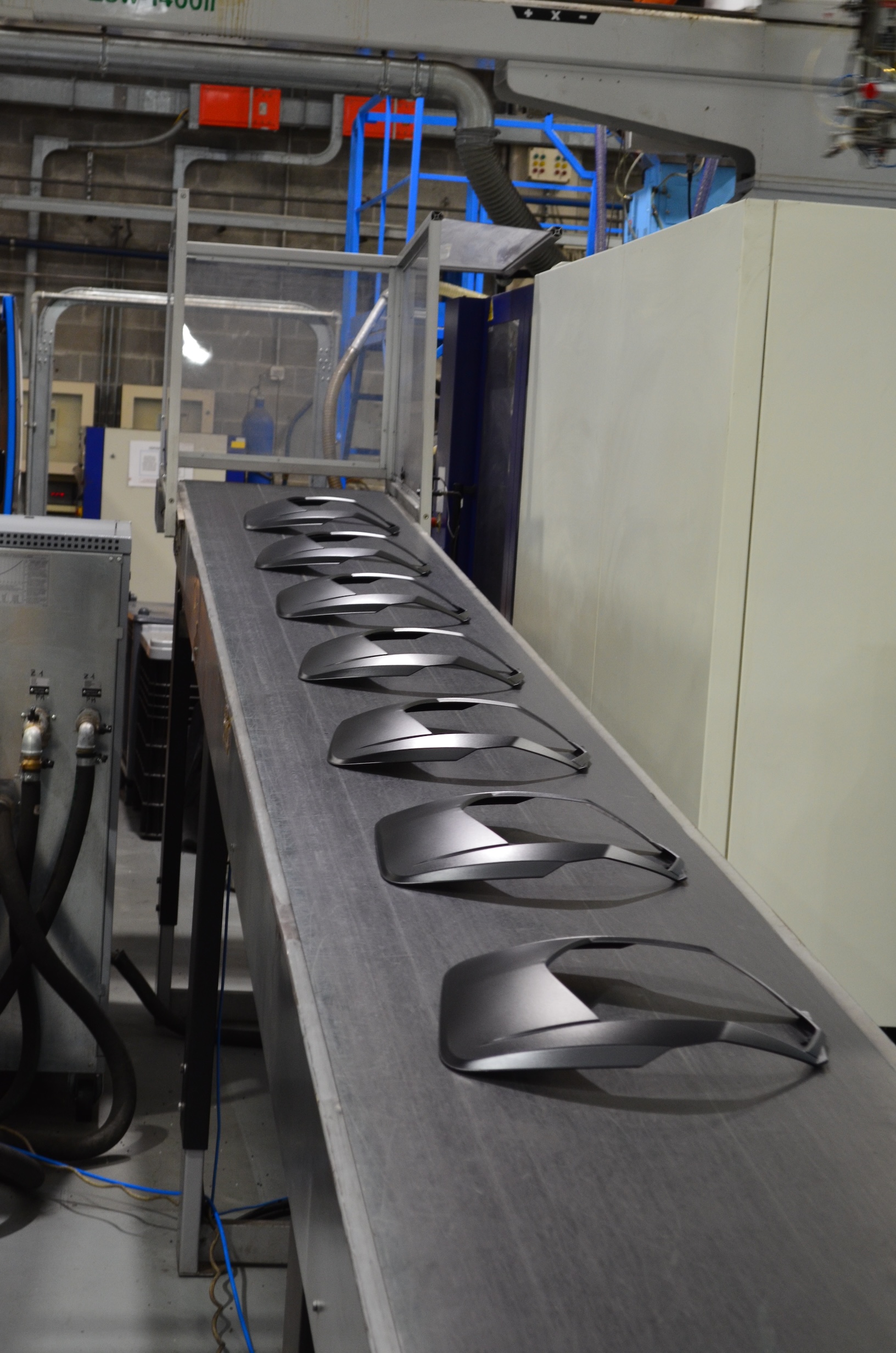
“Een mal wisselen duurt ongeveer anderhalf uur, nog een reden om bij de ontwikkeling van nieuwe producten te proberen om zo veel mogelijk bestaande onderdelen te gebruiken. Anders ben je vooral bezig met mallen wisselen in plaats van produceren. Merk trouwens op dat de mallen voor de grote onderdelen soms in meerdere delen opengaan. Mocht dat niet zo zijn, je zou de onderdelen niet meer uit de mal krijgen”, vertelt Deambrogi terwijl we langs de silo’s met het basismateriaal stappen.
Allemaal kunststoffen, uiteraard, maar in functie van de belasting van het onderdeel in kwestie wordt voor verschillende materialen gekozen. Zo mag een deksel van een topkoffer nog een beetje souplesse hebben om te voorkomen dat het item meteen stuk springt als je de koffer per ongeluk uit je handen laat glippen. Andere onderdelen worden van kunststof gemaakt die met vezels zijn versterkt.
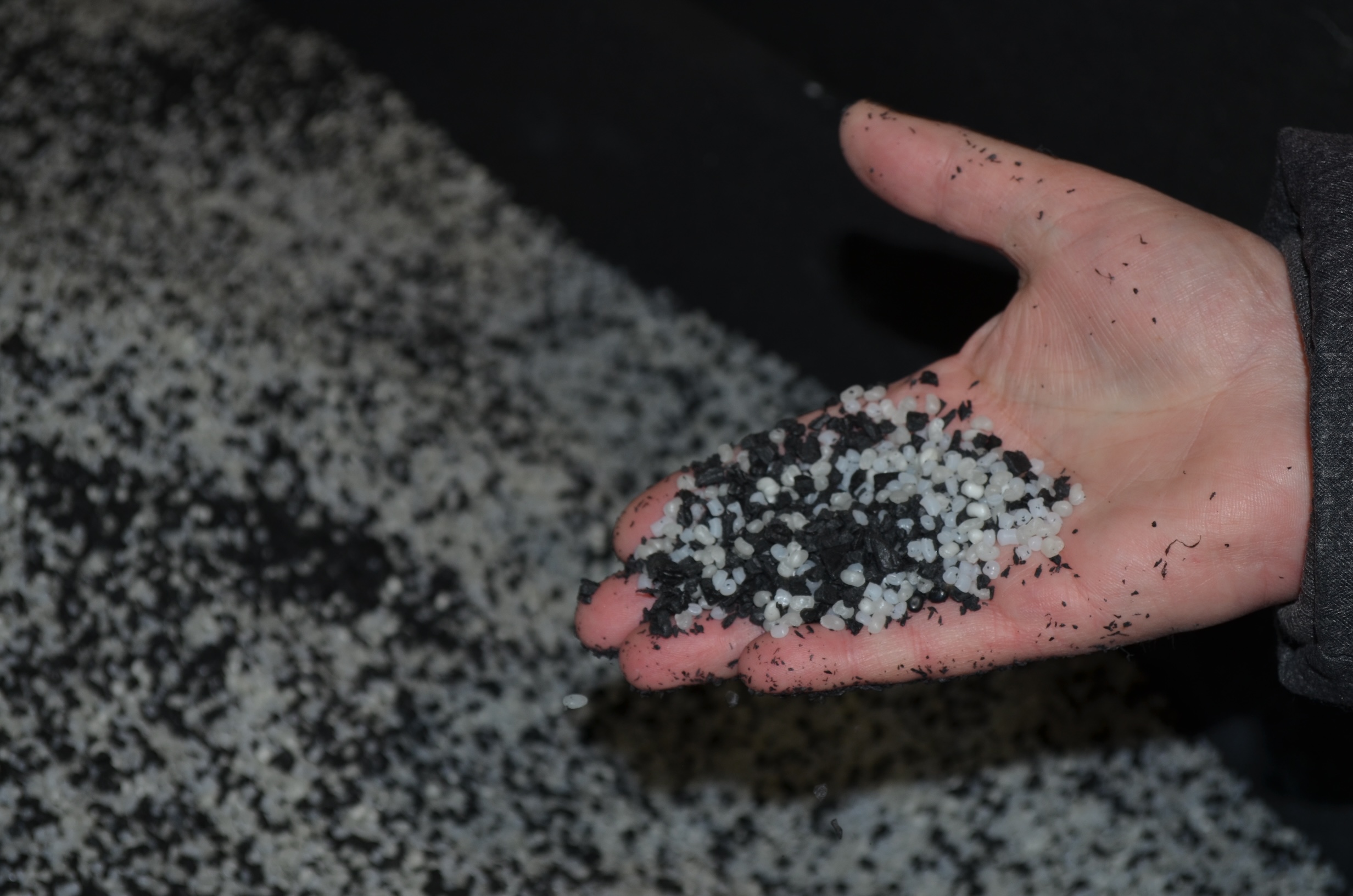
De Aftermarket Sales Director weet dat iedereen die tegenwoordig met plastic en kunststof werkt met een scheef oog bekeken wordt en hij wil niks liever dan ook de producten van Givi en Kappa groener maken. Dat is echter veel minder vanzelfsprekend dan je op het eerste gezicht zou denken. Giampaolo legt uit: “Momenteel gebruiken we voor onze kunststof onderdelen enkel virgin material, 100 % nieuwe grondstoffen dus waar geen gerecycleerd materiaal aan toegevoegd is. Omdat we van dat virgin material perfect weten hoe het zich laat verwerken en hoe het veroudert.
Als we zomaar een percentage gerecycleerd materiaal zouden toevoegen, dan moeten we onze mallen daaraan aanpassen én moeten we eerst onderzoeken hoe die gerecycleerde materialen verouderen. We willen producten afleveren die de consument jarenlang kan gebruiken, dus moeten we daar de nodige studies rond doen. We zijn daar trouwens mee bezig, maar het is een werk van lange adem.”
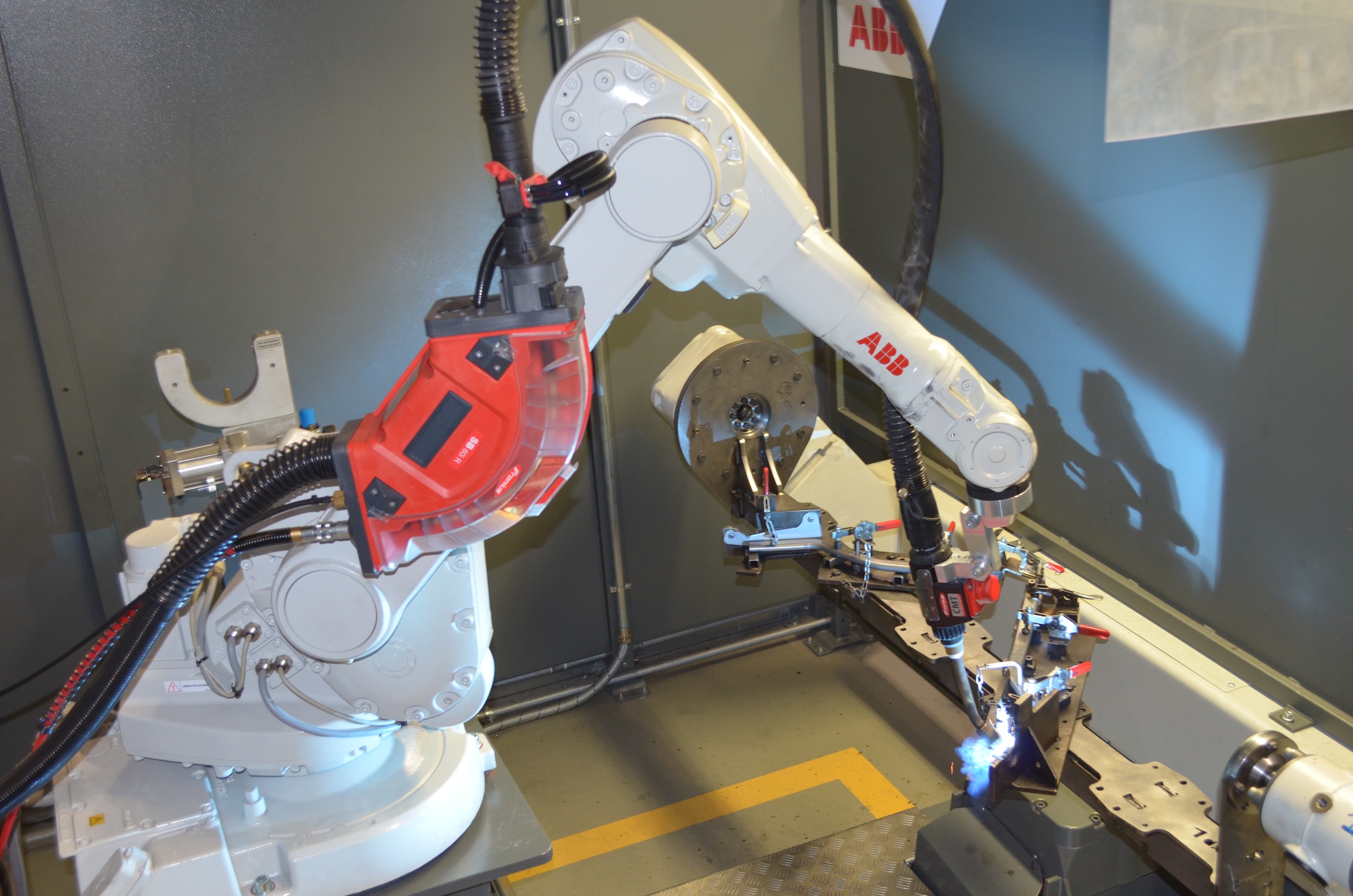
Alle koffersystemen worden door een onderaannemer geassembleerd, dus trekken we verder naar de fabriek waar al het staal wordt verwerkt, twee straten verder op hetzelfde bedrijventerrein. Hier geen geur van warme kunststoffen, maar de walmen van lasrobots en snijmachines. De stalen buizen worden door een gigantische lasersnijmachine op de juiste lengte gezet en waar nodig worden er gaten gemaakt. De 1,5 mm dikke platen van 5754 aluminium (een legering van aluminium en magnesium van Belgische makelij) worden met een andere laser zo efficiënt mogelijk versneden tot bases voor aluminium koffersets.
Het plooien en stansen van de gesneden platen is het werk van een andere onderaannemer. Voor het plooien en lassen van de stalen buizen die de kofferhouders moeten worden, zijn ingenieuze opstellingen bedacht. Aan de ene kant van het scherm legt een arbeider de metalen onderdelen in de matrijzen, aan de andere kant van het scherm last een robot alles aan mekaar.
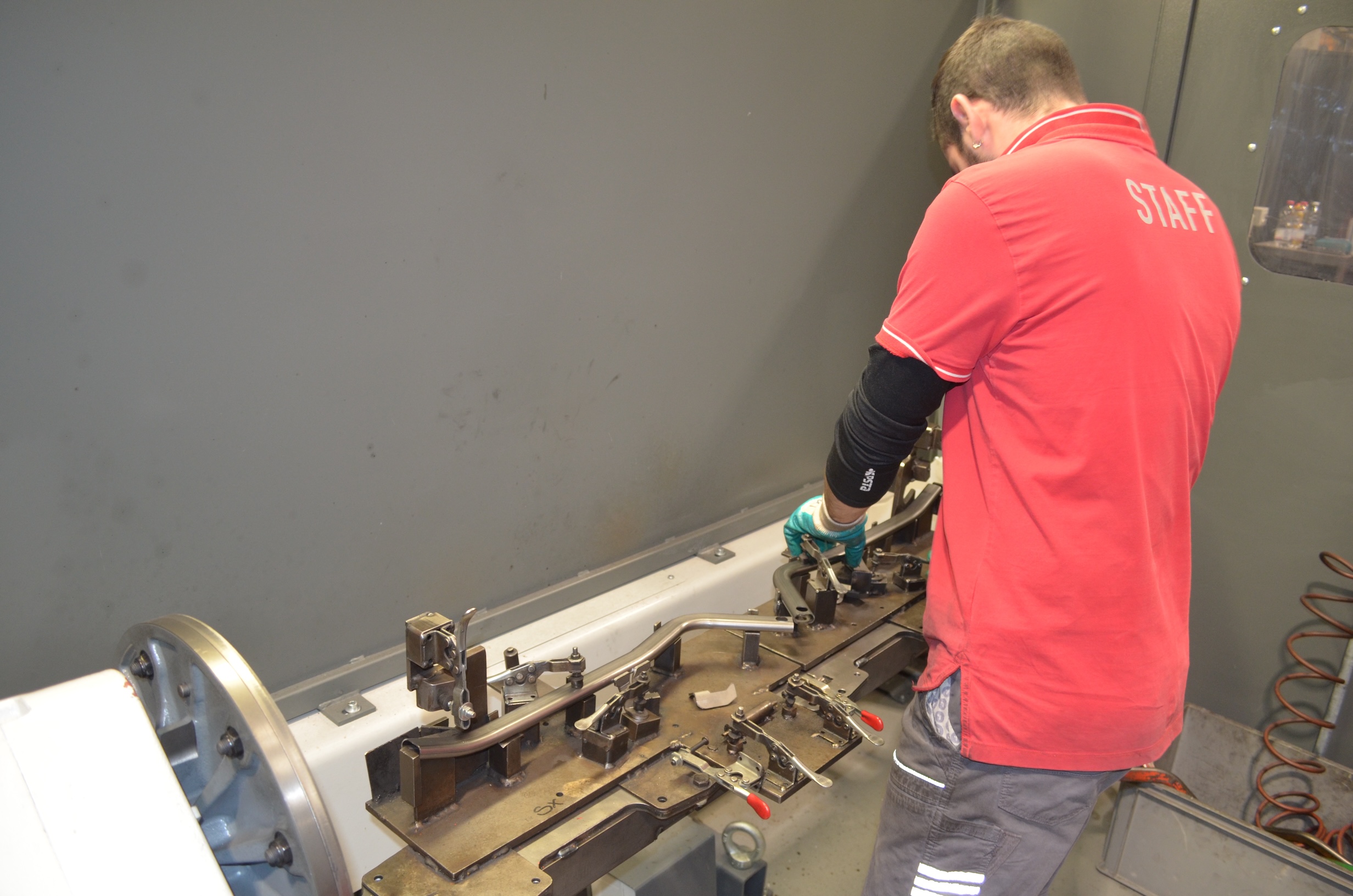
Om de minuut gaat het scherm omhoog en worden de twee werkposten gedraaid. De arbeider haalt het gelaste onderdeel uit de matrijs en legt er nieuwe stalen buisjes in terwijl de robot aan de andere kant van het scherm alweer aan het lassen is. Uiterst efficiënt, maar toch blijft het gruwelijk arbeidsintensief omdat elke kofferhouder voor elk type motor anders gevormd is.
En de puzzel wordt nog ingewikkelder omdat verschillende stappen van het productieproces worden uitbesteed, zo ook het lakwerk en de anti-corrosiebehandeling van het staal. Met andere woorden: voordat een koffer of een kofferrek vanuit het centrale magazijn verstuurd wordt, heeft het product al flink wat kilometers afgelegd tussen de Givi-fabrieken en de ateliers van onderaannemers.
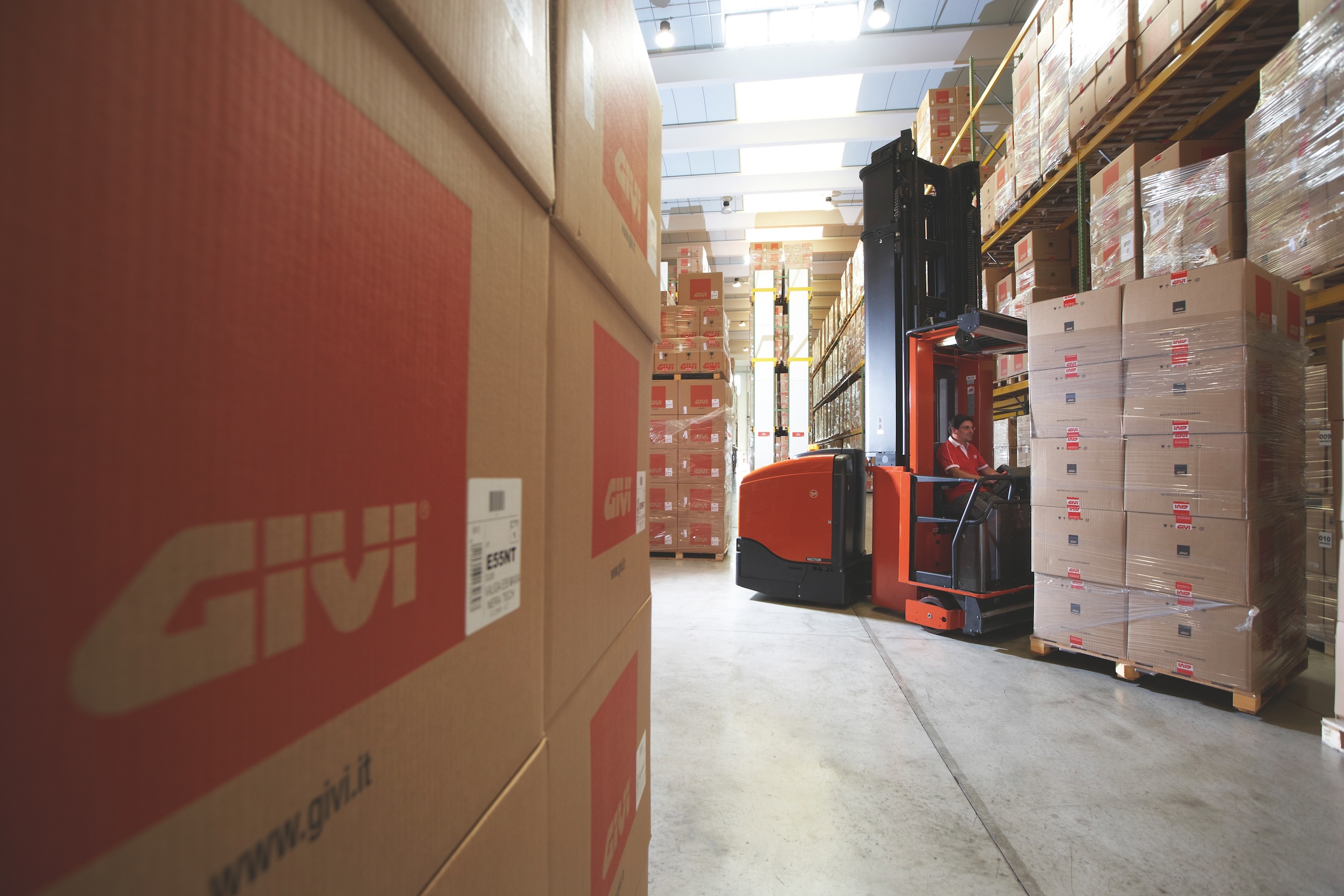
Terug in het hoofdkantoor trek ik met Deambrogi naar de ingenieurs die alle mallen op computer ontwerpen en praten we over de problematiek van de kunststoffen. Giampaolo weet dat het lastig concurreren is met fabrikanten die alles in Azië produceren. “Wij voegen een UV-block toe aan onze kunststof om de veroudering van het materiaal tegen te gaan. Dat staat slechts voor een paar procentjes van het totaal aan materiaal dat je nodig hebt om een kunststof onderdeel te maken, maar die UV-remmer is wel bijzonder duur. Sommige concurrenten voegen dat materiaal niet toe waardoor ze de prijs van hun koffers kunnen drukken. Dat weet je als consument uiteraard niet, je komt er pas achter als twee jaar na aankoop het deksel van je topkoffer helemaal vaalgrijs geworden is van de zon”, verduidelijkt de Italiaan.
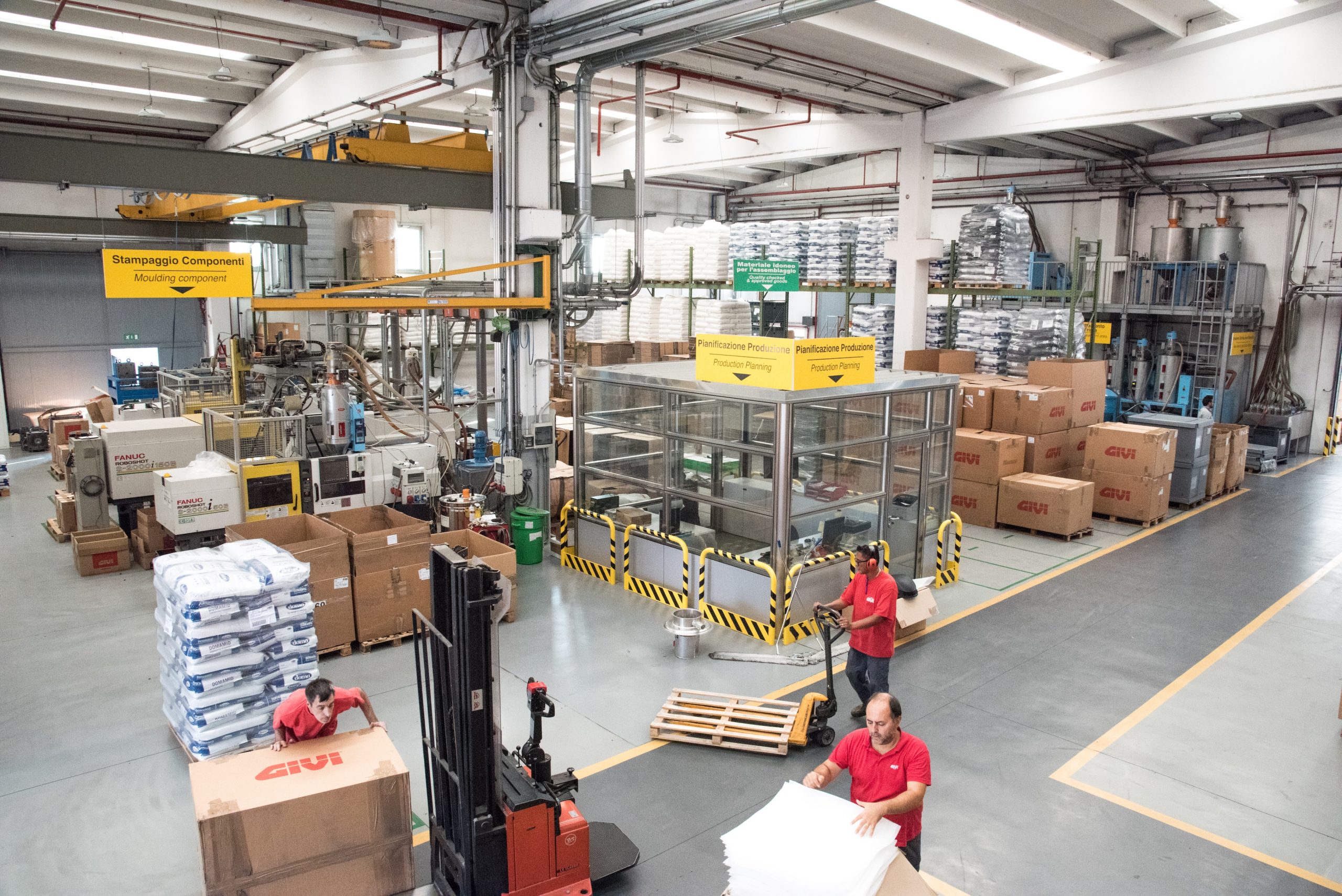
Als ik over de schouders mag meekijken van de mannen die bezig zijn met de ontwikkeling van de mallen, wordt me de complexiteit van de verwerking van kunststof pas duidelijk. Spuitgietwerk is veel meer dan wat plastickorrels verhitten en die onder druk in een mal rammen. Elke mal heeft slechts één poort van drie millimeter diameter waarlangs de vloeibare kunststof onder hoge druk wordt ingespoten. Bij de ontwikkeling van een mal moet je er rekening mee houden dat het materiaal al een beetje afgekoeld zal zijn als het zijn plaatsje vindt in het uiteinde van de mal, het punt het verst vanaf de injectiepoort. Die afstand bepaalt mee de temperatuur van de kunststof die wordt ingespoten, die kan immers variëren van 210 tot 300 graden.
Ook het soort kunststof speelt een rol, ABS wordt koeler ingespoten dan polypropyleen dat een heel hoge temperatuur vraagt. Daarenboven moet je bij de ontwikkeling van een mal rekening houden met het feit dat het onderdeel nog een beetje zal krimpen als het uit de mal komt. En dus moet je weten hoeveel het onderdeel in kwestie zal krimpen, anders krijg je die vijftig onderdelen die samen één koffer moeten vormen nooit geassembleerd. Logisch dus dat de overstap van virgin material naar gerecycleerde kunststoffen flink wat tijd in beslag neemt.
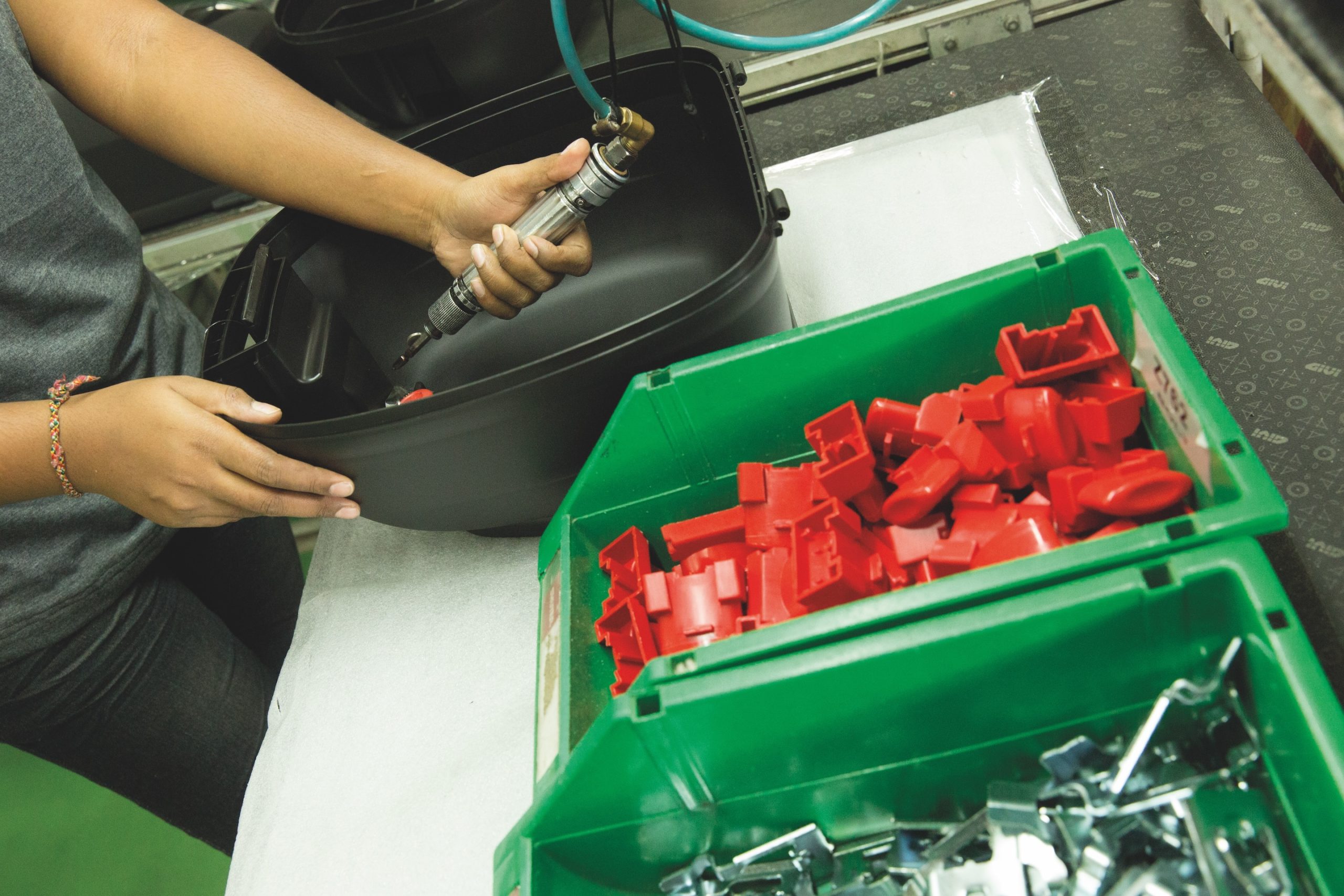
Alsof al het bovenstaande nog niet complex genoeg is, wordt Givi/Kappa dagelijks geconfronteerd met de enorme diversiteit van de motorbranche. Als fabrikant van aftermarket bagagesystemen moet je van elke nieuwe motor die op de markt komt beslissen of het de moeite waard is om voor die motor een koffersysteem te ontwikkelen of niet.
“Is dat het geval, dan zijn we afhankelijk van de goodwill van een aantal bevriende motordealers om de motor in kwestie een paar dagen in huis te halen. Dan meten we met een laser alle mogelijke bevestigingspunten van de motor op, waarna we een prototype van het bagagerek kunnen maken. Daarmee is de kous jammer genoeg niet af. Want als een motorfabrikant beslist om model X een update te gunnen die inhoudt dat bijvoorbeeld de voetsteunen voor de passagier twee centimeter lager worden gezet, dan zal die fabrikant ons daar niet van op de hoogte brengen. Dan bestaat het risico dat een klant een bestaande kofferset van ons voor dat model bestelt, maar die niet gemonteerd krijgt omdat die voetsteunen dus twee centimeter lager zijn gezet in het nieuwe modeljaar. Het resultaat? We kunnen opnieuw beginnen. Weer een motor ophalen bij een dealer. Weer opmeten met de laser. Weer matrijzen aanpassen”, omschrijft Deambrogi zijn nooit eindigende opdracht.
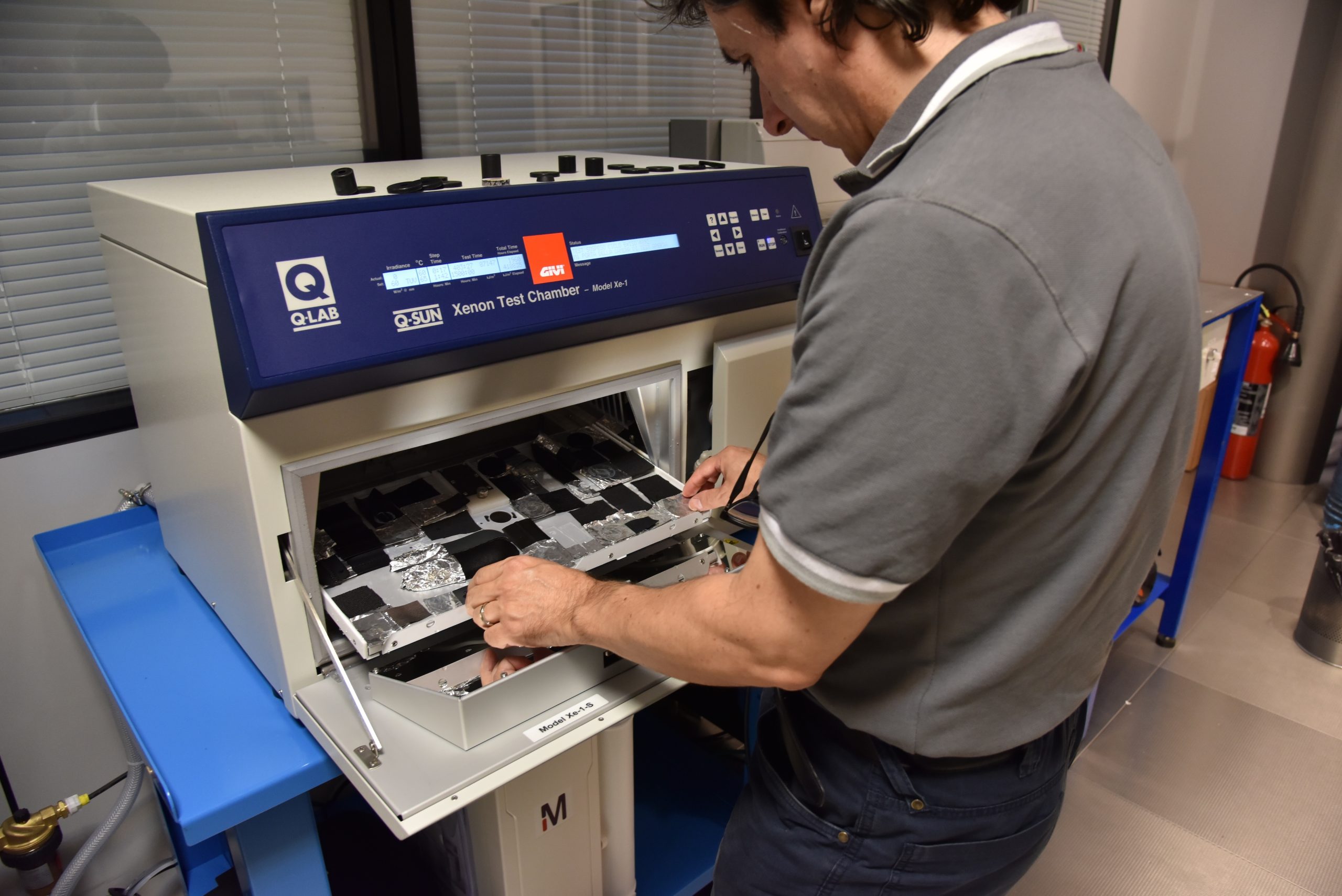
Dat Givi voor een aantal motorfabrikanten de standaard koffersets produceert, is niet meteen een hulp om die eindeloze puzzel te leggen. “Als een motorbouwer aan een nieuw model werkt en ons vraagt om de kofferset te ontwikkelen en te produceren, dan krijgen we het prototype onder heel strikte voorwaarden in huis. In een afgeschermde zone mogen enkel de medewerkers die OEM-spullen ontwikkelen (Original Equipment Manufacturer, red.) aan die motor werken en die informatie mogen ze onder geen beding delen met het andere personeel. Nee, daar wordt niet mee gelachen door de motorfabrikanten”, vertelt de manager terwijl we naar de testafdeling wandelen.
Kunststof delen worden hier belast om te kijken welke druk ze aankunnen, op een grote trilplaat kunnen Deambrogi en co. alle soorten wegdek nabootsen. “Bij de trilplaat kunnen we zowel de kracht van de klap als de frequentie van de klappen instellen. Of anders gezegd: rij je eenmalig met je motor door een grote put of rij je anderhalf uur lang over kasseien? We testen hoe de scharnieren reageren op schokken en ook de verbinding van de koffers op de houders. En we testen tot het breekt, om te voorkomen dat het breekt op jouw motor”, besluit Giampaolo Deambrogi met een knipoog.
Tekst Bart De Schampheleire • Fotografie Givi/Kappa, Bart De Schampheleire